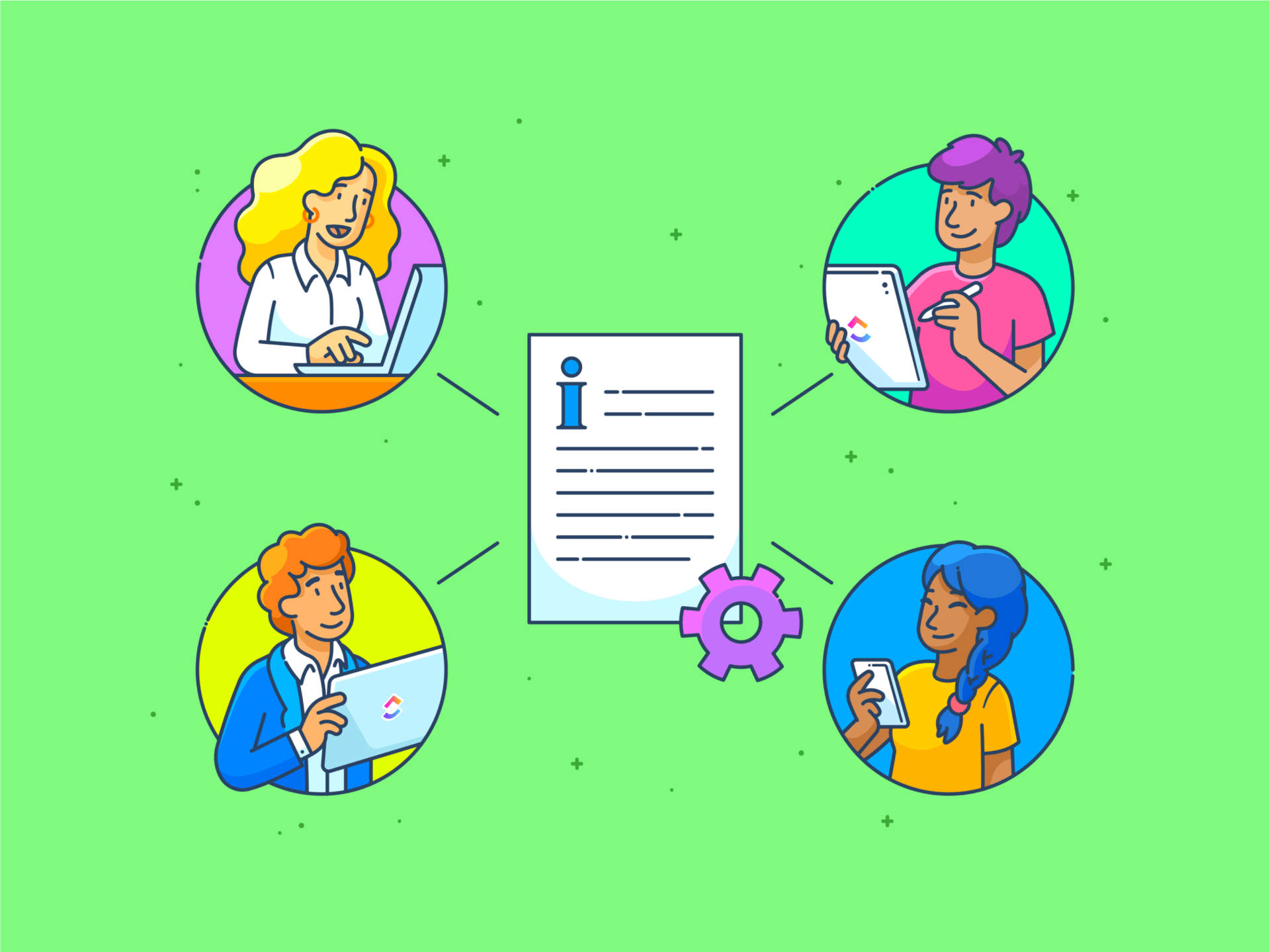
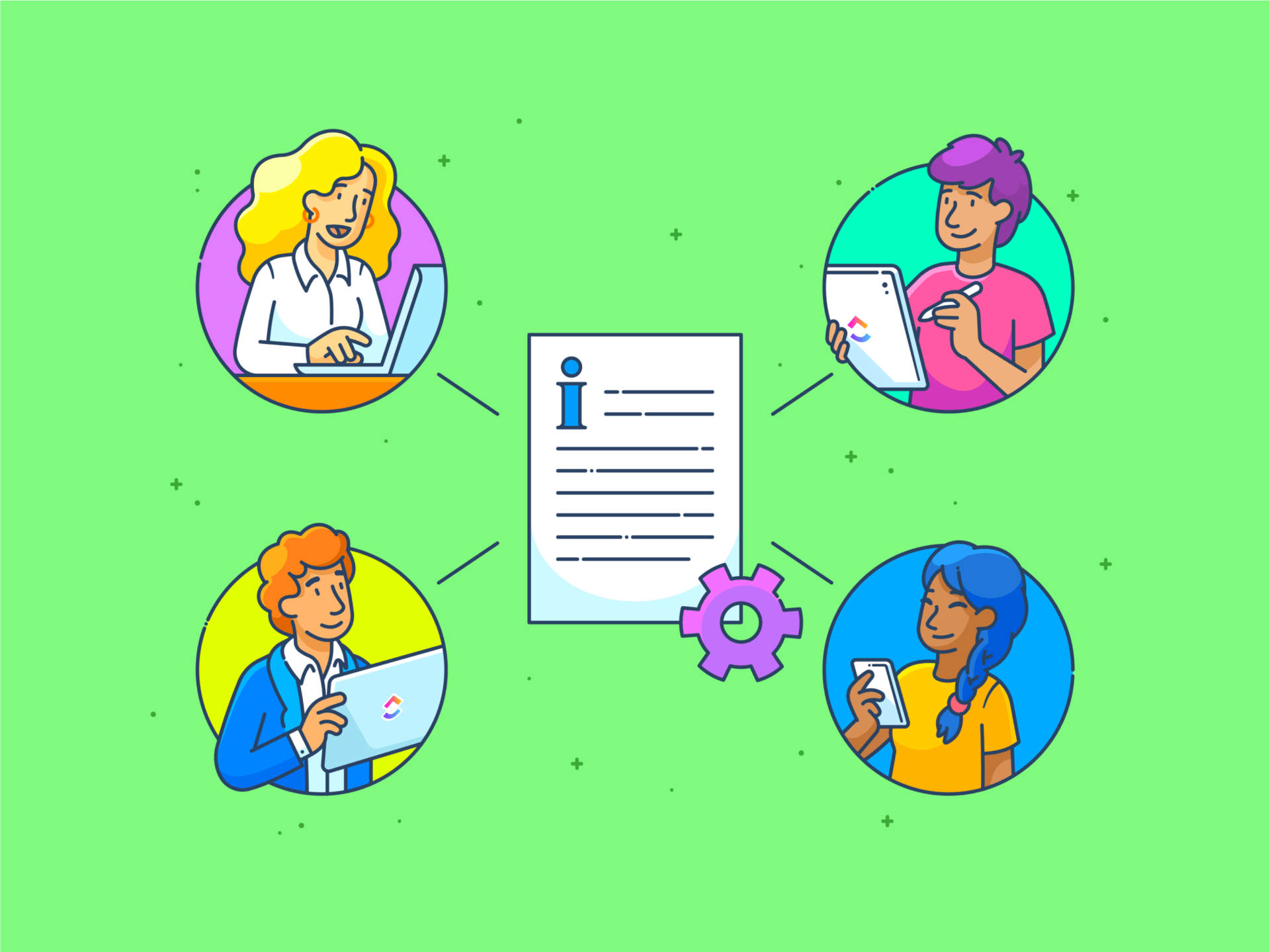
Success in business often hinges on clarity and consistency in communication. That’s where understanding work instruction vs. SOP becomes essential. These two tools serve as the foundation for efficient operations, ensuring tasks are completed accurately, and processes run smoothly.
