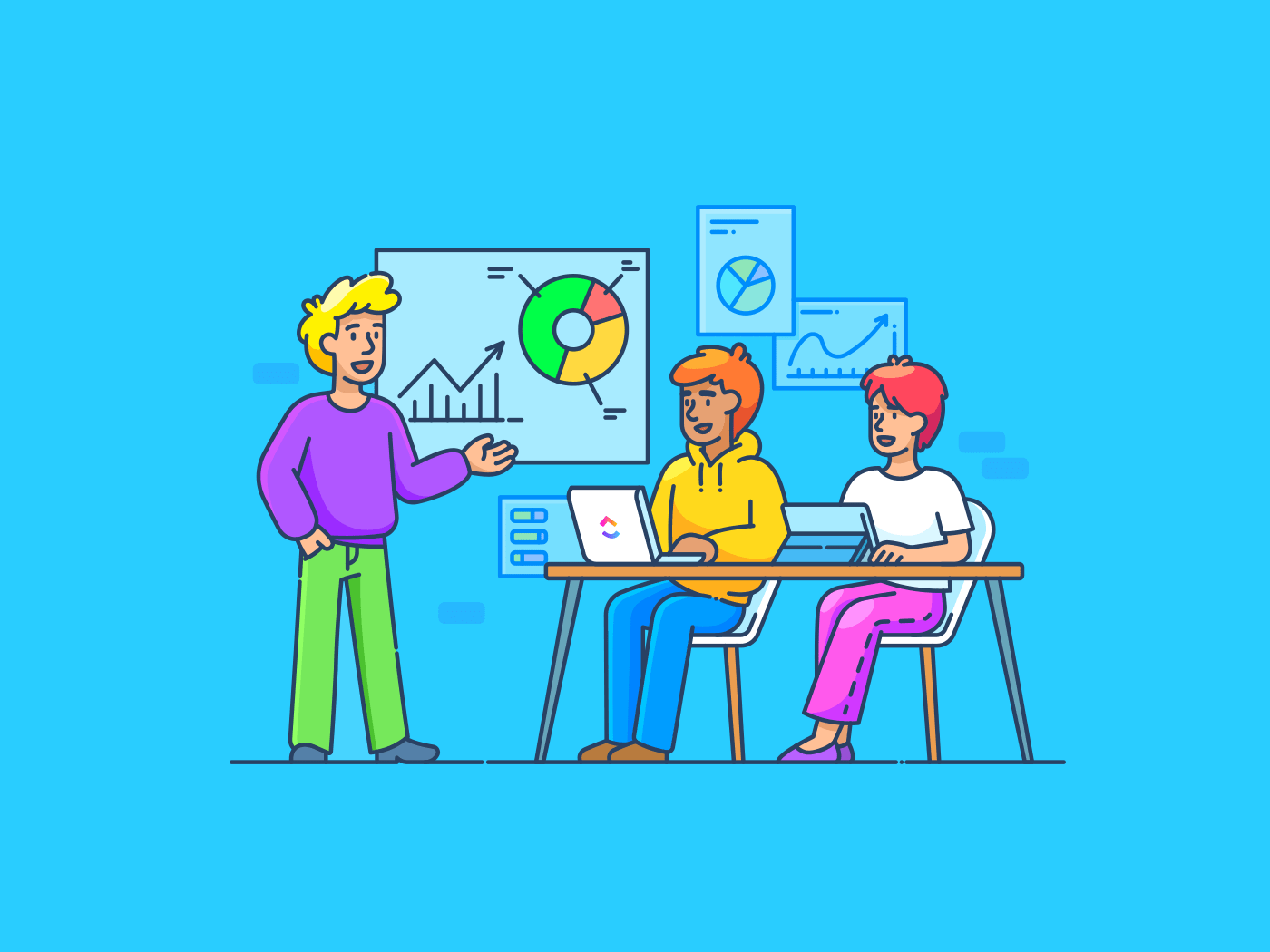
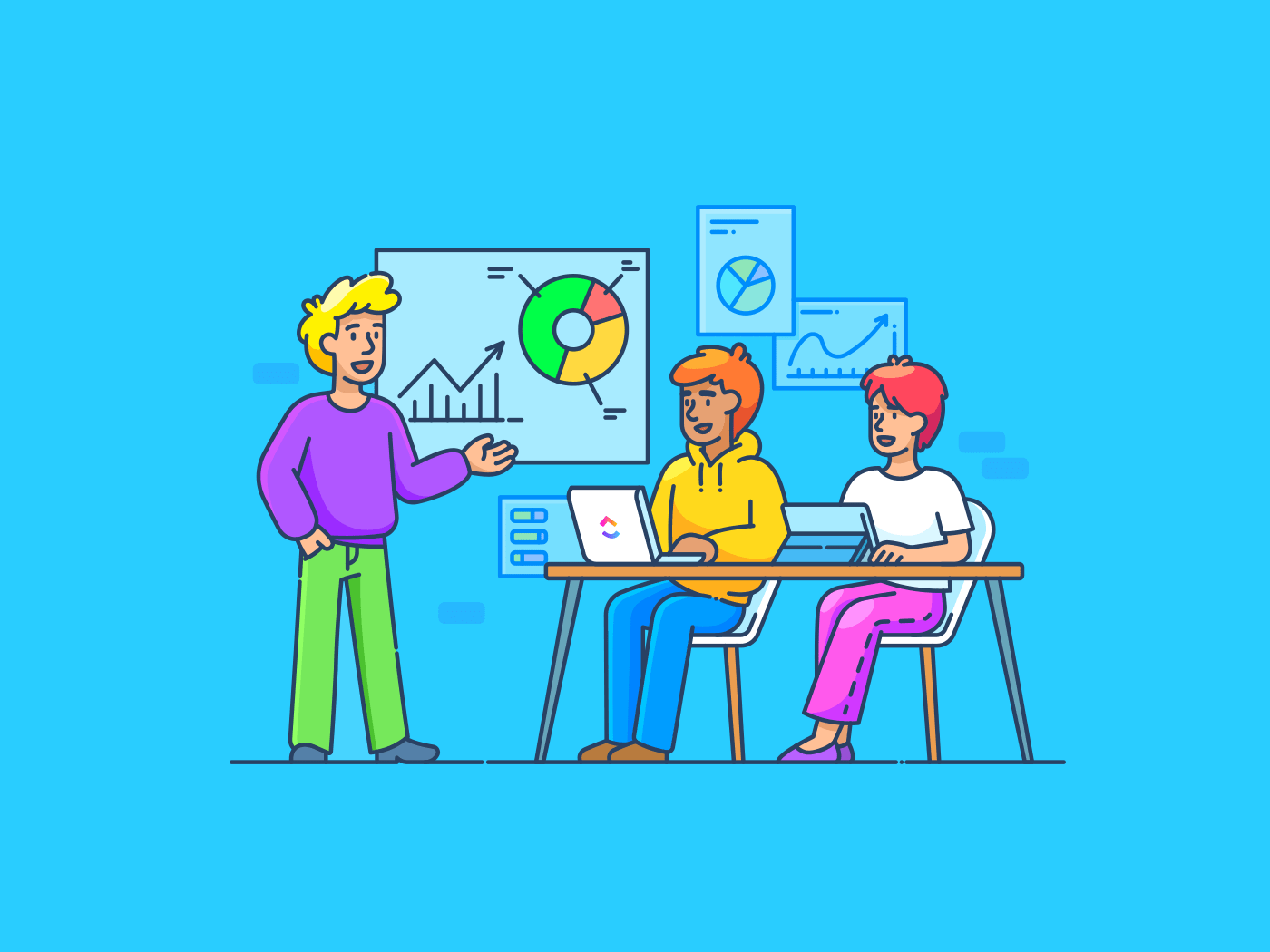
If you have a manufacturing business, you’ve likely heard of the process improvement methodologies Lean and Six Sigma.
