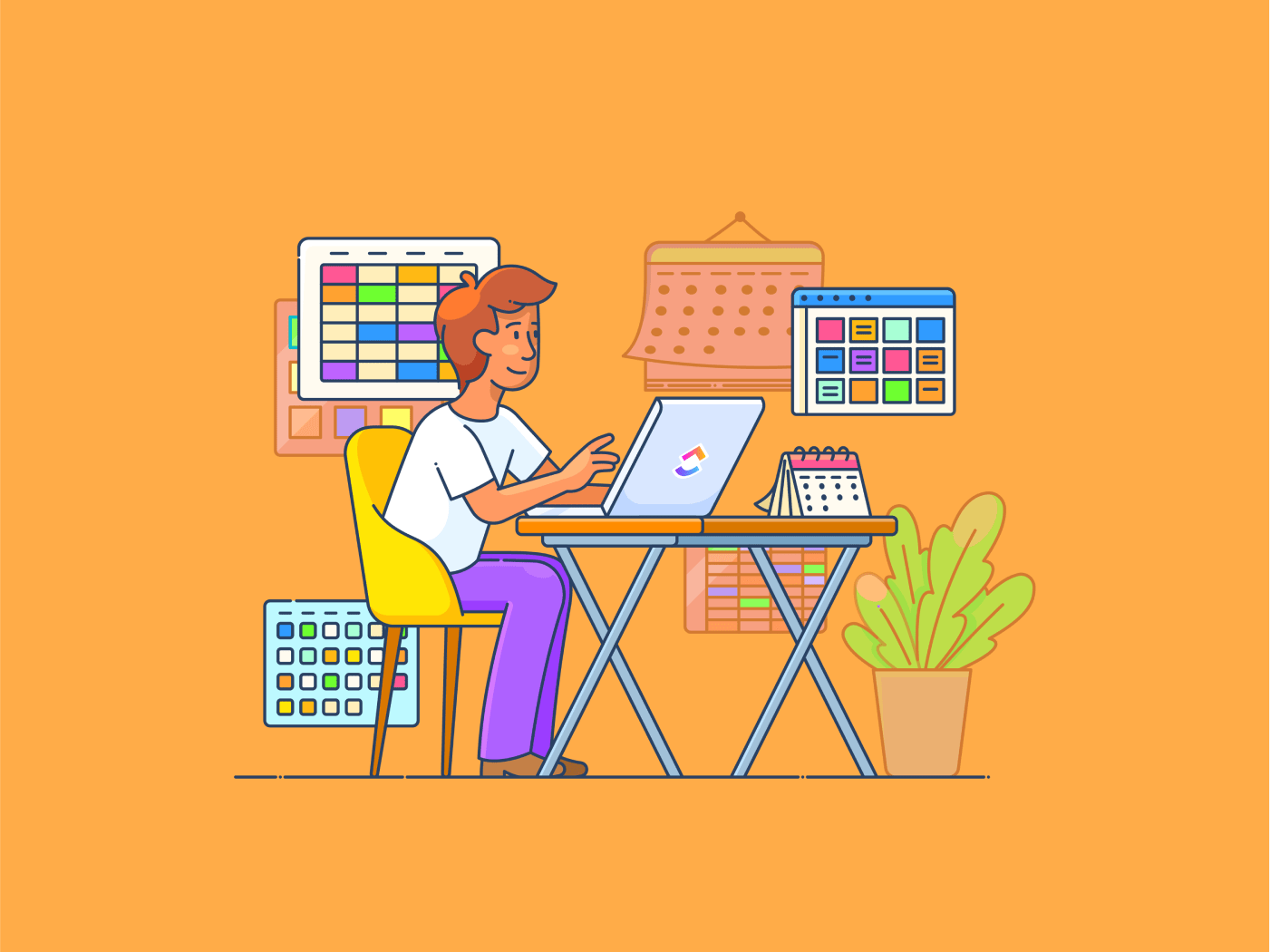
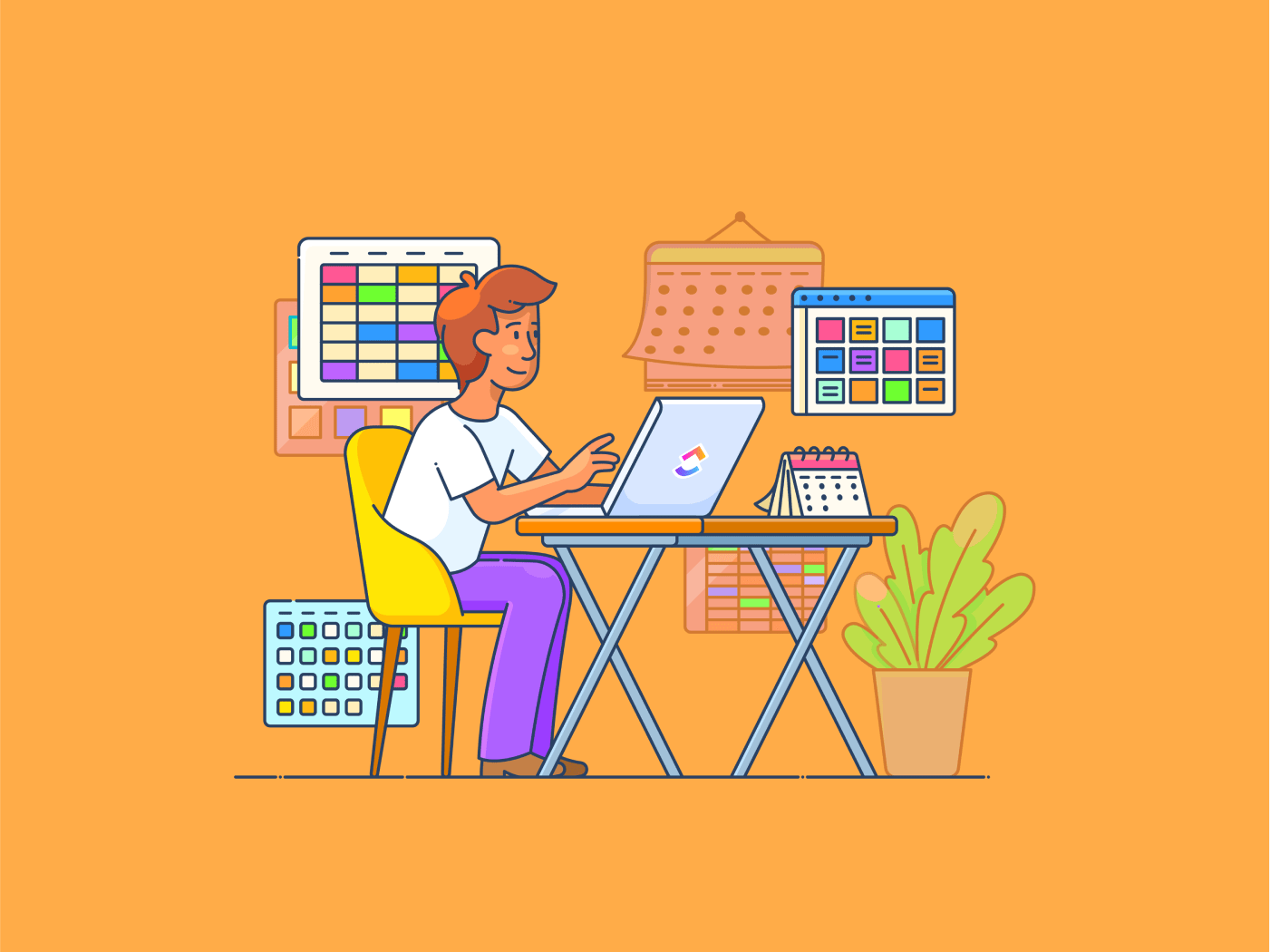
A smartphone today packs unimaginable storage capacity that would have taken up many rooms full of computers just 20 years ago—a transformation that did not happen overnight.
It happened due to an iterative process, which focuses on small changes that you can continue making to evolve your product or processes. This helps create outstanding technological advancements that make the world look on in awe.
Any organization must today follow the iterative process of continuous improvement. History offers many examples of companies that once dominated their markets but failed to adapt when competition advanced and were either rendered obsolete or died out. Organizations today need to evolve with market changes or risk obsolescence.
The lesson here is to incorporate continuous improvement to eliminate inefficiencies from your processes.
In this blog, we’ll explore the world of continuous improvement processes, its core principles, and the benefits they can bring to your business goals.
- What is Continuous Improvement?
- Frameworks for Continuous Improvement
- Continuous Improvement Examples in Software Development
- Challenges in Continuous Improvement
- Implementing Continuous Improvement in Organizations
- Implement Continuous Improvement Process for Your Organization With ClickUp
- Frequently Asked Questions (FAQ)
What is Continuous Improvement?