While work instructions focus on detailed, step-by-step guidance for individual tasks, SOPs provide a high-level framework for broader workflows. In this blog, we’ll break down their differences, explore their practical uses, and show how they can elevate your organization’s performance.
Understanding Work Instructions
Work instructions are precise, step-by-step guides designed to help employees complete tasks efficiently and accurately. These documents focus on specific tasks within a process, ensuring consistency and quality in operations.
They are typically tailored to particular tasks and provide actionable details that enable employees to execute their responsibilities effectively.
Who needs work instructions?
- Employees performing repetitive tasks requiring clear, step-by-step instructions
- New employees who need structured guidance to complete tasks
- Teams dealing with complex tasks where detailed instructions reduce errors
- Industries where adherence to safety protocols and industry regulations is critical
Types of work instructions
- Text-based instructions: Traditional formats with written, detailed steps
- Visual instructions: Diagrams, flowcharts, or images for visual clarity
- Video instructions: Tutorials demonstrating task completion in real-time
- Interactive instructions: Digital formats with embedded simulations or guides
Key components included in work instructions
- Specific procedure: Clear, actionable steps for the task
- Personnel involved: Roles and responsibilities for each step
- Tools or materials required: Necessary resources for task execution
- Safety protocols: Measures to ensure compliance and minimize risks
- Desired outcome: Defined results to achieve consistency
By leveraging work instructions, businesses can streamline operations and ensure consistent results while enabling employees to perform tasks precisely.
Read More: How to Write Procedures and Policies
Understanding Standard Operating Procedures (SOPs)
Standard operating procedures (SOPs) are detailed documents outlining the consistent processes required to carry out specific business operations.
They provide a high-level framework to ensure tasks are completed correctly, meet organizational standards, and adhere to industry regulations. SOPs are integral to achieving quality control, ensuring compliance, and maintaining efficiency across teams.
Who needs a standard operating procedure (SOP)?
- Organizations in regulated industries like healthcare or manufacturing to ensure compliance
- Teams managing cross-functional or interdepartmental workflows
- Businesses scaling operations to maintain quality standards
- Leadership aiming to define processes for new employees and strategic initiatives
Also Read: The Ultimate Guide to Process Standardization
Types of SOPs
- Linear SOPs: Sequential steps ideal for straightforward processes
- Decision-based SOPs: Flowcharts guiding users through decision points
- Safety-oriented SOPs: Focused on personal protective equipment and hazard mitigation
- Cross-functional SOPs: Covering processes involving multiple teams
Key components included in SOPs
- Purpose: Clear explanation of the SOP’s significance
- Application: Teams, roles, or scenarios the SOP addresses
- Steps and procedures: Detailed yet flexible guidelines for tasks
- Accountability measures: Metrics for tracking compliance and performance
- Regulatory requirements: Specific standards ensuring adherence to industry laws
SOPs are essential for businesses looking to maintain a well-oiled machine by defining processes and ensuring consistent implementation. Properly crafted SOPs improve efficiency, reduce errors, and ensure quality assurance across operations.
Work Instructions vs. SOPs: Key Differences
Understanding the distinctions between work instructions and standard operating procedures (SOPs) is essential for effective documentation and process management. While both aim to standardize operations, their scope, format, and application vary significantly.
