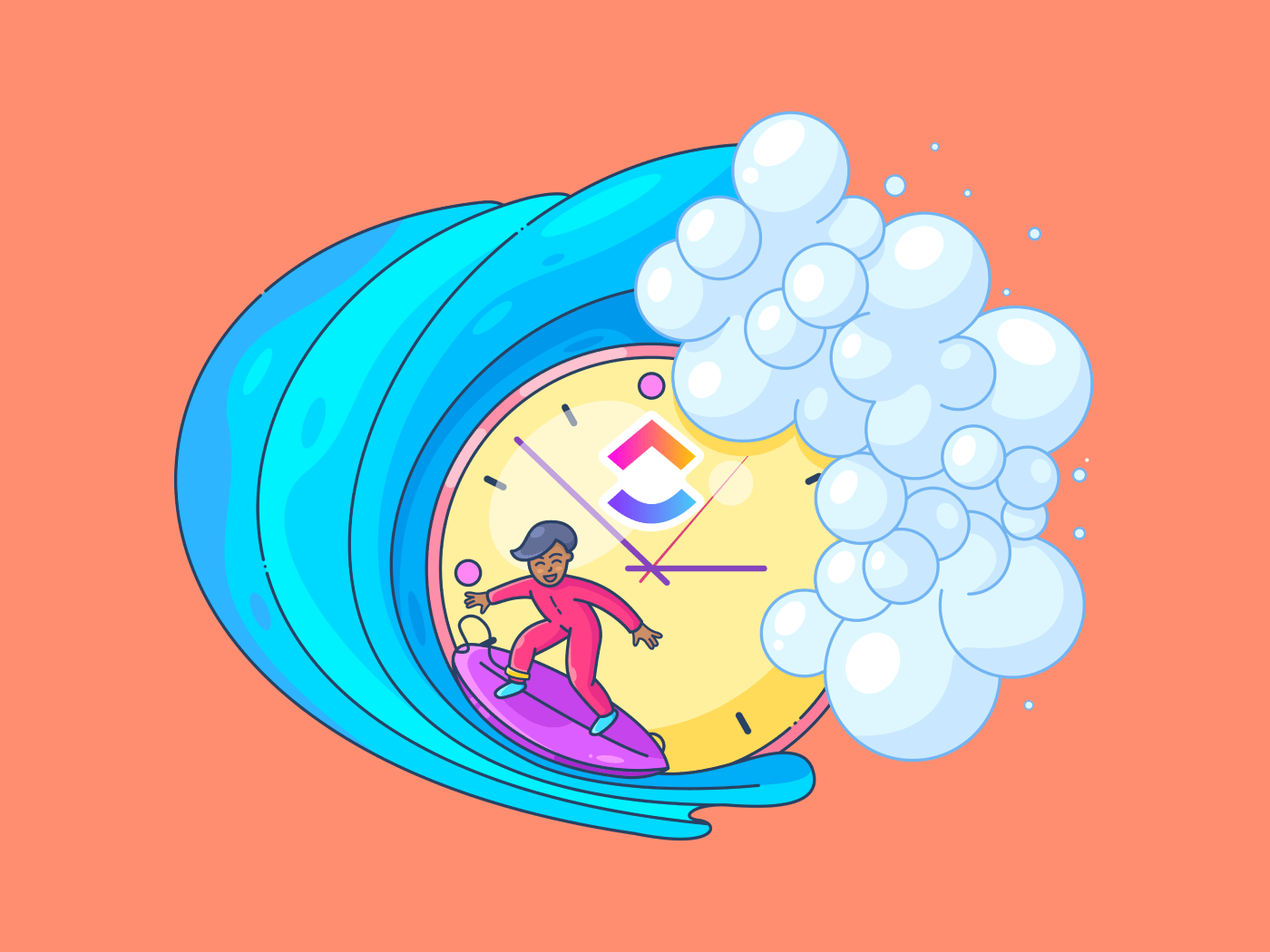
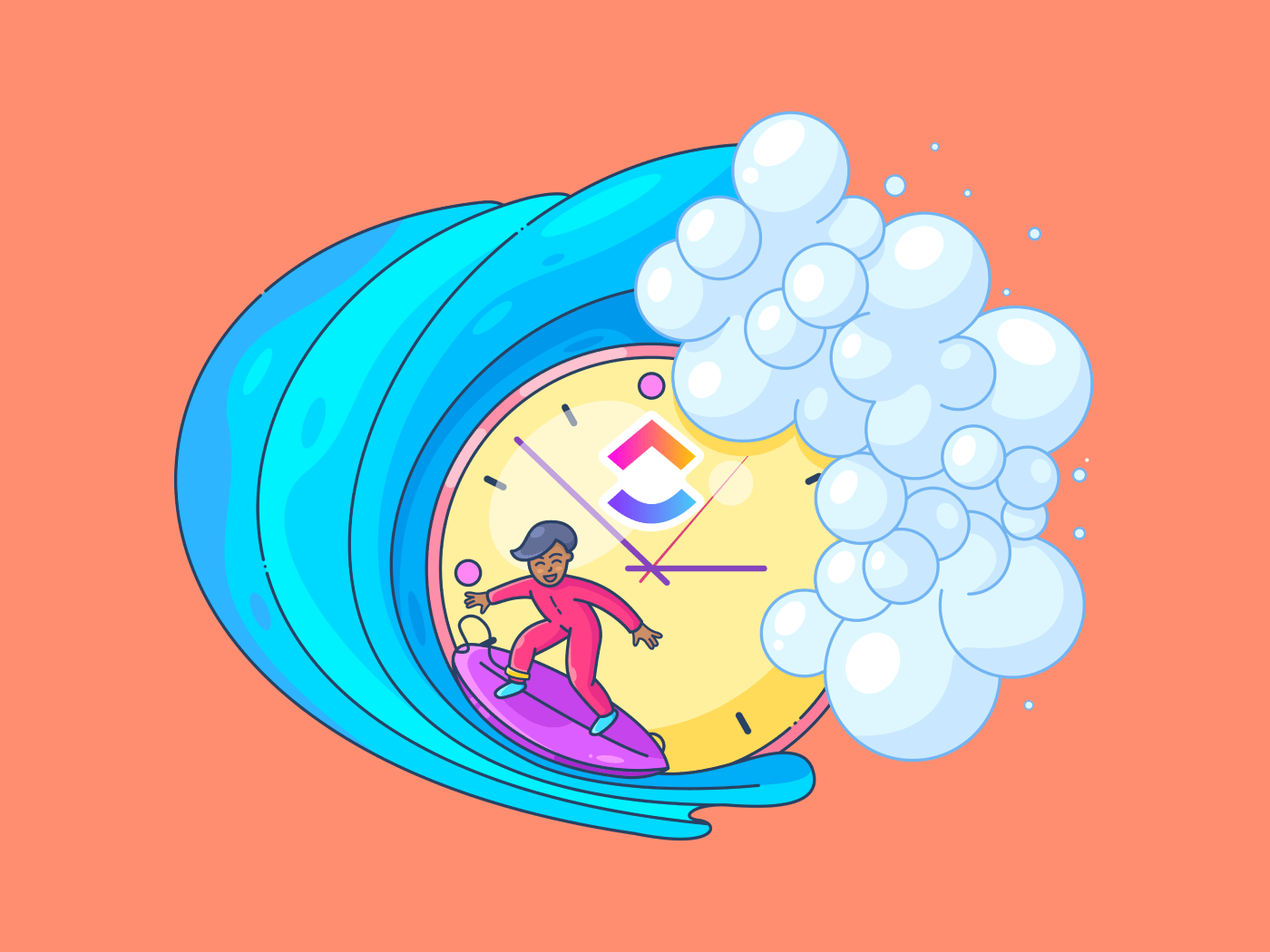
“How long will it take?” and “how much would it cost?” are the two questions that every buyer would ask, whether it’s a tailored suit or software implementation.
