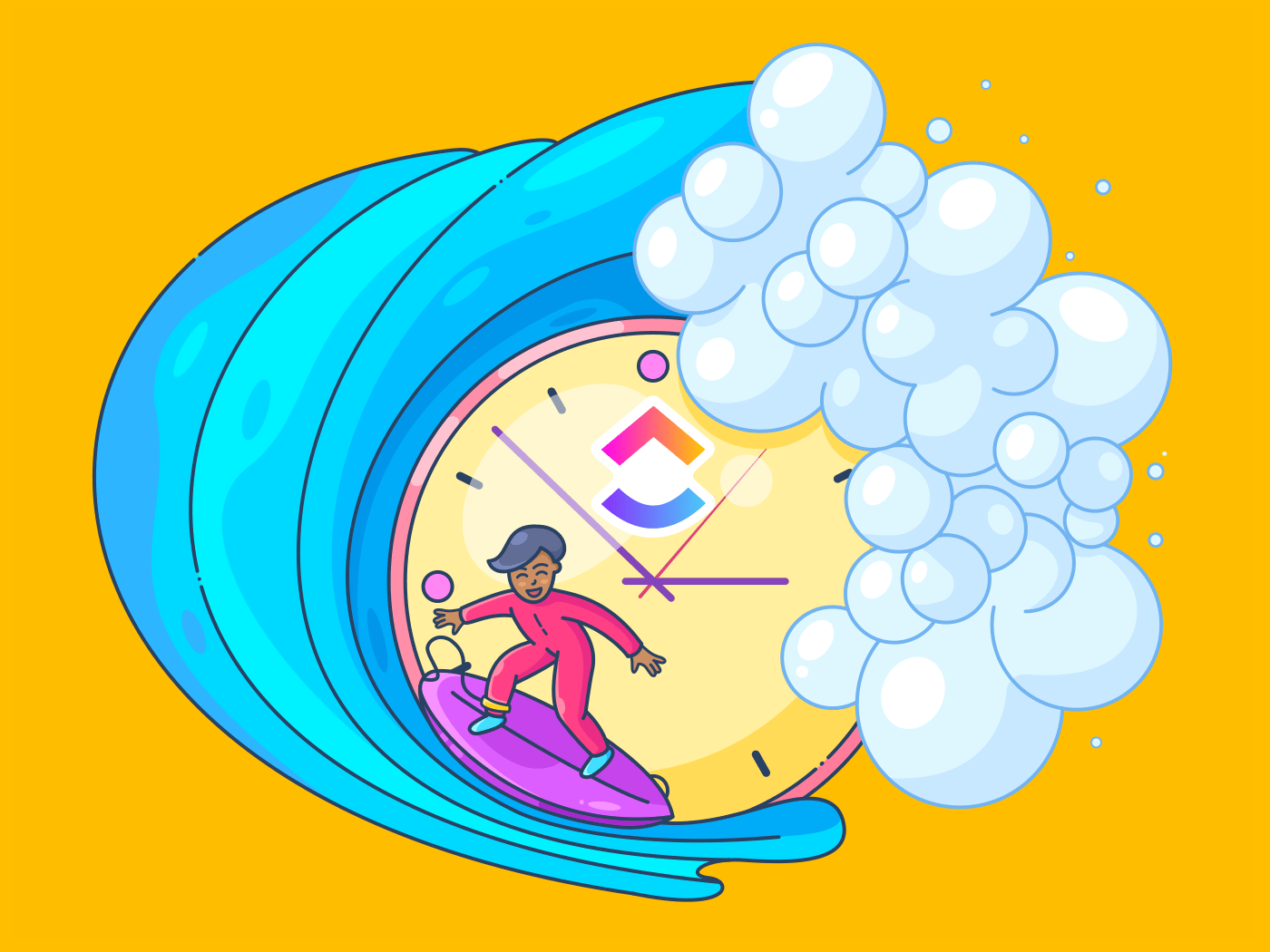
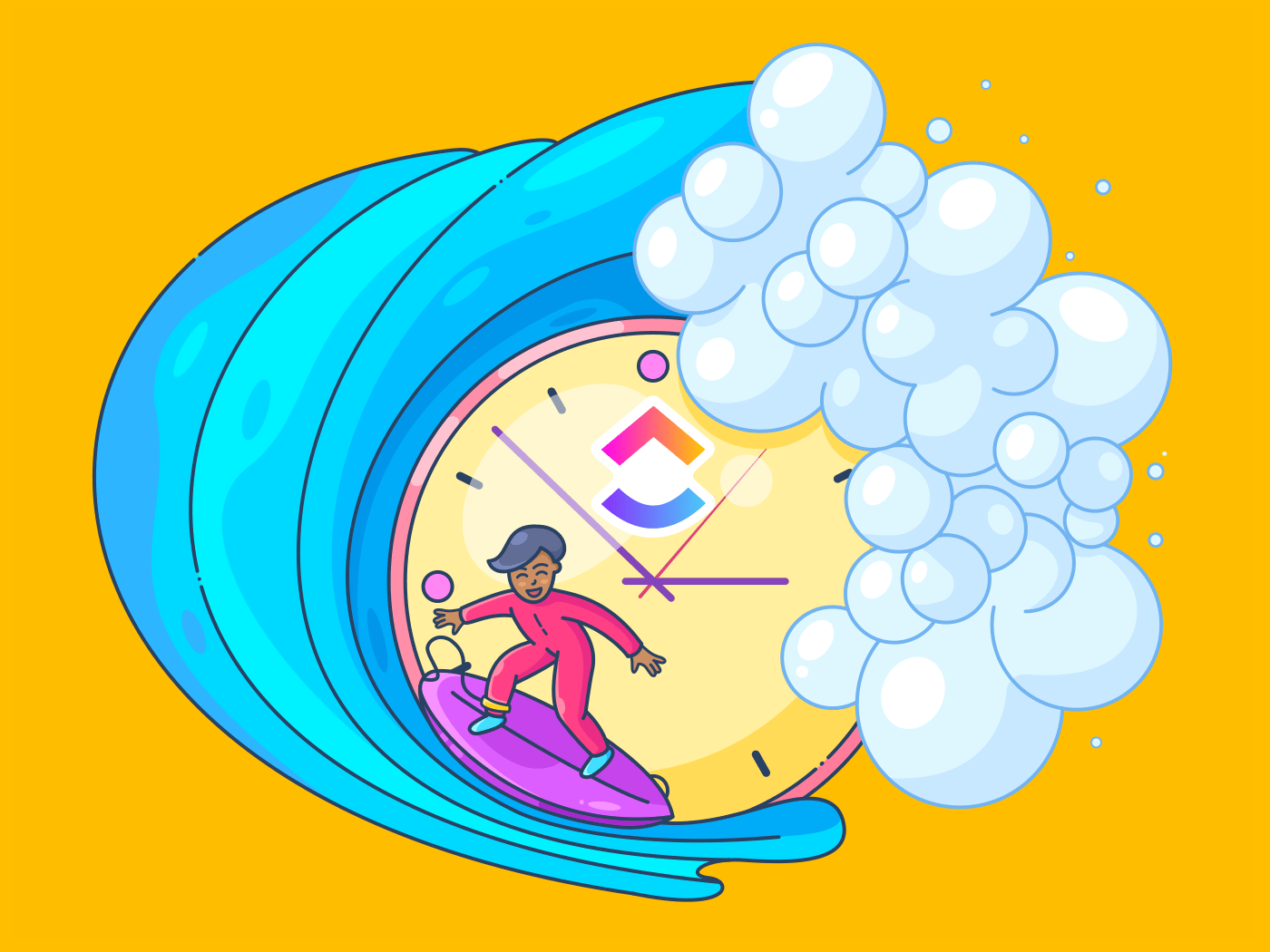
Curious about the differences between cycle time and lead time?
Cycle time and lead time are important metrics used in the production process. While cycle time tells you how long it takes to complete a task, lead time is the time taken between order placement and fulfillment.
We know, we know.
Those sound like two very confusing and not too different times.
But don’t worry.
Distinguishing between them isn’t as tricky as trying to understand the various components of a MasterChef meal.
Rock salt? Kosher salt? Pink salt?
What happened to just salt?!
In this article, we’ll cover the different definitions of lead time vs cycle time and how to calculate and track each metric effortlessly.
Let’s get started. There’s no time to waste!
Note: The first few sections are brief explanations of what cycle and lead time are. If you already have a good understanding of both metrics, you can skip ahead to our comparison section.
What Is Cycle Time?
Cycle time is the time taken to finish one process cycle, from start to end. And while “process” usually refers to the production process in manufacturing, it can be any repetitive activity too, such as answering customer calls.
Cycle time is also defined as the amount of time a team actually works on a product until it’s ready for customer delivery.
And since the word delivery has got us thinking about pizzas, why not use a pizza order as an example here.
