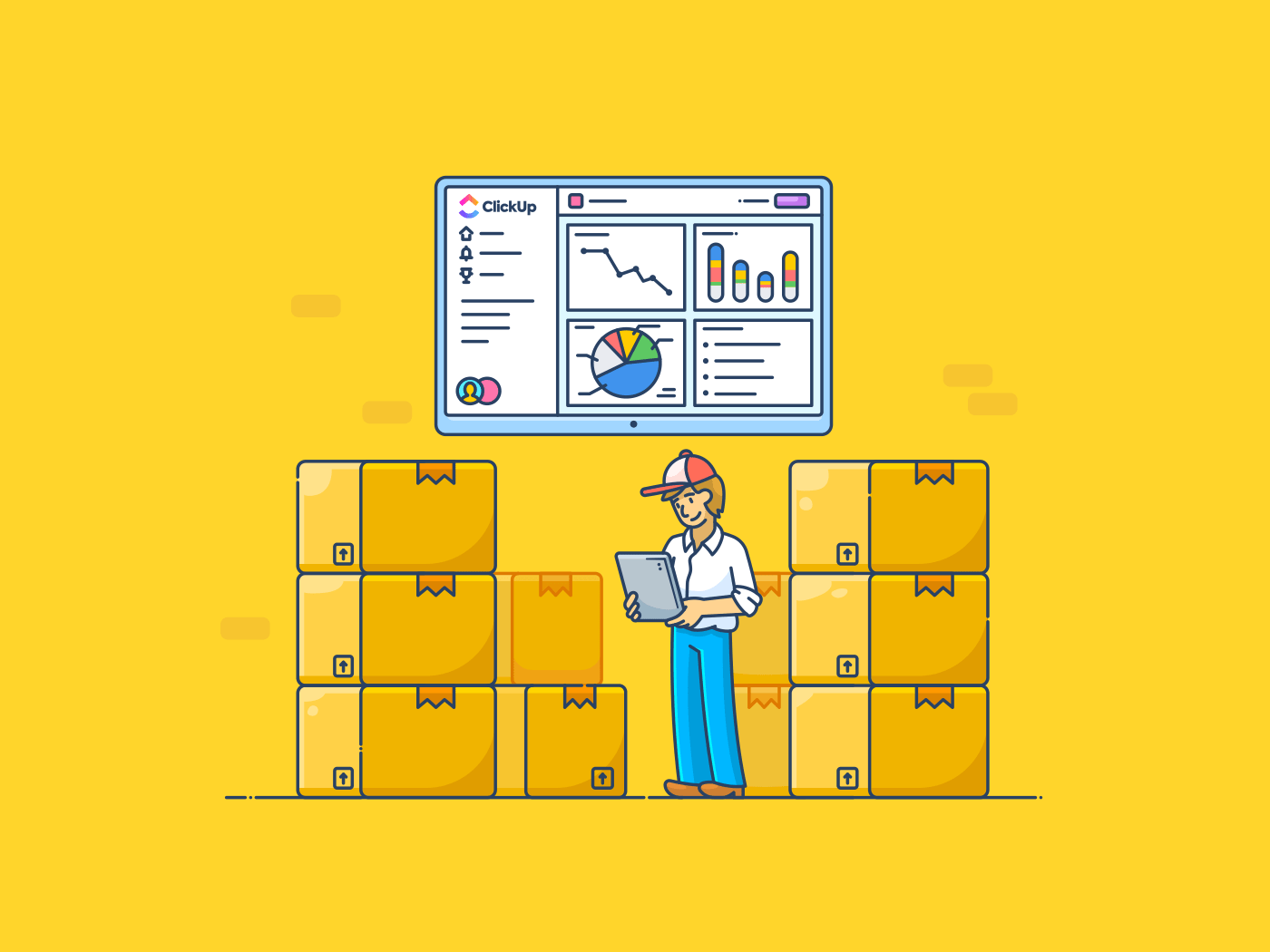
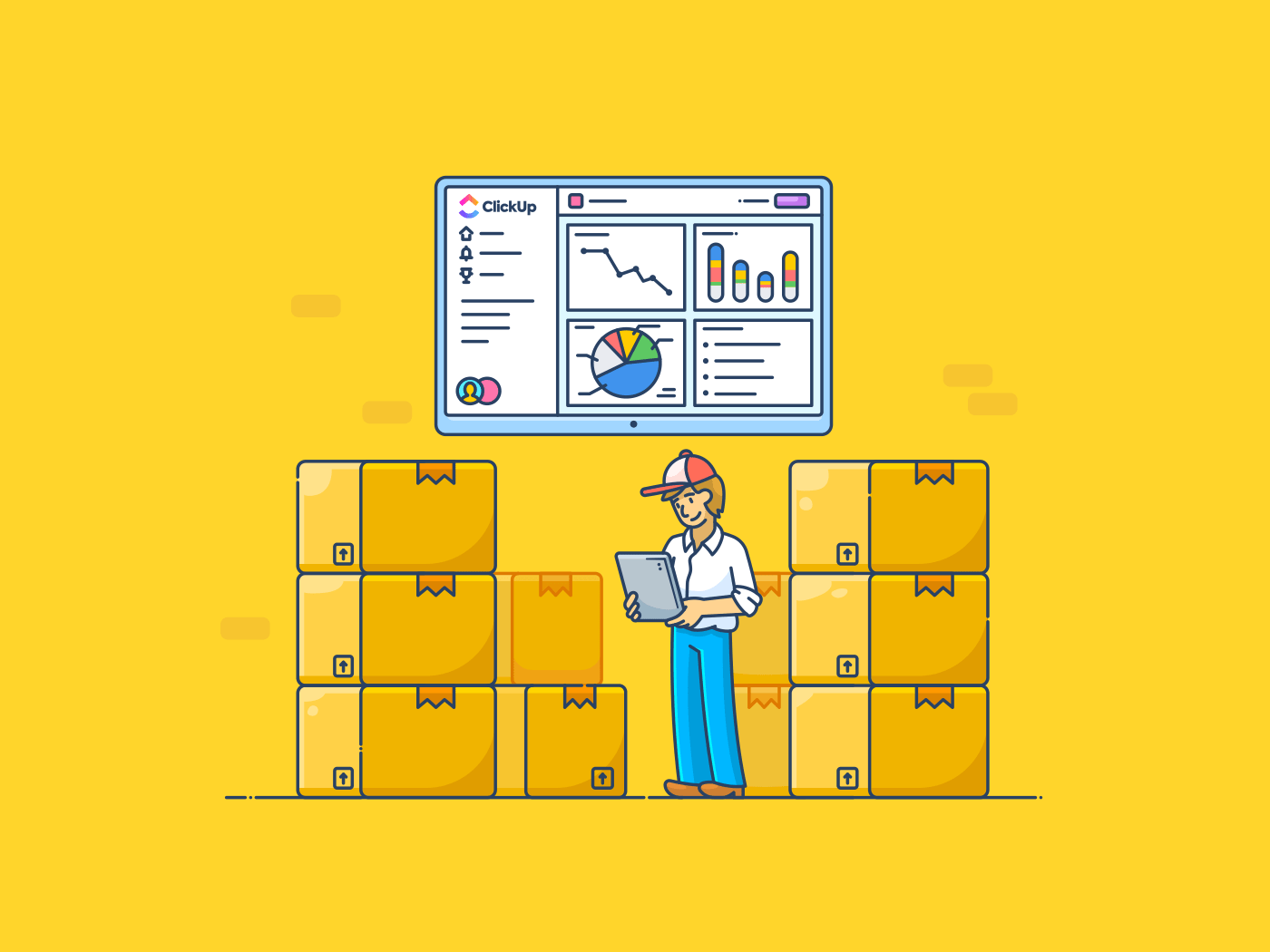
Every business, whether large or small, relies on systems and processes in order to operate smoothly.
One of these critical processes is inventory management. Ensuring that products are available when demand spikes is essential to maintaining sales momentum.
Effective inventory management drives cost savings and ensures seamless operations. It’s no wonder, therefore, that businesses are increasingly investing in inventory management systems. In fact, the market for these technologies is expected to grow at a compound annual growth rate of 9.7%, reaching $4.84 billion by 2032.
So, read on to learn how to create an inventory management system that can help your business stay ahead of the curve and meet customer demands with confidence.
What Is an Inventory Management System?
Inventory management is crucial for tracking the flow of products from suppliers to warehouses and then to customers. Its main goal is to ensure that the right items are in the right place at the right time.
A well-planned inventory management system shows inventory items in your supply chain and helps you know when to restock them.
For businesses with multiple sales channels, effective order management software provides a precise view of fulfillment and inventory operations across all channels.