In this blog post, let’s explore what it takes to answer the first question, using a concept called lead time.
What is Lead Time?
Lead time refers to the total time required to complete a process from initiation to completion. It is the latency between a customer placing an order and receiving their product or service.
The concept of lead time has roots in the early industrial age, gaining prominence with the rise of manufacturing and supply chain management practices. In manufacturing, it is the time taken by the production unit to manufacture a product. This could stretch across a few weeks.
From manufacturing, it is now a popular metric in various industries. When you go to a restaurant and order dinner, they might say, “please allow us 20 mins to prepare your food.” That 20 minutes is the lead time.
In agile software development, project managers use lead time for sprint planning, scheduling deployment, allocating resources, managing stakeholder expectations, and and more.
Different Types of Lead Times
Depending on your goals, you can measure lead times for the entire process or just some parts. Some of the different types of lead times are as follows.
Production lead time
The total time required to manufacture a product from the start of the physical production process to its completion is called production lead time.
Consider a furniture manufacturing company producing custom tables. If it takes:
- 2 days to receive materials
- 3 days for cutting and assembling
- 1 day for sanding
- 2 days for varnish and finishing
- 1 day for inspection
The total production lead time is nine days. If there are any gaps or wait times due to the non-availability of assembly line/team members, that should also be included.
Material lead time
The time from placing an order for materials until receiving them, ready for use in production is called material lead time.
It includes the time for the vendor to process the order, prepare/manufacture the raw material, pack and ship it to your assembly line.
Material lead time is often the first part of production lead time. Whether it’s a car manufacturer buying aluminum or a baker buying sugar, material lead time defines when you can start work.
Manufacturing lead time
The total time required to manufacture a product, from the start of production to the completion of the final product, is called manufacturing lead time. It encompasses all stages of the manufacturing process, including setup, project execution, and assembly.
While production lead time includes time for receiving materials, inspection, etc., manufacturing lead time is only the time taken to create the product.
Going by the previous example, the manufacturing lead time would be six days, not including the two days to receive materials and one day for inspection.
Procurement lead time
The duration from making a purchase request for goods or services until their delivery is called procurement lead time.
It encompasses requisition processing, purchase order creation, supplier selection, manufacturing, and delivery. Procurement lead time begins before material lead time but also includes it.
Procurement lead time helps project teams gauge the latency resulting from processes outside their immediate purview.
Customer lead time
The duration from when a customer places an order until they receive the product or service is called customer lead time.
In a fast-food restaurant like McDonald’s, the lead time is minimized by pre-processing items much ahead of order placement—possible because of the standardization of services. This applies to SaaS tools as well. A customer can instantly have access to software because the product is already created and ready to ship.
However, if you’re getting a customized logo designed for your brand, the customer lead times will include the entire production process.
Shipping lead time
The time from when a product is ready for shipment at the facility until its delivery to its final destination is called shipping lead time. This period includes preparing the product for shipment, handling, transit, and delivery to the customer or project site.
In modern supply chain management, shipping lead time is an important metric. For instance, if your smartphone is being assembled in China or India, your ability to sell it in the US depends on how long it takes for your vendor to ship it to you. So, your go-to-market plans must accommodate shipping lead times.
Cumulative lead time
The sum total of the lead times across various processes is called cumulative lead time or supply chain lead time. It includes the lead times of all its components and processes, from the initial order of raw materials to the delivery of the finished product to the end customer.
With so many types of lead times applicable to various situations and environments, calculating lead time can be a challenge. So, we’ve brought help. Here’s the lead time formula and a step-by-step process to calculate it.
How to Calculate Lead Time?
The simplest way to calculate lead time is to look at past data and calculate the time from the start date to the end date.
For example, if the process starts on 01/01/2024 and ends on 01/31/2024, the lead time is 31 days. On a project management tool like ClickUp, you can automatically calculate average lead times based on historical data.
While it offers a great consolidated view, this lead time formula doesn’t give you the granular input needed to improve efficiency. So, another way to approach this is to work forward. Here’s how.