Lean has been around for a long time, starting in manufacturing and spreading to other areas like HR. Comparatively, Six Sigma is a newer approach. They’re often discussed together because they improve processes and boost bottom lines.
But they’re quite different.
Lean focuses on making processes more efficient and faster by cutting waste. Meanwhile, Six Sigma aims to reduce errors and variations.
So, which is better: Lean or Six Sigma?
In this article, let’s explore what makes Lean and Six Sigma unique, how they work, and which might be the best approach for your business needs.
The Background and Principles of Six Sigma
Let’s take a deeper look into Six Sigma’s history and what it entails.
History of Six Sigma
It all began with an engineer named Bill Smith at Motorola in the mid-1980s.
He developed the Six Sigma methodology to improve the quality of production processes by reducing variability and defects.
The term ‘Six Sigma’ comes from statistics, referring to processes operating at no more than 3.4 defects per million opportunities.
In 1986, Motorola formally introduced Six Sigma as a company-wide quality improvement initiative and ended up saving millions of dollars in revenue. Due to this success, Motorola became the first company to win the Malcolm Baldridge National Quality Award in 1988.
Inspired by Motorola’s success, Six Sigma was quickly adopted by two major companies in the 1990s: Allied Signal and General Electric (GE).
- Allied Signal’s CEO, Larry Bossidy, aggressively implemented the method and saw significant success and savings by reducing defects
- CEO Jack Welch made Six Sigma a core business strategy at GE and saved over $1 billion in 1998. The news made headlines and popularized Six Sigma across many industries
Throughout the 2000s, Six Sigma evolved by integrating older quality management ideas with new data-driven techniques.
Today, it has become a global standard for quality management and process improvement. It’s widely used across industries, including manufacturing, healthcare, finance, and information technology.
Recently, Six Sigma merged with lean manufacturing principles to improve process flow, efficiency, and quality. This created the Lean Six Sigma methodology, which has been adopted by many major companies worldwide.
DMAIC in Six Sigma
DMAIC is one of the core components or principles of the Six Sigma methodology.
It’s a data-driven quality strategy for improving processes and outlines 5 phases with dedicated objectives and tools:
- Define: The aim here is to identify the problem and define project goals, scope, and customer expectations accordingly. Tools include project charter, SIPOC diagrams, and stakeholder analysis
- Measure: Quantify the problem by collecting data on current processes, validating the system, and setting baseline performance metrics. Use data collection plans, measurement system analysis, process maps, and statistical sampling for this phase
- Analyze: Now, you pinpoint the root causes of the defects by analyzing the collected data to determine cause-and-effect relationships and key factors affecting the process. So, work with Pareto charts, tools for root cause analysis (fishbone diagram, 5 Whys), and regression analysis
- Improve: Once you know what’s causing the issue, prepare potential solutions, test them, and implement them. Use techniques like design of experiments (DOE), poka-yoke error-proofing, process mapping, and pilot testing to check if the solutions work
- Control: Finally, use control charts, SOPs, and process audits to ensure improvements are sustained over time. Monitor process performance through different statistical process control (SPC) methods and standardize the solutions as needed
Six Sigma’s role in quality management and statistical process control
- Provides a structured methodology (DMAIC) for data-driven process improvement and defect reduction
- Helps deploy SPC methods like control charts to monitor and control processes
- Quantifies process capability using sigma levels and corresponding defect rates
- Improves quality from the design stage through tools like FMEA (Failure Mode and Effects Analysis) and DOE
- Bases decisions on statistical evidence rather than assumptions
With a solid grasp of Six Sigma’s origin and principles, let’s now turn our attention to Lean.