Imagine a never-ending loop of progress, where every step forward informs the next, and every project completed becomes a stepping stone to even greater achievements. That’s the essence of continuous improvement, an iterative process that slowly refines existing processes, workflows, and practices.
The continuous improvement process is a company-wide philosophy that encourages everyone to be on the lookout for ways to improve quality, efficiency, and overall performance.
The roots of process improvement can be traced back to Japan, which pioneered the concept of Kaizen. It is a Japanese term for continuous improvement efforts, which served as the basis for Japanese philosophy and business culture.
There are nine basic principles of continuous process improvement:
- Define how work is being done today: To identify areas for improvement, we need to assess the organization’s current processes. This involves discovering, documenting, and digitizing all your business processes into a single solution
- Understand your problems and define the goals: Define the desired outcome or goals from your processes. This helps to understand what you hope to improve upon and define the scope of your improvement projects
- Connect process improvement initiatives to your goals: Once your objectives are defined, start implementing process improvement initiatives to match your overarching business objectives, which can be cost reduction, digital transformation, achieving operational efficiency, eliminating waste, or others
- Define process owners: After creating your process improvement plan, involve subject matter experts (SMEs) as necessary. Also, define owners for each process or activity. This helps each team member understand their contribution and take ownership of the goal
- Empower employees: Empower your team to identify and implement improvements
- Focus on incremental improvements: Instead of trying to make a massive overhaul all at once, try to implement changes gradually by taking small steps toward the larger goal
- Continuous process improvement: After achieving your original target, use the Kaizen principles to continue making iterative progress. This gradually helps you transform your systems and processes to the desired level
- Measure, monitor, and repeat: These are the key pillars of any continuous improvement plan. By continuously measuring and monitoring the impact of your improvement projects, you can smoothly manage business operations and remain competitive even in an evolving market
Frameworks for Continuous Improvement
Now that we have understood how the overall process improvement process works, here is a look at some of the frameworks for process improvements:
The Lean methodology
The Lean methodology focuses on minimizing waste and maximizing value in every step of the production process. This approach was pioneered by Japanese carmaker Toyota as the Toyota Production System and gradually developed into today’s Lean.
In this methodology, the typical process is as follows:
- Specify value: Identify what truly matters to your customers and what constitutes value in your product or service.
- Identify steps in the value stream: Visually track all the steps involved in delivering your product or service, highlighting any waste or inefficiency
- Create flow: Optimize the production process to eliminate delays and ensure a smooth, uninterrupted flow of work
- Establish pull: Traditionally, production is often based on forecasts or estimations. Lean flips this concept to a ‘pull’ system. Here, production is triggered by actual customer demand. This means only what’s needed, and when it’s needed, is produced, avoiding excess inventory and waste
- Seek perfection: Continuously strive to improve processes, eliminate waste, and enhance customer value through ongoing evaluation and adaptation
In software development, Lean principles can be applied to simplify workflows, eliminate unnecessary features, and optimize resource allocation.
Six Sigma philosophy
Similar to the Lean methodology, this data-driven approach emphasizes defect prevention and process improvement through statistical analysis. Six Sigma can be used in any business or industry to identify and create avenues for process improvements.
The Six Sigma approach follows this basic framework:
- Define: Identify the issue and set measurable goals. What process needs improvement? What are the customer needs or expectations that aren’t being met? What specific outcomes do you want to achieve? Make sure you can answer these questions and set clear and measurable goals to achieve them with project improvements
- Measure: Define how you’ll track progress and start gathering data on the current performance of your process. This data will serve as a benchmark to measure future improvements against
- Analyze: Use data analysis tools to understand the root causes of the problems identified in the Define phase. Why are defects occurring? What factors are contributing to inefficiencies? Go deep into the analysis phase to identify underlying issues and factors that can be causing these issues
- Improve: Evaluate the effectiveness of your implemented solutions. Did they achieve the desired results? Are there unintended consequences? Based on your analysis, brainstorm and fine avenues to make improvements in your process
- Control: Continuously monitor the performance of the improved process using your defined metrics. Look for further opportunities to refine and optimize the process over time
Bonus: Learn about adaptive project management!
PDCA (Plan-Do-Check-Act)
PDCA is another popular approach to process improvement. Also called the Deming cycle, it follows the following framework:
- Plan: Identify an area for improvement, define clear goals, and develop a plan for change
- Do: Implement the change on a small scale to test its effectiveness
- Check: Analyze the results of the change and measure its impact
- Act: Based on your analysis, either standardize the successful change or adapt and try again
The Plan-Do-Check-Act cycle promotes a culture of experimentation and iteration, allowing you to refine your approach and achieve operational excellence continuously.