In cycle time’s context, “order” refers to customer order for a product or service.
So for a pizzeria, cycle time is the time taken to prepare one delicious pizza.
Just make sure there’s no pineapple on it.
To know the benefits of measuring the cycle time metric, check out our in-depth guide.
Does cycle time include wait time?
Yes, cycle time includes wait time, during which a work item is waiting for the next action. For example, the time spent waiting for the oven to heat up initially.
In a nutshell, cycle time is the total time taken to move a work item from the start to the end of a production or manufacturing process.
How do you calculate process cycle time?
Cycle time is calculated as the ratio of total production time to the number of units produced in that time.
Cycle Time = Total Production Time/Number of Units Produced
To illustrate this with an example, let’s say that you’re a chef in Gordon Ramsay’s restaurant.
No pressure at all, right?
Now let’s suppose that the restaurant works from 10 am to 11 pm and can prepare food for 200 customers per day.
So, Total Production Time = 13 hours.
Number of Units Produced (meals prepared) = 200 meals.
Then, Cycle Time = 13/200 = 0.065 hours.
So it takes around four minutes to prepare each meal.
Is that enough to satisfy Gordon? Let’s hope so!
Read more about calculating cycle time.
How to track cycle time?
Just use ClickUp!
ClickUp is the world’s #1 project management software. Whether it’s Agile, Scrum, Kanban, or Lean manufacturing, ClickUp is the master chef in any project cuisine.
How does ClickUp help track cycle time?
ClickUp’s powerful Agile Dashboards feature lets you calculate task turnaround time with the Cycle Time widget.
Cycle time is measured in two ways:
- ClickUp can automatically start tracking time the instant a task enters an Active status group in your Project Space
- Alternatively, ClickUp lets you choose any other status to count as the start of cycle time
Note: ClickApps help customize your ClickUp Workspace to suit your taste.
But the Cycle Time graph isn’t the only topping on ClickUp’s Dashboard… 🍕
For maximum flexibility, you can also choose from Burnup, Burndown, Cumulative Flow Diagram, Velocity Charts, and more.
What Is Lead Time?
Usually calculated from the customer’s perspective, lead time is the time spent between receiving the customer order to the final product or service delivery. And just like cycle time, you have different definitions for lead time based on the context.
For example, in project management, the lead time is the time taken to complete a project the moment you receive it from the stakeholder.
However, in supply chain management, it’s the time taken to receive supplies once you place an order.
And since we’re clearly in a mood for food right now, lead time starts when a waiter takes a customer order and ends when the customer receives their dish.
Generally, the lesser the lead time, the better, unless you want to experience Hell’s Kitchen quite literally.
Wondering how you can calculate lead time?
Check out our lead time formula guide.
How to calculate lead time?
To calculate lead time, you need to know the delivery date/time and the order’s request date/time.
Lead Time = Order Delivery Time (end date) – Order Received Time (request date)
For example, let’s say a customer orders pasta at 1:30 pm and receives it at 2 pm.
Then the lead time is 30 minutes.
Read more about calculating the lead time metric here.
How to track lead time?
While you could use stopwatches or kitchen timers to track lead time, that’s just a lot of manual work.
Not ideal when you have strict deadlines to meet or hungry customers waiting, right?
Instead, use the Lead Time Widget on ClickUp’s Dashboards! It’ll automatically track how long it takes on average to finish a task from the moment it’s created.
You can customize the:
- Time range: set the required time range and the frequency of the graph
- Sample time: choose how many days you want to include in the average for each point in the graph
- Status group counted as completion: select the status group, like Closed or Done, to indicate task completion
Note: The same customizations can be applied to ClickUp’s Cycle Time widget too.
Still confused about lead time vs cycle time?
Don’t worry! We’ve summarized the differences in a handy chart later on in this article.
However, before we get there, you need to understand that lead time and cycle time aren’t the only Lean metrics or Kanban metrics used by project managers.
You also have Takt time, their German cousin (“takt” is the German word for pulse or rhythm).
What Is Takt Time?
Takt time is the rate at which you should work to complete the production process to meet customer demands on time.
Measuring takt time helps you:
- Adjust workflow throughput based on customer demand
- Improve the entire value stream efficiency for a specific batch size
- Avoid raw material shortages and excess inventory
- Boost customer satisfaction with timely delivery
For example, if you know your restaurant’s takt time, you can optimize the kitchen workflow to serve food to customers on time, helping you avoid such hangry customers:
How to calculate takt time?
