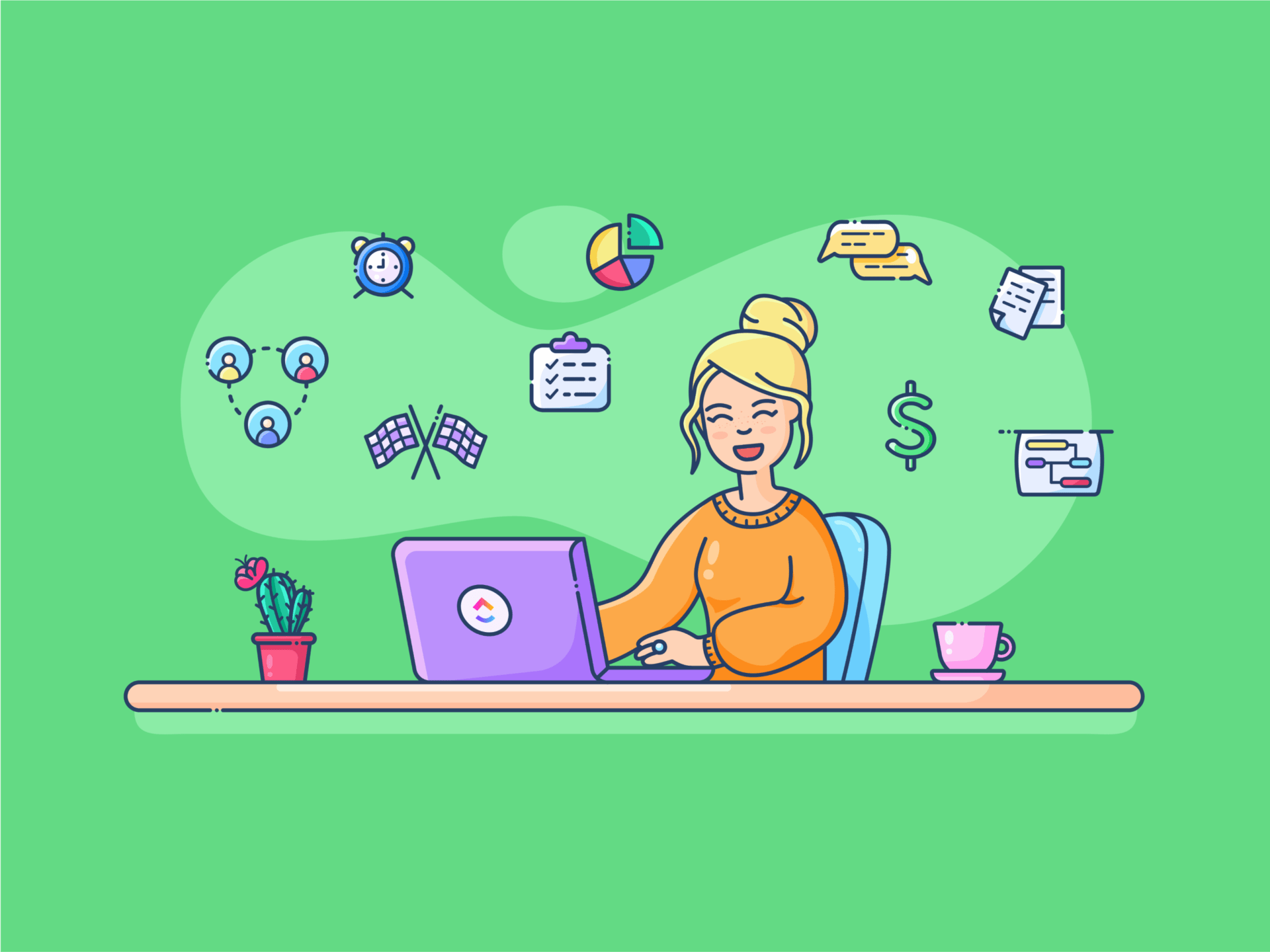
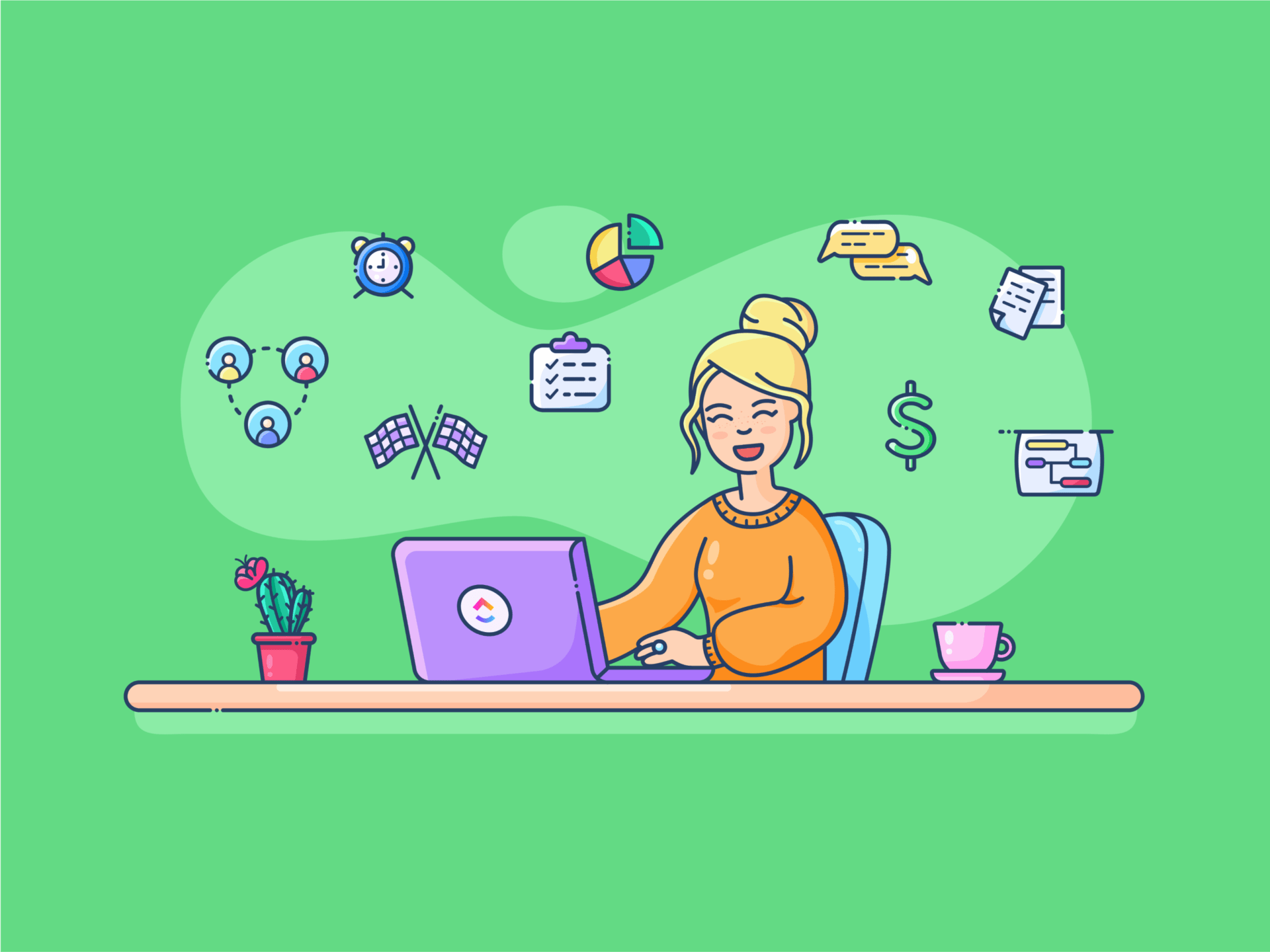
Feel like your improvement plans are slipping through your fingers, like trying to catch popcorn in a movie theater?
You’ve got a process to fix, a team to rally, and yet, somehow, things just…pop everywhere.
The PDCA cycle (Plan, Do, Check, Act) might just be the answer to organizing those scattered ideas.
This scientific method gives you a simple, clutter-free framework for tackling process improvements. Whether you want simplified operations or better results, the PDCA cycle keeps you grounded, efficient, and in control.
Ready to turn your scattered efforts into a smooth-running process machine? Let’s break down how the PDCA Cycle transforms your continuous improvement game.
What Is the PDCA Cycle?
Only less than one-third of companies report successful transformations that both improve performance and sustain those improvements over time. Even when transformation efforts succeed, companies capture, on average, only 67% of their maximum potential benefits.
In this context, the PDCA cycle is a framework that helps organizations overcome these challenges. Short for Plan, Do, Check, Act, PDCA is a continuous improvement model designed to help organizations implement changes effectively.
Originally known as the Shewhart Cycle, this method was developed by statistician Walter A. Shewhart and later popularized by Dr. W. Edwards Deming.