Difference between continuous improvement and traditional improvement methods
Traditional improvement methods often focus on one-time fixes or major overhauls. Continuous improvement, in contrast, is a never-ending process of small, incremental changes. Some of the differences between these two theories include:
Feature | Continuous Improvement | Traditional Improvement Methods |
Focus | Ongoing process of small, incremental improvements | One-time fixes or major overhauls |
Goal | Continuously improve efficiency, quality, and performance | Address specific problems or inefficiencies |
Culture | Collaborative, data-driven, learning-oriented | May be a siloed, top-down approach |
Pace of change | Slow and steady, iterative | Can be rapid but less sustainable |
Data usage | Highly data-driven, with ongoing measurement and analysis | May rely less on data and metrics |
Employee involvement | Empowers employees to identify and implement improvements | Limited employee involvement |
Flexibility | Adapts easily to changing circumstances | May be less flexible and adaptable |
Risk | Lower risk due to small, incremental changes | Higher risk due to larger-scale changes |
Examples | Lean manufacturing, Agile development, Kanban, PDCA cycle | Reorganizing a department, implementing a new software program (without ongoing improvement) |
Continuous Improvement Examples in Software Development
Now that we have understood process improvement concepts and methodologies, let us look at some process improvement examples that can be implemented in business processes:
Lean software development
As mentioned earlier, Lean principles are potent tools for continuous improvement in software development. They focus on delivering maximum value to the customer while enabling waste reduction. They emphasize a collaborative and iterative approach, breaking down projects into smaller, manageable chunks and prioritizing features that deliver the most value to the end user.
A great example of Lean software development is the MoSCoW approach, which breaks down critical functions into:
- Must-Have
- Should-Have
- Could-Have
- Won’t-Have
This approach helps prioritize activities based on the above categories—enabling a smooth, continuous improvement workflow.
Agile software development
Another cornerstone of continuous improvement in software development and operations management is the Agile methodology. Agile is a flexible and iterative approach that prioritizes collaboration, rapid feedback, and continuous adaptation.
It breaks down projects into manageable ‘sprints’ with clearly defined goals. Teams work collaboratively in short cycles, constantly refining the product based on user feedback and ongoing testing. This allows for faster course correction and ensures the final product remains relevant and user-centric.
Scrum
Scrum, a popular Agile framework, provides a specific structure for iterative development and continuous improvement. It takes a time-boxed approach, with projects divided into short sprints (typically 1-4 weeks) where focused work occurs.
Each sprint has a defined goal, and the team works collaboratively to achieve it. Scrum emphasizes roles like the Product Owner (who prioritizes features), the Development Team (who builds the product), and the Scrum Master (who facilitates the process).
Kanban
Kanban development offers another Agile framework that thrives on continuous improvement principles. It utilizes a visual workflow management system, typically a Kanban board with columns representing different stages of development (e.g., To Do, In Progress, Done). Tasks are represented by cards that move across the board as work progresses. Kanban focuses on limiting work in progress (WIP) to avoid bottlenecks and ensure a smooth workflow.
Iterative and incremental development
Iterative and incremental development involves breaking down projects into smaller, manageable pieces.
Each iteration focuses on delivering a functional increment of the product, gathering user feedback, and incorporating that feedback into subsequent iterations. This allows for continuous refinement and ensures the final product aligns with user needs.
Iterative and incremental development are most popular in product development. The first iteration is the minimum viable product (MVP), which includes the core functionalities. This is released, and then incremental updates are added to this product after gathering user feedback and prioritizing development efforts.
The role of quality assurance and usability testing in continuous improvement
While development methodologies like Agile and Scrum provide a framework for continuous improvement, it’s crucial to have mechanisms in place to ensure quality throughout the process. This is where quality assurance (QA) and usability testing come into play:
- Quality assurance (QA): QA specialists act as a safety net, meticulously testing the software for bugs, performance bottlenecks, and security vulnerabilities. By identifying and resolving issues early, QA plays a vital role in preventing defects from reaching later stages of development, saving time and resources
- Usability testing: Usability testing involves observing real users interact with the software and identifying any usability issues or areas for improvement. By understanding how users interact with the product, teams can continuously refine the user interface and user experience, ensuring the final product is functional, intuitive, and user-friendly
QA and usability testing provide valuable data and insights that fuel continuous improvement. By identifying bugs, performance issues, and usability problems early and often, teams can continuously iterate and refine the software, leading to a higher-quality and more user-friendly product.