1. Identify the components of lead time
Start by breaking down the process into its main components, such as:
- Procurement of raw materials
- Pre-processing
- Production/manufacturing
- Cooling off period, if any
- Latency/wait times
- Quality control and inspection
- Assembly
- Packaging
- Order processing
- Shipping and logistics
Not all processes will affect lead time. In some cases, they might be called or performed differently.
For instance, in software engineering, packaging might include containerization, and shipping might be deployment. For such projects, ClickUp’s project time tracking is a fantastic tool to measure accurately. To track time on ClickUp, team members can start and stop the timer, add a range, or just enter the time taken in hours/minutes retroactively!
So, choose all the components applicable to your business.
2. Measure individual lead times
Based on whichever components apply to you, calculate individual lead times.
Procurement lead time formula: Date of receipt of order – date of requisition from the project team.
If you use ClickUp forms to collect requisitions, you’ll find it much easier to enter the date of receipt and view the lead time on the dashboard.
While the project team has little control over how quickly the procurement team works, this lead time is critical for the overall efficiency of the process.
Production/manufacturing lead time formula: Date of final output – date of receipt of raw materials. Use this metric to determine the time needed to turn raw materials or components into the final product, including setup, processing, assembly, quality assurance, or inspection times.
Shipping lead time formula: Time delivered to the customer – time shipped from the warehouse. Some businesses include packaging in manufacturing lead time, while others consider it a shipping-related process. Choose what’s right for you.
3. Add ‘em up!
Sum up the individual lead times (procurement, production, and shipping) to get the total lead time or actual order lead time. ClickUp Formula fields can make it much simpler with date and time functions, string functions, logic functions, and mathematical functions.
While you do that, here are a few things to remember.
Consider buffer time: If you’re using lead times as a benchmark for deciding the promised delivery date to the customer, add some buffer time to cover for any unforeseen delays or variability in the process.
For instance, a small delay in one step can have a cumulative impact on the following ones. Use the ClickUp Gantt chart to visualize dependencies and overall impact on the delivery timeline.
Break down the lead time to granular detail: Most businesses calculate lead times to improve efficiency. If that is the case, you want to keep all granular detail. For instance, you need to know if customs clearance takes the biggest chunk of your shipping lead times.
Lead Time Examples
Lead time is simply the time between the start and finish of a process. Across industries, businesses, projects, and teams, there are hundreds of examples of lead time.
Lead time in manufacturing
Let’s say you’re a manufacturer of cotton t-shirts selling through retail stores. Your lead time would be the total of:
- Procurement time for cotton (15 days)
- Procurement time for other materials such as threads, buttons, packaging materials, etc. (3 days)
- Production/processing time for measuring, cutting, stitching, ironing, folding, and adding tags (1 day)
- Inspection time (1 day)
- Packaging time (3 days)
- Shipping time to retailer (12 days)
Total lead time = 35 days
Lead time in software project management
Software development projects might be slightly different. The planning and architecture phases might be much longer, but the rest might happen in short sprints, which develop incrementally.
Therefore, lead times are typically calculated from when a user story is ready until the time the feature is deployed.
Benefits of Reducing Lead Time
Lead time tells you how much time you take to do the work. By extension, you can learn how much you can produce at any given time. For instance, if one person can develop one feature in a week (i.e., your lead time), you can plan your resource allocation and capacity based on how many features you need to develop each week.
With a reduced lead time, i.e., if one person can develop two features each week, you can increase revenue, efficiency, customer satisfaction, competitive advantage, and more!
Customer satisfaction: When you can deliver a product sooner to a customer, they’re likely to be more satisfied. This is why reducing delivery lead time—i.e., meeting deadlines—is a critical metric for e-commerce players like Amazon, who invest heavily in warehousing, logistics, and automation for order fulfillment.
Efficiency: A shorter lead time means you can do more within the same duration, improving process efficiencies. Greater efficiency also speeds up production and reduces storage and holding costs.