The Background and Principles of Lean
Lean project management originated from Toyota’s manufacturing practices in Japan after World War II.Â
Often referred to as the Toyota Production System (TPS), this systemic approach developed by Taichi Ohno aimed to improve efficiency, eliminate waste, and enhance product quality.Â
The term ‘lean’ was coined much later, in the 1980s, after researchers from the West published a book highlighting the effectiveness of TPS.
Lean principles
Lean aims to create more value for customers with fewer resources by optimizing processes and eliminating waste. The key lean principles include:
- Value: Understand what the customer values in the product/service and focus specifically on those (value-added) activities. Eliminate all resources that don’t contribute to these values
- Value stream: The value stream is the entire sequence of all activities and information flows required to deliver the value. Visually map out this sequence to identify and eliminate wasteful steps
- Flow: The value-creating steps need to have an uninterrupted flow. So, make sure to design and redesign processes to enable a continuous flow, reducing waiting times and bottlenecks
- Pull: A pull system lets customers drive value creation by producing products based on actual demand. That means you produce only what is needed when it is needed. Implement such systems (for example, Just-in-Time or JIT production) to reduce excess inventory and work in progress
- Perfection: Lean is a continuous journey to perfection, aiming to streamline processes, reduce waste, enhance value, and constantly improve. It promotes constant improvement and encourages everyone to do their best
Comparing Lean vs. Six Sigma
Lean and Six Sigma are not the same. So, how do they differ from each other? Let’s find out.
Key similarities & differences
There are several similarities between these two methodologies:
Similarities
Lean and Six Sigma originated in Japan’s automotive manufacturing and were later adopted by Western manufacturers. While Lean has various versions, both methods share a common goal: boosting process performance by eliminating waste, defects, and variations.
Plus, both rely on a data-driven approach, making changes based on data analysis and measurable metrics rather than assumptions.
Customer satisfaction is equally central to both Lean and Six Sigma, with a strong emphasis on creating value for customers. And the process for this value creation is often led by cross-functional teams.
Regardless of your chosen methodology, both techniques are huge promoters of continuous improvement. They encourage you to constantly review and optimize workflows to increase their efficiency and effectiveness.
Differences
But there are also several differences between these two methodologies:
1. Waste: Lean and Six Sigma define waste differently. Lean sees waste as any process or activity that doesn’t add value to the customer. So, lean practitioners focus on optimizing processes to increase customer value.
In contrast, Six Sigma identifies waste as a result of variation within a process. People who use this method work to eliminate defects and waste by reducing this variability.
2. Methods and approaches: Lean is a mindset based on principles that guide smarter decision-making. It uses methods like Kaizen events, value stream mapping, 5S, and TPM to continuously increase value and eliminate waste. This approach works best when it becomes part of the organization’s culture and everyone participates.
On the other hand, Six Sigma is a structured program that uses DMAIC and DMADV (Define, Measure, Analyze, Design, Verify) to reduce variability and risk.
It comes with a ‘belt’ certification system, where people at different levels have specific roles:
- Black belt: Leads projects and trains teams
- Green belt: Collects and analyzes data and leads smaller projects
- Master black belt: Trains and coaches other belts and develops key metrics
- Yellow belt: Participates in projects and reviews improvements
- White belt: Works on local teams and basic Six Sigma concepts
3. Tools and functional areas: Lean’s origins are in software development, so it’s still used in forms like Kanban, agile methodologies, and Scrum. Many sectors prefer its visual tools to add customer value.
Because of its arsenal of statistical methods, Six Sigma is great for complex environments that require reduced variability and risk. It’s applied in areas such as manufacturing and engineering but can become an issue for small companies due to resource limitations.
Application of Lean in business process management vs. Six Sigma’s statistical focus
Lean takes the help of visual methods to improve business process management.
For example, it uses value stream mapping to depict the sequence of activities, information flow, and handoffs within a business process. This way, you can easily identify waste, bottlenecks, and areas that require attention.
In addition to eliminating waste with 5S and Kanban methods, Lean also tries to establish an uninterrupted flow of work using techniques like single-piece workflow. It standardizes work procedures through documentation, training, and visual controls.