Challenges in Continuous Improvement
Since process improvement focuses on continuous change, it can face several roadblocks. Some of the most common challenges include:
Resistance to change
Many organizations have existing processes that were created after several rounds of trial and error. These processes use existing frameworks and technology to get the job done, making them not so easy to replace. For example, many traditional banks using legacy mainframe infrastructure tend to resist digitizing banking processes since it could create many disruptions. Existing teams have to be upskilled and trained to work with these new technologies, and these changes can bring significant disruption to the overall banking process.
Solution: To go beyond this resistance, organizations must create a continuous improvement culture while clearly communicating the ‘why’ behind any improvement processes. Introduce subtle changes and build incrementally to ensure that this resistance can be overcome.Â
Bottlenecks in production
In most organizations, production processes are interdependent. So, if one task is delayed or stuck, it will hinder overall progress in every task that depends on the successful completion of the former. This is a bottleneck and causes significant challenges in the continuous improvement cycle.
Solution: Â To address this, organizations can use automation software or process mapping tools to track and automate simple tasks and identify task dependencies, thereby improving efficiency.
You can use the ClickUp Gantt chart view to understand the relationship between each activity and map dependencies. It helps you visualize task dependencies, clearly showing how tasks rely on each other’s completion. This helps identify potential bottlenecks and plan accordingly.
Lack of visibility
Imagine navigating a complex improvement project without a clear view of progress, resource allocation, or other critical data. This is the reality when visibility is limited. Lack of visibility can lead to:
- Misinformed decisions: Without a real-time grasp of project progress, leaders might make decisions based on outdated information, leading to inefficiencies and missed opportunities
- Resource mismanagement: Unclear resource utilization can overload some team members while others remain underutilized. This creates an unbalanced workload and hinders overall efficiency
- Missed opportunities: Limited visibility makes it difficult to identify roadblocks or areas for improvement early on. By the time issues become apparent, they can snowball into bigger problems
Solution: Â To ensure that you have detailed insights into your processes, implement data collection and reporting systems to gain clear visibility into project progress, resource utilization, and other key metrics.
Insufficient clarity
Another issue that can cripple processes is the insufficient clarity on individual roles, team goals, and priorities. This can lead to several issues:
- Disengaged employees: Unclear expectations and goals leave employees feeling lost and unsure of how their work contributes to the bigger picture. This can lead to disengagement and a lack of ownership in the improvement process
- Duplication of effort: If roles and responsibilities are undefined, individuals might unknowingly duplicate efforts, or tasks may fall through the cracks. This wastes valuable time and resources
- Misaligned priorities: When everyone has their own interpretation of priorities, conflicting efforts may arise, hindering progress toward the shared goal
Solution: Â To avoid this issue, organizations must clearly define roles, responsibilities, and organizational goals to ensure everyone is on the same page.
By communicating the goals and creating avenues for open communication, you can generate relevant feedback and address any lingering confusion that could dismantle the entire project.
Inventory management challenges
A smooth-running improvement process relies on having the necessary resources readily available. Inefficient inventory management can lead to several issues:
- Running out of essential materials can halt progress and disrupt your improvement initiatives
- Waiting for supplies to arrive can significantly delay improvement efforts
- Overstocking can tie up valuable resources and create additional storage and management burdens
Solution: Â Use tools to track, manage, and optimize inventory levels.
With ClickUp, you can customize and track inventory levels, creating custom fields for quantity, reorder points, and other relevant information. The tool also includes ready-to-use templates, such as the Inventory Management Template, to help you stock, reorder, track order statuses, manage vendors and costs, and more. The advanced template helps you to:
- Track inventory levels, stock availability, stock movements, and costs
- Organize product information like pricing and images
- Analyze inventory trends and make data-driven decisions about restocking and other requirements
Organizations can leverage iterative improvement cycles and on-ground training to obtain the required resources for improvement processes. This enables the organization to scale or adapt to the evolving needs of a continuous improvement mindset.