Agility: Reducing project execution lead time increases a company’s ability to respond quickly to market changes or meet customer demand. During COVID-19, organizations that could work remotely and create digital experiences quickly—in shorter lead times—gained immense competitive advantage.
Inventory management: Shorter lead times lead to reduced inventory levels—the fundamental advantage that Japanese automobile players first saw with lean manufacturing. This freed up warehouse space, reduced inventory obsolescence, and decreased the capital in stock, improving the company’s overall financial health.
The benefits of reducing lead times can be seen throughout the process. But how would you achieve it? Here are some tips.
Strategies to Reduce Lead Time
To optimize anything, you need to know the current state. So, begin there.
Use time management apps to calculate lead time across all processes and stages accurately. Then, identify optimization opportunities. Once you have the basic data at your fingertips, the next question is: How to save time?
Automate
Automate processes that don’t need human interaction or intervention. This could be as simple as setting up if-this-then-that workflows on your project management software. For instance, if a task is overdue, people are automatically notified on the escalation matrix. Or, if the designer has completed a task, automatically assign it to the developer.
ClickUp Automations has 100+ templates to streamline workflows, routine tasks, project handoffs, and more.
Schedule better
Schedule resources to eliminate any unnecessary wait times. Use the ClickUp Workload view to see who’s doing what and assign work. Encourage team members to see their own productivity reports to achieve their time management goals!
If you’re unsure where to start, ClickUp’s time management templates are here to help. Choose from the ten templates and customize them to your needs!
Forecast accurately
Reduce inventory management lead time with techniques like safety stock, reorder points, and economic order quantity (EOQ) to optimize inventory levels. Use robust inventory management software for taking stock!
Share knowledge
Prevent knowledge gaps with detailed documentation and knowledge-sharing. ClickUp Docs is designed to help you write and share anything within the organization. What’s more? ClickUp AI can proofread, summarize, and make information more accessible.
Reduce Lead Time and Optimize Your Workflow With ClickUp
Accurately and instantly answering the question—How long will it take?—is an important project manager job.
It helps throughout the project management lifecycle in planning, scheduling, allocating resources, building contingencies, disaster recovery, stakeholder management, go-to-market strategy, etc.
Accurately calculating lead time is a simple yet powerful way to predict the future. In today’s rapidly evolving world, minimizing lead time can be your business’s single biggest differentiator.
As you invest more in reducing lead times, you also build efficiency and productivity in your systems. For instance, even the simplest automation reduces lead times not only for that process but also for the entire organizational workflow.
Optimizing lead times has compounding effects, so ClickUp is designed to give you the power to see, measure, and minimize lead times.
ClickUp’s all-in-one free project management software empowers you to track task time, monitor lead times, measure performance, optimize metrics, and automate processes all in one place.
From creative agencies to real estate management, organizations across the spectrum deliver products and services quickly with ClickUp. See for yourself.
Frequently Asked Questions (FAQ)
1. What is lead time formula?
Lead time = Time of completion – start time
While this is the most straightforward lead time formula, it doesn’t explain why the lead time is the number it is. So, organizations sometimes work forwards. During such times, the lead time calculation is as follows.
Lead time = Procurement lead time + production lead time + delivery lead time
2. What is lead time vs. cycle time?
Though somewhat similar, these two metrics serve different purposes and needs. Here’s an overview of cycle time vs. lead time.
Lead time | Cycle time | |
---|---|---|
Definition | Total time taken from the moment a customer places an order until the order is delivered | Time required to complete a specific task or process in the production of a single item |
Scope | Measures the end-to-end process | Measures the time spent on a specific segment/sub-process |
Purpose | Estimate delivery times Plan supply chain activities Provide a timeline for customersManage inventory | Assess operational efficiency Identify bottlenecksOptimize production processes |
Formula | Delivery date – Order request date | Total production time/number of units produced |
3. What is lead time for delivery?
Lead time for delivery refers to the total time from when a customer places an order to when it’s delivered to their doorstep.