Takt time is calculated as the ratio of your total production time to the number of units required by the customer.
Takt Time = Total Production Time/Number of Units Required (customer demand)
Let’s take Gordon Ramsay’s example we discussed earlier.
The cycle time is four minutes to prepare a dish, which should be okay under normal circumstances.
But it’s the weekend, and Gordon expects rush hour.
He wants the staff to serve 300 customers in 13 hours.
Then, takt time = 13/300 = 0.04 hours, which is roughly two minutes per meal.
So if you’ve to meet the demand, you’ll have to reduce the cycle time from four to two minutes.
Good luck serving up a filet mignon that quickly!
Read more about takt time.
How does ClickUp help here?
ClickUp’s Cycle and Lead Time widgets aren’t the only features for operations management.
With the flexibility that even puts the most versatile ingredients in the kitchen to shame, ClickUp offers a wide variety of features like:
- Native Time Tracking: track how long your tasks take right inside ClickUp
- Due Dates: create task deadlines and get auto-notified when deadlines are overshot
- Time Estimates: set accurate timeframes for your remote or in-house team
- Timeline View: visualize your production schedule over days, weeks, and months
- Workload View: monitor your team’s capacity for efficient resource management
- Pulse: analyze your in-house or virtual team’s takt over a day
- WIP Limit: set Work In Progress (WIP) limits to indicate when there’s too much work under a specific status
- Time Tracking Integrations: ClickUp integrates with several time tracking tools like Toggl, Harvest, and Everhour to help you track task time with ease
Check out all of ClickUp’s powerful features here.
What Are the Differences Between Cycle Time, Lead Time, and Takt Time?
Understanding how cycle time, lead time, and takt time are different isn’t as difficult as identifying dishes in MasterChef’s Blind Taste Test challenge.
If you’re still confused about it, don’t worry!
We’ve summarized the key differences between lead time vs cycle time vs takt time in this handy chart:
Cycle Time | Lead Time | Takt Time | |
What it helps with |
|
|
|
What it considers |
|
|
|
How businesses use it |
|
|
|
Formula |
|
|
|
FAQs about Cycle Time, Lead Time, and Takt Time
Dabble in cycle time or lead time, and you’ll probably come across terms like throughput, value stream, and more.
Now, what are they?
No worries, here’s a quick Masterclass to clear your doubts:
1. What is the difference between manufacturing lead time & throughput rate?
From the customer’s perspective, manufacturing lead time is the time between placing an order and receiving it.
On the other hand, throughput rate is considered from the production perspective and measures the rate at which raw material or a manufacturing unit passes through the process.
2. What is value stream mapping?
In Lean manufacturing, a value stream is a sequence of value-adding activities that create an overall product or result for customers or stakeholders.
Value stream mapping is a method where you visualize all the essential steps in your value stream using a flowchart. The chart (known as a value stream map) helps you identify and reduce/remove unnecessary steps in the value stream, making it more efficient.
3. What factors negatively affect lead time?
Five key factors negatively affecting lead times are:
- An unnecessary process step in the production flow
- Inefficient inventory management
- Inventory stock-outs that could cause a production bottleneck
- Varying lead times between your different vendors/suppliers
- Unpredictable events like sudden raw material unavailability
4. How can you reduce your cycle time?
Reducing cycle time not only improves customer satisfaction, but it’ll also boost your team’s productivity.
So here are some ways you can reduce your cycle time:
- Define each user story and goal clearly
- Encourage teams to be self-sufficient, take responsibility, and work with minimal feedback
- Use the WIP limit method to eliminate multitasking
- Automate repetitive manual work
- Adopt an Agile-based approach like Scrum
- Use project management tools like ClickUp to manage processes with ease!
5. What is the main goal of Agile?
The Agile methodology’s main goal is to help teams build and deliver superior quality products in the shortest time possible. For this, Agile metrics (like cycle time and lead time) and tools (like sprint backlog) aid process improvement.
Read more about Agile project management.
Conclusion
In the kitchen, knowing how you’ll tackle a recipe (from prep to garnish) not only prevents cooking disasters, but it’ll also make the entire process more efficient.
And that’s where different times like cycle time, lead time, and takt time come into play.
Understanding and tracking each metric is crucial for streamlining any production or manufacturing process, be it software delivery or satisfying hungry customers on time.
However, using stopwatches to time each operation is anything but efficient.
Instead, just use Clickup!
From accurately tracking cycle time and lead time to managing remote projects, ClickUp can help you every step of the way.
Get ClickUp for free to start tasting project success today!