Lean continuously improves the process by reducing setup times. It uses Single-Minute Exchange of Die (SMED), a powerful tool that dramatically reduces the time it takes to switch between production runs of different products on the same equipment. It also analyzes root causes (with methods like the 5 Whys) and involves everyone in Kaizen events.
Six Sigma, however, relies on statistical principles. It heavily emphasizes data-driven decision-making, employing statistical tools throughout its DMAIC approach (Define, Measure, Analyze, Improve, Control).Â
Common statistical assumptions include:
- Normal and Poisson distributions for continuous and discrete variables
- Use of control charts, capability analysis, and design of experiments (DOE) to optimize processes
The method uses various statistical tools at different stages to pinpoint root causes and maintain the improvement of processes. Some of these are:
- Descriptive statistics
- Control charts
- Histograms
- Regression analysis
- DOE
Plus, Six Sigma checks data accuracy with measurement system analysis (MSA) in the Measure phase, ensuring it’s reliable for decision-making.
4. Leadership: If teamwork is your priority, Lean is the way to go. Its flexible structure allows teams from all levels (from individual contributors to executives) to collaborate, solve problems, and think broadly.
Six Sigma has a structured, hierarchical leadership model, which is great for highly organized companies. Its certified roles range from local problem-solving to leading projects and training teams.
Lean vs. Six Sigma
Here’s an overview of the differences between Lean and Six Sigma:
Aspect | Lean | Six Sigma |
Goal | Process improvement | Process improvement |
Definition of waste | Process or activity that adds no value to the customer | Results from variation within a process |
Approach | Mindset based on principles | Structured program with a belt certification system |
Methods | Kaizen events, value stream mapping, 5S, TPM | DMAIC and DMADV |
Metrics tracked | Cycle times, inventory levels, flow metrics | Defects per million opportunities (DPMO) |
Functional areas | Software development companies of any size | Suitable for big, complex organizations |
Tools | Visual tools, single-piece workflow, SMED, 5 Whys | SPC, DOE, statistical analysis tools |
Leadership | Flexible, great for collaboration | Hierarchical, works best for highly organized companies |
Benefits & Limitations of Lean vs. Six Sigma
Lean and Six Sigma have their fair share of benefits and limitations.
Benefits of Lean
- Improves process flow and gets rid of waste
- Makes product cycles faster and more responsive to what customers want
- Uses simple visual tools like value stream mapping
- Gets employees involved in always making things better
- Simplifies complicated processes, especially ones with lots of stops or delays
Limitations of Lean
- Not as focused on numbers and statistics as Six Sigma
- Might miss process variations
- Does not use advanced data analysis methods
Benefits of Six Sigma
- Cuts down process differences by using strict data-based methods
- Measures process quality in sigma level (defects per million)
- Uses strong number-crunching tools like DOE, hypothesis testing
- Follows a clear plan with set training and certifications
- Works great for tough processes that require high-quality outcomes
Limitations of Six Sigma
- Needs more training than Lean
- Harder to use for simple processes
- May miss overall improvements by focusing too much on defects
- Seen as more strict and controlled from the top down
How to Implement Lean or Six Sigma
Whether it’s Lean or Six Sigma, you can implement either of them in your organization by following the steps below:
1. Get commitment from your leadership
First things first, you’ll have to get top management to support and commit to Lean or Six Sigma as a key part of the organization’s goals and strategy. Ensure the company leaders are on board to effectively drive whichever methodology you choose.
2. Have a compelling foundation
Find a strong reason to start Lean or Six Sigma, like resolving customer complaints, quality problems, or process inefficiencies. Without a clear reason, motivating people to use these methods effectively might be harder.
Once you have sorted out your reasons, build a program structure that handles planning, training, project selection, and oversight.
3. Pick projects that show quick results
Time is of the essence when it comes to business. And if you don’t want to wait too long for the outcome, choose high-profile projects that can show quick results. Starting with projects that provide visible and immediate improvements can build momentum and support for further efforts.