It offers a structured and iterative approach to enhance your internal and external processes and solve problems by breaking down improvement into four steps:
📌 Planning the change
📌 Implementing it
📌 Reviewing its effectiveness
📌 Taking corrective action
The Four Stages of the PDCA Cycle
The PDCA Cycle is broken down into four core stages, each designed to tackle and improve your project management lifecycle systematically.
Here’s how each step functions:
Stage 1: Plan
In the planning phase, the focus is on identifying the problem and planning a solution. It involves understanding the root cause of the issue, setting clear objectives, developing a strategy for implementing a solution and documenting the process.
💈Bonus: Use ready-made process improvement templates to save time with a structured framework from the start. They simplify task organization, ensure consistent documentation, and make it easy for your team to standardize improvements so nothing is missed in your PDCA cycle.
Stage 2. Do
Here, the plan is put into action, often on a small or pilot scale, to minimize potential risks. This controlled implementation lets teams observe how well the change works in real time and make adjustments as needed.
💈Bonus: Begin with a test run to spot any hiccups early. See which process in your project management lifecycle desperately needs change and test your plan on it. By testing on a small scale, you can spot and fix any issues without impacting the entire operation.
Stage 3. Check
At this stage, your team is able to review the results and see if the desired improvement has been achieved.
By collecting and analyzing data, your team determines whether the change was effective or if adjustments are needed. This step is key to validating the results and guiding future actions.
💈Bonus: Use KPIs and performance metrics to measure the success of your pilot. Reviewing expected results now helps prevent scaling issues later, so analyze outcomes thoroughly to avoid surprises in the full rollout. It’s the project manager’s way of saying, “Trust, but verify!” 🕵️
Stage 4: Act
Based on the review in the Check phase, the team can decide whether to implement the change on a larger scale or make further adjustments. If the pilot is successful, the change can be standardized; if issues are discovered, the team can revisit the Plan stage to refine the approach.
💈Bonus: Standardize what works and adjust where needed. Document changes and create SOPs (Standard Operating Procedures) for future reference, ensuring consistency across the board. Think of it as building a “best practices” manual for your next project phase! 📖
Here’s a visual representation of the process to help you break it down further:
💭 Example of PDCA cycle implementation
Plan: A manufacturing company notices an increase in product defects. As part of its total quality management efforts, the team analyzes the data, identifies a flaw in the assembly process, and plans a modification to improve product quality
Do: The team modifies the assembly line for one product batch, observing if the defect rate decreases without affecting production time or cost
Check: The defect rate dropped by 30% in the pilot batch, but they also noted some unexpected delays due to the new setup
Act: Seeing success in defect reduction, the team refines the new assembly process to minimize delays and then rolls it out across all production lines
Benefits of the PDCA Cycle
A McKinsey Global Survey found that organizations pursuing comprehensive, staged improvements are three times more likely to succeed in their transformations.
The PDCA cycle brings a unique, action-oriented approach to business process improvement that goes beyond the basics. It helps teams enhance problem-solving and create adaptable workflows.
Here’s how:
- Built-in problem solving: The cycle’s iterative structure allows teams to address issues methodically, breaking complex problems down into manageable steps. This structure turns problem-solving into a repeatable process rather than a one-time fix
- Encourages ‘test and learn’ culture: By testing on a small scale in the Do stage, teams gain a safe space for innovation. This culture encourages experimentation and agility, making teams more adaptable in the face of change
- Prevents burnout: Rather than overwhelming teams with large-scale changes, PDCA promotes small, consistent improvements that keep momentum without exhausting resources or people
- Reduces risk of blind spots: Studies show that a quarter of transformation value is lost in the target-setting phase alone. PDCA’s Check phase mitigates this by continually validating and refining outcomes so issues don’t go unnoticed or unresolved
- Improves team engagement: Data shows that successful transformations often hinge on engaged frontline employees—teams connected directly to the process. PDCA fosters involvement at each stage, assigning clear responsibilities and promoting sustained team engagement
Bring the PDCA Cycle to Life For Continuous Improvement
The PDCA cycle, much like a PDSA cycle, offers a simple and repeatable approach to implementing change effectively. Here’s how you get started:
Step 1: Set up your team for success
Preparing your team to embrace the PDCA cycle involves more than explaining the steps. It’s about building understanding and enthusiasm for continuous improvement in your processes.
Begin by educating your team on each PDCA stage, emphasizing how each step empowers them to make iterative but impactful, measurable changes. Incorporate hands-on project knowledge training sessions so they get to implement change at a small scale and see the process in action.