Comparison of work instructions and SOPs
Aspect | Work Instructions | Standard Operating Procedures (SOPs) |
Purpose | Provide step-by-step guidance for completing specific tasks | Offer a high-level overview of broader processes or workflows |
Focus | Granular details for task execution | Ensuring compliance with industry regulations and quality standards |
Best use cases | Training new employees or ensuring repetitive tasks are completed consistently | Streamlining operations across departments or teams |
Application | Used when precision and clarity in individual tasks are critical | Emphasize consistency and accountability in broader business processes |
Scope of the task | For isolated, detailed tasks | For workflows involving interconnected tasks or teams |
Audience | Ideal for employees with limited prior experience | Better suited for managers and cross-functional teams ensuring compliance |
Compliance requirements | Complement SOPs by providing actionable details for critical tasks | Rely on SOPs to meet legal standards in industries with strict regulations |
Flexibility | Demand strict adherence to specific steps | Allow some procedural adaptability while ensuring consistency |
Documentation integration | Deliver precise task details within a broader process | Provide the framework for comprehensive workflows and reference work instructions as needed |
When to use | For single, well-defined tasks (e.g., machine operation steps) | For processes involving multiple tasks or teams (e.g., quality assurance workflows) |
Practical examples highlighting differences
- Work instructions example: In a food production factory, a work instruction outlines the exact steps for operating a dough mixer. It includes precise measurements for ingredients, mixer settings (e.g., speed and time), and cleaning protocols after use. This ensures consistent dough quality regardless of who operates the equipment
- SOP example: In the same factory, an SOP governs the broader baking process. It includes steps like dough preparation, baking temperatures, quality inspections, and packaging procedures. This ensures every batch meets the company’s quality standards and regulatory requirements
- Hybrid use case: In an automotive assembly plant, an SOP for vehicle assembly might refer to specific work instructions for installing a car door. The SOP covers the overall assembly process, while the work instruction provides detailed guidance on tools, torque specifications, and alignment checks for door installation
Implementing Work Instructions and SOPs
Effectively implementing work instructions and SOPs is crucial for streamlining operations, ensuring consistency, and maintaining quality control. By adhering to best practices and utilizing the right tools, businesses can optimize the creation, management, and usage of these documents.
Best practices for creating work instructions and SOPs
- Start with clear objectives: Define the purpose of the document and its intended outcome. This ensures both work instructions and SOPs address specific needs effectively
- Keep it simple and concise: Use clear, straightforward language. Avoid unnecessary jargon and focus on providing actionable details that are easy to follow
- Involve stakeholders: Collaborate with those directly responsible for the tasks or processes. This improves accuracy and ensures the instructions are practical and relevant
- Use visuals: Incorporate flowcharts, diagrams, and images to enhance clarity, especially for complex tasks
đŸ‘€Did You Know? According to ScienceDirect, adding the right visuals to written instructions makes it easier for people to understand and remember what they’ve learned.
- Standardize formats: Create reusable templates to maintain consistency and simplify updates. This ensures documents are easy to read and follow across teams
- Regularly review and update: Schedule periodic reviews to keep documentation accurate and aligned with current workflows and compliance requirements
- Test for usability: Have the intended users test the documents to ensure clarity and effectiveness
- Provide training: Educate teams on how to use SOPs efficiently to maximize their value
Using tools to manage SOPs and work instructions
Modern tools like ClickUp make managing these documents easier by offering features like templates, task tracking, and collaborative editing. For example, the ClickUp SOP Template simplifies creating and maintaining standardized procedures.
Advantages of the SOP template:
- Fast setup for documentation
- Consistent formatting across processes
- Customizable for various business needs
In addition to templates, ClickUp provides robust features for managing work instructions and SOPs efficiently:
Organize and track actionable steps
ClickUp Tasks will help you streamline your task management. Break down SOPs into smaller, actionable tasks that can be assigned to specific team members.
Real-time tracking ensures that each step of the process is completed on schedule, minimizing bottlenecks. Tasks can also include due dates, priority levels, and checklists for added clarity.
Collaborate and refine documents in real time
Create, store, and collaborate on SOPs and work instructions directly using ClickUp Docs. These documents support rich text formatting, hyperlinks, and integrations with tasks, making them an all-in-one solution for documentation. Real-time collaboration ensures everyone stays aligned, even in distributed teams.
Additional templates like the ClickUp Process and Procedures Template and ClickUp Work To-Do Template complement these features, offering a streamlined way to organize and manage processes.
By combining templates, task management, and document collaboration, ClickUp empowers teams to create and maintain SOPs and work instructions with greater efficiency and accuracy.