For example, your system should track inventory status and update it once a Goods Received Note is signed. This ensures accuracy in downstream accounting processes.
Here are several key reasons why a structured inventory management system is essential for a business:
1. Optimizes financial management
Inventory management helps prevent unnecessary blockage of working capital by tracking inventory and highlighting products selling quickly or slowly. This allows you to prioritize high-profit items and adjust inventory levels for slower-moving products.
2. Boosts customer satisfaction
Poor inventory organization can result in slow deliveries and frustrated customers. Effective inventory management speeds up shipping by streamlining item storage and movement, reducing the risk of order cancellations or stockouts that disappoint customers.
Advanced inventory management software provides complete visibility into each item’s location and movement. This is crucial for efficient distribution, especially for businesses with multiple locations.
3. Enhances automation and analytics
Automated tools allow for the systematic tracking and analysis of inventory data. AI inventory management software collects real-time information on stock levels, movement rates, and more. This data reveals sales patterns, identifies areas for improvement, and helps automate processes such as estimating shipping times.Â
Additionally, project management resources can enhance these improvements by effectively allocating tasks and monitoring progress, ensuring your inventory system runs efficiently.
4. Improves inventory organization
Your order fulfillment speed and customer satisfaction depend on how quickly employees can find and ship items. By organizing and managing inventory effectively, you can identify popular items, frequently paired products, and those with slow turnover and arrange stock more efficiently.
How to Create an Inventory Management System: A Step-by-Step Process
Efficient inventory management can significantly impact your business, especially if you’re scaling up.
Here’s a step-by-step process to create a robust inventory management system:
1. Planning and preparation
Designing and developing even a simple inventory management system can be complex, so thorough planning and preparation are essential. Consider the following key factors:
- Integrations: Identify which systems need to connect with your inventory management application, such as ERPs, CRMs, WMS (warehouse management systems), accounting software, purchase order management, and point-of-sale systems. WMS specifically helps by optimizing warehouse operations, improving inventory tracking and inventory reports, and ensuring accurate order fulfillment
- System type: Decide whether you need a purely software-based system or one that includes hardware components
- Data migration: Plan how to transfer data from existing static inventory records to a dynamic database
💡 Pro Tip: Use ClickUp Whiteboards to convert your team’s ideas into detailed action plans in a single, organized space. They enable real-time collaboration and visualization of tasks, making it easier to assign responsibilities, track progress, and keep everyone aligned.
2. Defining your goals and requirements
The second step involves defining the goals and requirements for your inventory management system. Begin by specifying the essential features your system must support. For instance, if your point of sale uses RFID technology, your inventory management system should be compatible with this method for recording sales.
Identify the non-negotiable features you need, such as integration of sales and operations processes or automated stock alerts. Make sure that these requirements align with your business objectives.
For example, if reducing overstocking during peak sales seasons is a priority, robust inventory forecasting capabilities should be an essential requirement. By clearly defining requirements, you ensure that the system you implement will effectively meet your business needs and support your strategic objectives.
ClickUp Goals helps you stay focused on achieving your objectives with clear timelines, measurable targets, and automatic progress tracking.
When setting up your inventory management system, ClickUp Goals can streamline the process by allowing you to define specific goals—whether numerical, monetary, true/false, or task-based—that align with your needs, such as improving stock accuracy or hitting sales targets.
With automatic progress updates and well-defined timelines, ClickUp Goals ensures you stay on track, aligning your inventory management system setup with strategic priorities and enhancing overall efficiency.
3. Conducting market research
With your requirements and goals defined, the third step is to conduct market research to identify available software and tools. Focus on the most popular inventory management systems used by businesses similar in scale to yours.
During your research, consider whether additional software or tools, such as procurement or logistics software, might be necessary to enhance your system’s capabilities. Compare different options, including the costs of hiring developers versus using pre-built solutions, to determine the most cost-effective and suitable choice for your needs.
💡 Pro Tip: Organize the information you collect into a structured Table view in ClickUp. Create separate tables and add custom fields to evaluate key features, pricing, and integration options of different inventory management systems. This way, you can efficiently analyze and compare options to select the most suitable and cost-effective solution for your business needs.
4. System design
System design is a crucial phase in developing an inventory management system. In this stage, you’ll work with your development team to plan and design the modules, components, interfaces, and interactions that will comprise your system.