A productivity platform like ClickUp eases your team’s adoption of PDCA.
Use this all-in-one project management tool to create a clear roadmap, ensure access to relevant documents, and track each phase smoothly so your team navigates the cycle seamlessly. Here’s how Clickup helps specifically at this step:
Build a PDCA roadmap with ClickUp Docs and Checklists
Start with a ClickUp Doc to outline the process and make training materials accessible. ClickUp Docs lets you create detailed, interactive resources with nested pages and embedded checklists.
With this feature, you get to:
- Build a comprehensive PDCA guide with nested pages for each stage, including objectives, tasks, and management practices
- Tag team members in comments or assign action items directly within the document
- Collaborate live on the Doc so changes, feedback, or updates are instantly visible
Step 2: Pinpoint where the PDCA method is needed
Choosing the right projects for PDCA implementation is essential for maximizing impact with sustainable improvements. This means identifying areas for improvement to address persistent project management challenges and enhance efficiency.
For example, a retail company might choose to implement the PDCA cycle in its inventory management process to reduce stockouts and overstock, leading to smoother operations and cost savings.
Go granular with ClickUp Custom Fields
With ClickUp Custom Fields, you can add specific data points—such as potential impact, urgency, and complexity—to each project, creating a tailored evaluation framework. This makes prioritizing projects easy based on custom criteria that align with your improvement goals.
With this feature:
- Assign impact levels to potential PDCA projects to easily identify high-priority areas
- Track resource needs and costs by adding Custom Fields, helping assess each project’s feasibility
- Set KPI fields to monitor project outcomes, keeping performance metrics clear in the Check phase
- Designate task owners to ensure accountability at each PDCA stage and streamline follow-through
Step 3: Stick to the right tools and resources
Implementing the PDCA cycle requires the right tools to support, automate, and track each stage. The right resources enable teams to manage tasks effectively, streamline processes, and monitor time investment—all essential for an efficient, continuous improvement cycle.
Here’s how ClickUp’s features support this step in the PDCA process:
Build your PDCA blueprint with ClickUp Task Management
ClickUp’s Task Management feature provides a solid foundation for structuring each PDCA phase. With customizable and adaptable tasks, teams can create specific tasks for every stage, from the planning phase to executing actions for desired results.
This feature allows you to:
- Create tasks for each PDCA phase, assign priorities, and link related tasks to keep the cycle organized and focused
- Add fields like deadlines and impact levels, and assign items to team members responsible for specific steps. Break tasks into smaller subtasks and checklist items
- Set dependencies between tasks, ensuring that each PDCA stage progresses sequentially and nothing gets missed
Use ClickUp’s Task Checklists to outline action items within each individual task. This enables you to track task completion within each PDCA phase, ensuring accountability. These tools support an interactive approach to learning and allow teams to stay engaged while tracking progress through each improvement cycle.
Here’s what all you get to do with the ClickUp Checklists:
- Assign checklist items to team members from the ClickUp Tasks, ensuring each part of the process is covered
- Save checklist templates for recurring tasks within the PDCA cycle to standardize workflows
- Use nested checklist items to add further detail to each task
Let routine work run itself with ClickUp Automation
ClickUp Automation reduces the manual work in the PDCA cycle, letting you focus on meaningful improvements while automating repetitive tasks. With automation, your team can streamline transitions between PDCA stages and stay on track without the busy work.
Here’s how ClickUp’s Automations support PDCA:
- Automate status updates and notifications to keep the team informed as each PDCA stage progresses
- Use dynamic assignees to automatically direct tasks to the relevant team members as stages advance
- Set reminders for regular reviews in the ‘check phase,’ prompting timely evaluations and keeping the PDCA cycle on schedule
Keep an eye on every minute with ClickUp Time Tracking
ClickUp’s Time Tracking offers a transparent view of how resources are allocated throughout each PDCA stage, helping teams optimize efficiency and plan strategically for future cycles. By monitoring time spent, you gain valuable insights into resources across the improvement process.
Here’s how it enhances your PDCA cycle:
- Track time spent on each PDCA phase to identify areas that may benefit from process adjustments
- Add notes to time entries for added context, helping the team understand what was completed
- Compare tracked time with initial estimates to enhance planning future cycles
Step 4: Implement the PDCA cycle
Monitoring progress, analyzing results, and adjusting strategies are crucial to fully integrating the PDCA cycle. The cycle requires ongoing evaluation and modification to drive continuous improvement.
Here’s how ClickUp makes each phase of PDCA implementation effective.