Implementing Continuous Improvement in Organizations
Continuous improvement isn’t just about methodologies and tools. It takes a combined effort to foster a culture that embraces ongoing learning and implementing automated workflows. Here’s how to create an environment where continuous improvement thrives:
- Focus on continuous change management: Invest in employee training programs and learning methodologies that equip your team with the skills and knowledge needed to identify and implement improvements
- Enhance efficiency by improving employee retention and onboarding process: A stable, experienced team is essential for continuous improvement. By streamlining onboarding processes, you foster a culture of continuous improvement from the get-go. This helps new hires understand the importance of continuous improvement and makes it a part of your company’s culture. This can also help with employee retention, as once the employee is fully onboarded, having a positive organizational culture with well-defined processes helps to retain employees for longer
- Gather feedback for improving customer satisfaction: Process improvement isn’t just about improving internal processes but also about enhancing customer experience. Actively seek customer feedback through surveys and user interviews to gain actionable insights into how you can improve your products, services, or business processes. You can use the ClickUp Form view to easily capture feedback, organize it, and turn it into actionable goals. This also encourages your team to voice their concerns and turn their feedback into tasks for efficient management
- Enhance user experience: Prioritize user experience throughout the development process. Especially if you have a digital platform, you need to ensure that your digital solutions are built keeping your customers in mind
- Vendor management: Continuously evaluate your vendors and identify opportunities for better pricing or service quality
- Performance reviews and updates: Monitor and track your processes to identify areas that require improvement, gather valuable insights into your overall efficiency, and take your output to the next level. For this, you can leverage ClickUp Brain, a built-in AI assistant that can help you analyze data and automate tasks. This allows you to automate action items and subtasks and even fetch the right details from your docs, projects, and company wikis
Using these strategies, you can empower your team to implement continuous improvement methodologies in your business process. ClickUp, an all-in-one project and process management software, equips you with a powerful arsenal of features designed to make continuous improvement an intuitive and collaborative endeavor.
This unique platform allows you to get all your data in one place, enabling you to gather the required information, prepare plans, and adapt or refine your approach. This gives you the flexibility and agility you need to learn, iterate, and continuously achieve lasting success.
ClickUp helps you visualize your improvement journey, allowing you to:
- Track progress with ClickUp Dashboards, your fully customizable mission control center. This allows you to gain a real-time snapshot of key metrics, progress on improvement initiatives, and potential bottlenecks
- Collaborate with your teams to build new ideas and have effective brainstorming sessions with ClickUp Whiteboards. You can use sticky notes, mind maps, and other visual elements to capture ideas and organize them into a cohesive plan
- Create trackable goals using ClickUp Goals to hit your objectives with clear timelines and measurable targets, and assign action items to your teams
- Leverage ready-to-use process improvement templates and frameworks for conducting effective project retrospectives, a cornerstone of continuous improvement. The ClickUp Project Retrospective Template guides your team through a retrospective process, allowing you to identify areas for improvement, brainstorm solutions, and define action items for future iterations
Implement Continuous Improvement Process for Your Organization With ClickUp
Continuous improvement is a consistent quest for excellence. By embracing this method and implementing the strategies outlined above, you can empower your team to achieve remarkable results.
By combining ClickUp’s features with these strategies, you can transform your approach to continuous improvement. Ready to take the first step towards continuous improvement?
Sign up for your free ClickUp account today and implement continuous improvement effectively within your team!
Frequently Asked Questions (FAQ)
1. What is continuous improvement in the workplace?
Continuous improvement is a company culture that focuses on constantly refining processes, workflows, and practices to achieve better results and build innovative solutions. It involves strategies and methodologies that encourage all employees to identify inefficiencies and seek ways to improve efficiency, quality, and overall performance.
2. What are examples of continuous development in the workplace?
There are numerous examples of continuous improvement across various departments. Here are a few examples specific to software development:
- Implementing Agile methodologies like Scrum or Kanban to break down projects into smaller, manageable tasks and iterate based on feedback
- Automating repetitive tasks with ClickUp automation to free up developer time for more strategic work
- Utilizing ClickUp Dashboards to visualize workflows, identify bottlenecks, and optimize resource allocation
- Conducting regular code reviews to identify and fix bugs early in the development process
- Encouraging employee feedback through surveys or suggestion boxes to gather ideas for improvement
3. How can I improve my continuous improvement?
To improve continuous improvement processes within your organization, you can do the following:
- Set clear goals and objectives to provide direction and focus for improvement efforts.
- Track and measure results to assess the effectiveness of implemented changes
- Foster a culture of open communication where employees feel comfortable sharing ideas and concerns
- Invest in training and development to equip employees with the skills and knowledge needed to identify and implement improvements
- Utilize process mapping tools like ClickUp to brainstorm ideas, build vision maps, create tasks from notes, and track goals efficiently