Begin with a high-level design to outline the overall structure and flow of the system, followed by a more detailed low-level design that addresses specific functionalities and components. Your developers will draft these designs and establish a suitable architecture using tools such as flowcharts, UML diagrams, and wireframes. On this note, use ClickUp Mind Maps to outline the basic structure of your system and expand on the details. This will help you visualize and organize the design process, ensuring a comprehensive and aligned system architecture.
Bonus Tip: Use inventory templates to speed up the design and setup of your system. This way, you can quickly implement a functional structure tailored to your needs without starting from scratch.
5. Architecture and design
The architecture and design phase is crucial for establishing a robust foundation for your inventory management system (IMS). This step involves defining the overall structure and components of your system, which typically follows a client-server model.
The architecture consists of several key components:
- Database: The backbone of your inventory management system, the database stores critical product information such as SKUs, names, descriptions, quantities, locations, and prices. This central repository ensures data consistency and accessibility across the system
- Business logic: This component handles the core functionalities of the system, including stock-level calculations, order processing, and demand forecasting. It ensures that the system operates efficiently and accurately according to the defined rules and processes
- Integration layer: This layer facilitates communication between the IMS and other systems, such as point of sale (POS) systems, enterprise resource planning (ERP) software, shipping systems, and order management tools. It enables seamless data exchange and integration across various applications
- User interface (UI): The UI provides a user-friendly interface for interacting with the system. It allows users to input, retrieve, and analyze data efficiently, ensuring a smooth and intuitive user experience
- Reporting module: This component generates essential reports on stock turnover, sales analysis, inventory levels, and other vital metrics. It helps in tracking performance and making data-driven decisions
By carefully designing each component, you create a well-structured inventory management system that meets your business needs and supports effective inventory management processes.
6. Choosing the right technology stack
Once the architecture of your inventory management system is established, the next step is to select a technology stack that provides the necessary tools and frameworks to build and operate the software. This tech stack will enable developers to create a system that aligns with your requirements and goals.
Begin by choosing the programming languages that will be used, such as PHP, Swift, Python, or others, based on the system’s needs and your team’s expertise.
Next, select the appropriate databases, platforms, and frameworks that will support the system’s functionality and scalability. Additionally, identify relevant libraries to enhance the development process and add necessary features.
When selecting your tech stack, it is crucial to consider factors such as your budget, timeline, and end goals. Additionally, ensure that the chosen tools and components are compatible with each other and any existing systems to facilitate smooth integration and future scalability.
7. Development process
The development process for your inventory management system (IMS) begins once you have finalized the tech stack, architecture, requirements, and system design. This phase is important, as it transforms your planning into a functional system, involving several critical steps:
- Coding: Developers write the code using the chosen programming languages. This step involves creating the system’s logic, implementing database interactions, and ensuring core functionalities are developed correctly
- Database design and implementation: Developers will design and implement the database schema, defining tables, relationships, and indexes. They will populate the database with initial or dummy data to facilitate testing and validation
- UI development: Using HTML, CSS, and JavaScript, developers will build the user interface, ensuring it is intuitive and aligns with the requirements for data input, retrieval, and analysis
- Testing: Comprehensive testing is conducted, including integration, unit, and system tests, to identify and resolve any errors or glitches. This ensures the system functions as intended and meets all outlined requirements
- API development: If your inventory management system needs to integrate with other systems, developers will create and implement the necessary APIs to enable seamless data exchange and functionality
Effective management is crucial throughout the development process. Coordinating tasks, managing resources, and ensuring alignment with goals and deadlines are key to a successful implementation,
8. Integration and migration
In this phase, developers link the inventory management system with other enterprise systems or software to enable smooth communication between them.
This integration allows data to flow freely, providing more accurate insights into sales predictions and key performance indicators (KPIs). For example, connecting the inventory management system with accounting and logistics systems improves overall efficiency and data accuracy.
After testing the inventory management system and confirming the database’s performance, data migration takes place. If the database files are correctly formatted, migration is usually automated, ensuring a seamless data transfer to the new system.
9. User training
For any software to be truly effective, users must know how to maximize its potential. The next step involves informing the relevant departments about the upcoming implementation and ensuring that staff members are prepared to undergo training.
Here are several ways to plan and facilitate hands-on training:
- Provide staff with essential documentation, user manuals, and resources to help them understand the software’s functionality.
- Arrange webinars or seminars to demonstrate the software’s capabilities.