Benefits of digital platforms for SOP and work instruction management
- Efficient collaboration: Team members can work together simultaneously, making updates faster and reducing delays. This is especially beneficial for remote or hybrid teams
- Centralized integration: Integrating documentation with tools like project management systems, communication platforms, and cloud storage keeps all processes connected and accessible
- Streamlined workflows: Automations help ensure tasks are completed in sequence, reminders are sent, and approvals are tracked. This reduces errors and improves efficiency
- Version control: Maintaining an archive of document changes helps teams track updates and ensure compliance
- Customizable workflows: Teams can adapt processes to fit specific organizational needs, from document approvals to task tracking and updates
Using the right tools like ClickUp allows businesses to effectively manage their work instructions and SOPs, ensuring processes remain consistent, compliant, and efficient without manual bottlenecks. This results in higher productivity, better quality, and a seamless workflow across teams.
Practical Applications of Work Instructions and SOPs
The analysis of work instruction vs. SOP becomes particularly meaningful when applied to real-world scenarios. Together, they help industries maintain consistency, improve safety, and achieve operational excellence. Here’s how they make an impact in various fields:
Role in manufacturing industries
- Work instructions detail precise steps for operating machinery, performing quality checks, and assembling components.
- SOPs define broader processes like production planning, material handling, and equipment maintenance schedules.
- Both ensure compliance with industry regulations, minimize errors, and improve efficiency on the production floor.
Example: In an assembly line, SOPs guide overall workflow coordination, while work instructions specify tasks like calibrating machines or inspecting product quality.
Importance in operations
- SOPs provide a structured framework for cross-functional workflows, ensuring tasks are completed consistently.
- Work instructions focus on specific operational tasks like data entry, equipment setup, or client onboarding.
- Together, they reduce delays, enhance productivity, and maintain quality across departments.
Example: In a logistics operation, an SOP ensures the seamless flow of goods, while work instructions guide employees on packaging procedures or inventory checks.
Health and safety applications
- SOPs outline critical safety protocols, hazard response procedures, and compliance measures.
- Work instructions detail the use of personal protective equipment (PPE), machine safety checks, and emergency drills.
- Their integration reduces workplace risks, ensures compliance with safety regulations, and promotes a culture of safety.
Example: In a chemical plant, an SOP covers the overall hazardous material handling process, while work instructions specify steps for operating safety equipment like eyewash stations or ventilation systems
Relevance in inventory management
- SOPs standardize inventory workflows, including stock audits, order fulfillment, and replenishment schedules.
- Work instructions guide employees on using inventory software, conducting cycle counts, or processing returns.
- They help minimize stock discrepancies, improve accuracy, and streamline inventory tracking.
Example: In a warehouse, an SOP governs inventory restocking procedures, while work instructions focus on barcode scanning or stock placement methods.
Work instructions and SOPs, when implemented effectively, enhance operational clarity and efficiency across industries. Their adaptability ensures they meet the specific needs of diverse workflows, making them invaluable tools for modern businesses.
Bonus: AI SOP Generators!
Unlocking the Power of Work Instructions and SOPs
Understanding the role of work instruction vs. SOP is key to fostering efficiency and consistency in any organization. By aligning these tools with their unique purposes, businesses can reduce errors, enhance compliance, and streamline operations.
Whether it’s guiding employees through detailed tasks or managing broader workflows, work instructions and SOPs form the backbone of a high-performing workplace.
Ready to simplify your processes and boost productivity? Sign up for ClickUp today and take the first step toward smarter workflow management.
Frequently Asked Questions(FAQs)
Q. Is an SOP the same as a policy?
A. No. A policy outlines broad rules or principles, while an SOP provides step-by-step instructions for carrying out specific processes.
Q. Can work instructions be used in place of an SOP?
A. Not effectively. Work instructions detail how to perform individual tasks. An SOP covers the entire process, with work instructions often supporting rather than replacing it.
Q. Who is responsible for creating SOPs and work instructions?
A. Usually, managers or subject matter experts develop these documents, often with input from the employees who perform the tasks.
Q. Are SOPs and work instructions necessary for all businesses?
A. They’re not mandatory for every company, but most organizations benefit from them to ensure consistency, improve efficiency, and maintain compliance.
Q. Clarify the difference between policy, SOP, and work instruction
A. A policy sets general principles, an SOP outlines the procedures to follow, and a work instruction gives detailed guidance for completing individual tasks within that procedure.