Use Gantt Charts to visualize and track
ClickUp’s Gantt Charts allow you to see timelines, dependencies, and critical paths in one view. This visualization highlights project flow, timelines, and areas that may need attention, helping you manage PDCA initiatives efficiently and ensuring no steps are overlooked.
Using ClickUp Gantt Charts:
- Map each PDCA stage to visualize the cycle’s flow from plan to act phase in one timeline
- Link dependencies between stages to ensure tasks progress sequentially, avoiding skipped steps
- Mark timelines and deadlines to set clear expectations and keep each PDCA phase on track
Monitor progress with ClickUp Dashboards
ClickUp Dashboards provide a centralized view of your PDCA progress, helping you monitor key metrics in real time. Customize your dashboard with charts, lists, and data to track task completion, performance, and critical milestones.
With these insights, teams gauge effectiveness, identify issues, and celebrate achievements at each PDCA stage.
With the ClickUp Dashboards, you can:
- Visualize success metrics and track changes and outcomes at each phase
- Centralize data and task metrics for a high-level view of project health
Here’s why users are loving this feature 🚀
Enhance PDCA planning with ClickUp’s PDCA Process Whiteboard Template
ClickUp’s PDCA Process Whiteboard Template is an interactive tool for managing the cycle visually. This template organizes tasks into the ‘Plan-Do-Check-Act’ structure, making it easy to track each step’s progress and collaborate in real time.
Empower your Plan Do Check Act process with this template by:
- Visualizing each PDCA stage on the whiteboard for clear tracking and team alignment
- Collaborating in real-time with team members to align each PDCA stage
- Switching views seamlessly to track tasks visually or in detailed lists
- Capturing decisions and changes with embedded notes to guide future cycles
PDCA vs. Other Improvement Methodologies
The PDCA Cycle, Lean, Six Sigma, and Agile all continuously improve processes and deliver better results, yet each has distinct approaches and advantages.
Here’s how PDCA compares with these popular project management methodologies:
Methodology | Approach | Pros | Cons |
---|---|---|---|
PDCA | Iterative cycle of Plan, Do, Check, Act to solve problems and drive continuous improvement | Simple and adaptable; excellent for continuous, small-scale improvements; encourages team engagement at each stage | May be slower for large-scale changes; relies heavily on effective implementation of each phase |
Lean | Focuses on reducing waste and maximizing value with streamlined processes | Improves efficiency; reduces waste significantly; ideal for industries aiming to optimize resources | May overlook quality control aspects; less effective if not fully embraced as a cultural change |
Six Sigma | Data-driven approach to minimize defects and improve quality using statistical analysis | Excellent for process standardization and quality control; Tools like the SIPOC template provide a clear view of processes and make it easier to identify areas for improvement | May be complex; requires specialized knowledge and training in statistical methods |
Agile | Flexible, iterative approach with short cycles (sprints) focused on delivering incremental improvements | High adaptability; great for projects requiring regular feedback and adjustments; promotes teamwork and fast response to change | Best suited for software development; less effective for processes that require consistent standardization |
Pros and cons of PDCA compared to other methodologies
Pros
- Flexibility and simplicity: Unlike Lean or Six Sigma, PDCA is easy to adopt and can be applied across various industries without intensive training
- Encourages continuous learning: PDCA’s iterative process supports ongoing improvement, ideal for organizations seeking gradual process evolution
- Broad applicability: Works well in a wide range of settings, from small teams to large organizations, without the need for specialized knowledge
Cons
- Less precise in data-driven environments: Compared to Six Sigma, PDCA lacks a rigorous statistical foundation, making it less suitable for high-stakes quality control
- Limited for large-scale changes: PDCA is slower to implement on a large scale compared to Agile, which can pivot quickly and deliver faster iterative results
- Dependency on feedback loops: For PDCA to succeed, strong and consistent feedback is essential, which may not always be feasible in fast-paced or resource-limited environments
Supercharge Your Internal and External Processes With ClickUp
The PDCA Cycle gives businesses a straightforward approach to process improvement, helping teams evolve without the need for complicated systems or extensive training.
Its cyclical nature makes it ideal for organizations committed to continuous learning and incremental progress, supporting adaptability in changing environments.
The PDCA cycle is powerful on its own, but when paired with ClickUp, it becomes a potent, fully supported process. ClickUp makes each PDCA stage—from project planning to acting—more organized, efficient, and collaborative.
Whether you’re tracking progress, adapting to feedback, or visualizing improvement steps, ClickUp ensures every part of your process is covered. Ready to simplify your improvement journey? Get started with ClickUp for free today!