- Offer live training sessions that cover the software’s features, troubleshooting methods, and other critical aspects.
Use ClickUp Clips to create quick screen recordings for training videos about your inventory management system. Instead of lengthy written instructions or extended discussions, record your screen with ClickUp Clips to effectively demonstrate the system setup.
Additionally, use ClickUp Docs to create a comprehensive user manual or instruction guide. With ClickUp Docs, you can consolidate your notes and instructions, utilizing features like nested pages, styling options, and templates to create a well-organized and accessible training resource.
If you are wondering how to create an inventory system for a small business, focus on simplicity, ease of use, and cost-effectiveness. Opt for a system that doesn’t require extensive training or complex integration. Prioritize features like barcode scanning, low stock alerts, and real-time inventory tracking, which can help you manage your stock efficiently without overwhelming your team.
10. Launch and maintenance
In the final step, you will launch the custom inventory management software across all relevant departments. Establishing a software maintenance and update schedule is also crucial to keeping the system running optimally.
Additionally, plan for the maintenance of connected hardware components, like RFID systems, to ensure their seamless operation.
Managing Inventory With ClickUp: Top Features to Explore
ClickUp is an all-in-one productivity tool that offers a variety of features and customizable templates that can greatly enhance your inventory management processes. Instead of building a complicated tech stack, you can use ClickUp as an all-in-one solution for inventory management, productivity, and team collaboration.
Here’s how to create an inventory management system with ClickUp:
ClickUp’s Table View helps you streamline inventory management by organizing product data in a highly structured and customizable format.
With its help, you can set up columns to show critical product information, such as SKU numbers, quantities, and logistics attributes, and use custom statuses and flags to track different criteria.
Additionally, with ClickUp Dashboards, you can easily view your inventory information through a customizable interface, which prominently displays all crucial data. With custom statuses and reporting tools, you can efficiently track stock movement and availability.
Set up quick access to important data via Dashboard widgets and automate manual inventory-related tasks, such as low stock notifications. With ClickUp Automations you can set up task triggers to automate recurring activities (like supplies or dispatches), and inventory replenishment processes. This integration enhances your planning and preparation, ensuring a more streamlined approach to managing your inventory system.
ClickUp also gives you an integrated AI assistant, ClickUp Brain, that helps you save time and effort in many ways. It can analyze data and generate insights to help you make better decisions, create task updates, and summarize meeting notes to suggest action points for you. The AI Writer can also quickly generate copy for contracts, SLAs, RFQ emails, and more, so you can use your time for more strategic work.
ClickUp’s Inventory Management Template helps you efficiently organize and track your inventory. When setting up an inventory management system, it helps you keep tabs on inventory levels and ensure stock availability is consistently up-to-date. It is designed to monitor stock movements and track changes in inventory costs.
Here’s how it helps:
- Monitor current stock quantities to ensure you maintain appropriate inventory levels
- Quickly assess available inventory to streamline order fulfillment and prevent overstocking or stockouts
- Observe inventory flow and usage trends for better decision-making and resource allocation
- Stay informed about fluctuations in inventory costs to manage your budget effectively
On this note, using purchase order templates can streamline your ordering process, making it easier to track and manage inventory effectively. Make sure to integrate these templates to enhance efficiency as you launch and maintain your system.
ClickUp’s Inventory Template simplifies the setup of an inventory management system by streamlining both integration and migration processes. It provides a structured framework that offers smooth data transfer and reduces human errors, ensuring accurate inventory records from the outset. This efficiency in migration helps maintain data integrity and supports effective system setup.
The template enhances overall inventory management with its various views, including inventory, vendor location, order form, and vendor lists. These views offer comprehensive oversight and enable detailed tracking of stock levels.
Custom attributes like Requested By, Reorder Point, and Cost per Unit provide actionable insights, helping you prevent issues like overstocking and overspending while making informed decisions.
Take Control of Your Inventory System with ClickUp
Effective inventory management is vital for maintaining accurate stock levels, meeting customer demands, and avoiding costly errors like overselling or overstocking. A good system ensures full visibility of your inventory, which leads to better decisions and improved efficiency.
ClickUp offers a versatile solution that simplifies inventory management. With its comprehensive range of templates and features, you can build a robust inventory management system tailored to your business needs—all conveniently available in one place.
Now you know how to create an inventory system with ClickUp, so why wait? Sign up on ClickUp now and streamline your inventory management effortlessly.