4. Train and educate your teams
Now that you know what process you’ll move ahead with, it’s time to get your teams up to speed. Train your employees on Lean or Six Sigma principles, tools, and techniques to ensure everyone has the necessary knowledge and skills to use them.
5. Define your goals and objectives
The next step is to identify the goals and objectives that correspond to the areas of problem that you need to resolve. Set specific, measurable, achievable, relevant, and time-bound (SMART) goals to guide the process as smoothly as possible. Map current value streams or define project charters for the targeted problems.
6. Involve key leaders and execute your project
For proper leadership, bring in experts who understand Lean or Six Sigma like the back of their hands. They can help motivate your teams and show them the value of these methods.
Involve influential people, like senior and middle managers, in the process along with them. Their support is crucial for the successful adoption of the Lean Methodology or Six Sigma.
After that, implement your plan. Use the right set of tools and lead Kaizen events or DMAIC projects to drive improvements in your project execution process. Also, ensure systems are in place for collecting, analyzing, and monitoring process/quality data.
Want to get a headstart? Try ClickUp
ClickUp is an all-in-one, AI-powered project management software that simplifies daily business processes with comprehensive tools and features.
It also has a huge library of templates to help you get started on various project management processes and techniques, including Lean or Six Sigma.
If you’re struggling with Lean and want to keep track of your business plan steps without wasting resources, use the ​​ClickUp Lean Business Plan Template. It prioritizes agility and validation over lengthy, traditional plans.
This template helps you quickly create a lean and high-level plan without starting from scratch. It provides a clear structure to guide you through defining your business model, target market, goals, finances, and more. However, it also offers flexibility to adapt to your specific needs.
It gives a complete overview of your business strategy and an easy-to-follow outline for your business plan, along with step-by-step guidance for each section.
Benefits of using this template:
- Ensures that you concentrate on the most critical aspects without overlooking key details
- Results in a clear, easy-to-read presentation
- Can be updated and adjusted swiftly to match changing market conditions
- Provides an efficient way to convey your business plan to potential investors and stakeholders
However, if you want to streamline specific business areas, such as production or customer service, try ClickUp’s Process FMEA Lean Six Sigma Template.
It combines Lean Six Sigma (a combined version of the two methods) and FMEA (Failure Mode and Effects Analysis) into one place to help you systematically identify failure modes, their occurrence and detection probabilities, and actions to mitigate effects and causes.
It’s perfect for recognizing process risks, clarifying improvement areas, and creating an action plan with team alignment.
This comprehensive template simplifies the process by allowing you to:
- Swiftly and accurately identify potential process risks
- Gain clarity on areas that require improvement
- Create an action plan for improvement with team alignment
You can also use ClickUp’s Whiteboard to visualize your Lean and Six Sigma implementation processes, identify bottlenecks, and collaborate on implementation steps and strategies with your team. It’s a versatile tool for mapping out workflows and simplifying operations.
The Whiteboard offers a fully customizable canvas for brainstorming, strategizing, and mapping business processes.
You can use it to:
- Manipulate agile workflows
- Categorize tasks and sub-tasks within Lean and Six Sigma workflows
- Identify root causes of process inefficiencies
- Come up with a corrective action plan to improve critical business processes
Apply Lean or Six Sigma to Your Business with ClickUp
A set of well-structured, smooth-flowing processes is the cornerstone of a successful business, and both Lean and Six Sigma are designed to achieve this.
However, they can seem quite complicated to even experienced project managers. A way to simplify them and achieve the outcomes you’re aiming for? ClickUp!
With project management features, customizable templates, and 1000+ integrations, ClickUp can handle all your business processes irrespective of your chosen process improvement method.
Not only will your production be error-free, but it will also be backed and handled by AI-powered tools and features to ensure you’re on top of everything from a single platform.
Sign up for ClickUp today and let it help you manage your process improvement methods with ease!