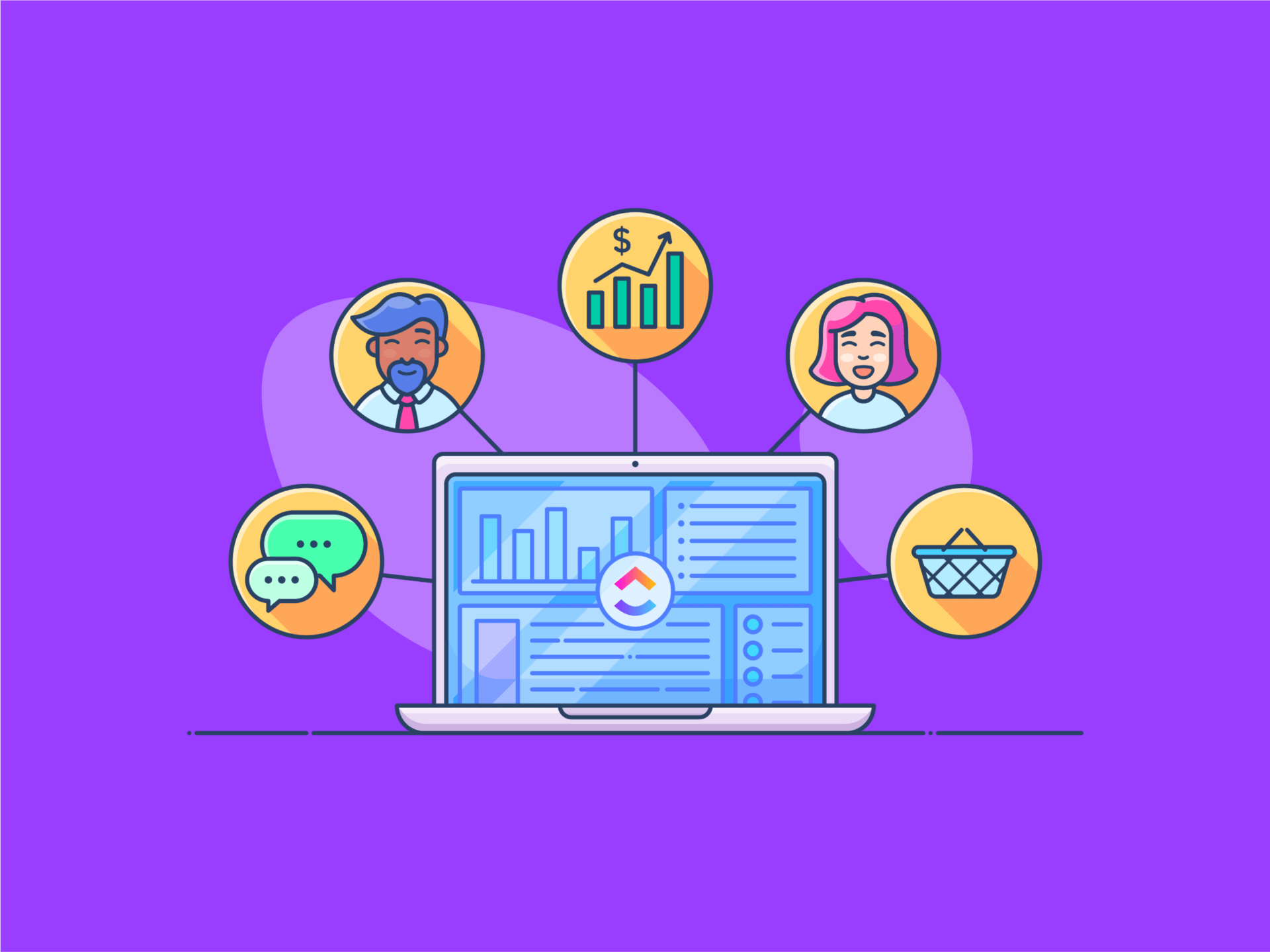
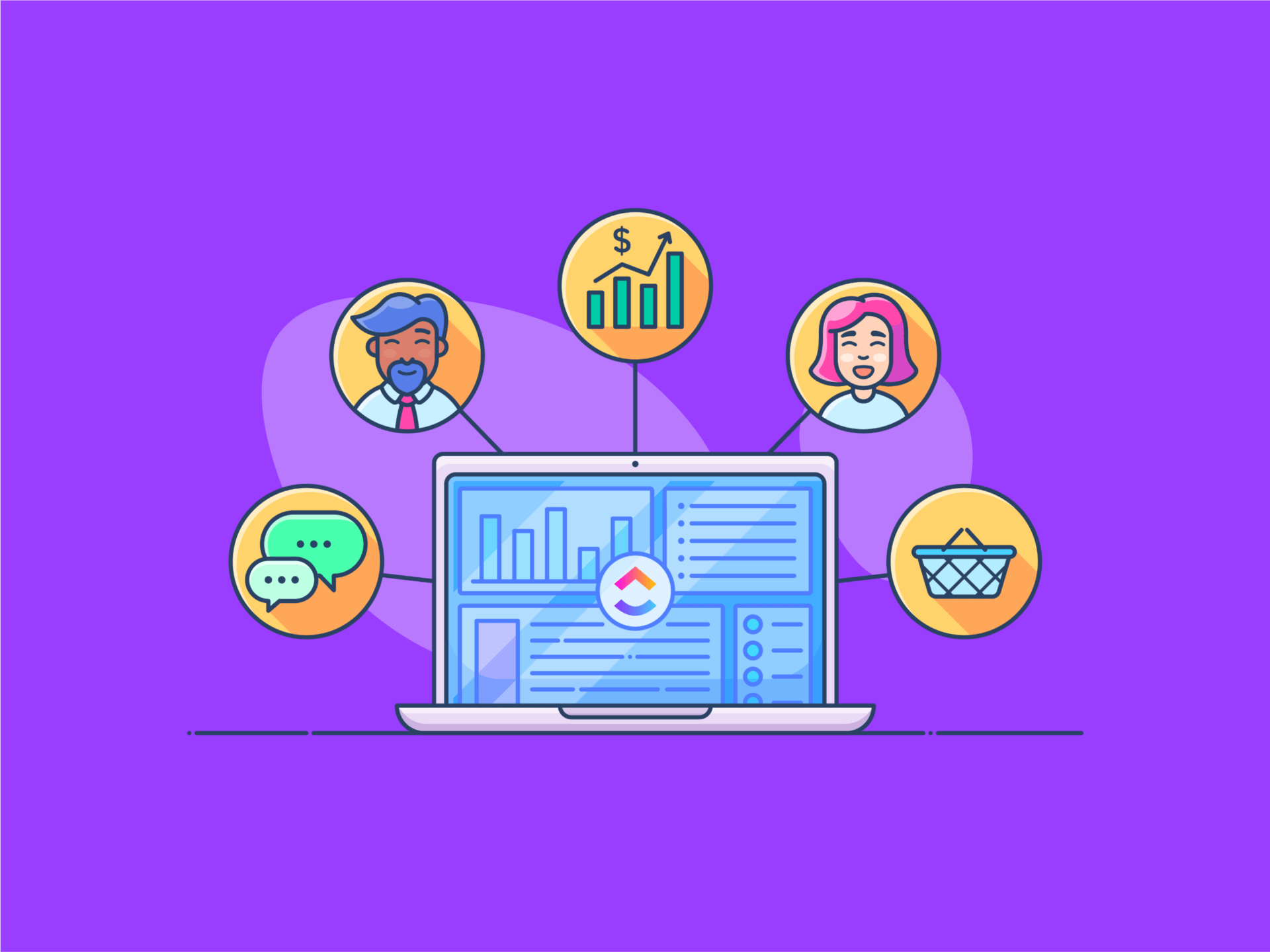
Organizations globally invest $48 trillion in projects annually, but only a fraction achieve success. This highlights the urgent need for advancement in enterprise project management practices.
In the manufacturing industry, the most important functions depend on effective project management. For example, ensuring operational efficiency, meeting production deadlines, and maintaining high-quality standards
So, manufacturing project management requires a unique blend of skills, tools, and strategies tailored to the industry’s needs. Let’s explore these nuances and understand the roles, stages, and tools essential for success.
Understanding Project Management for Manufacturing
Manufacturing project management is the process of planning, coordinating, and overseeing projects within the manufacturing industry to achieve specific objectives, such as product development, process improvement, or facility expansion.
This specialized form of project management integrates various functions, such as procurement, production, and logistics, to deliver projects on time and within budget.
Manufacturing project management is crucial for several reasons:
- Efficiency: Streamlining operations to reduce waste and optimize resource management and utilization
- Quality control: Ensuring products meet stringent industry standards
- Cost management: Keeping manufacturing projects within budget while maximizing returns
- Innovation: Facilitating the development of new products and processes
Examples of manufacturing projects
These are some of the examples of project management in manufacturing:
1. New product development: Designing and launching a new product line
Example: Developing and launching a new line of energy-efficient washing machines. This would include the following key project management considerations:
- Clearly defining product requirements and specifications
- Coordinating cross-functional teams (R&D, engineering, manufacturing, marketing)
- Implementing stage-gate processes to manage the development lifecycle
- Ensuring seamless transition from prototype to full-scale production
- Conducting thorough testing and quality control measures
- Aligning launch timing with market demand and sales/distribution channels
2. Facility expansion: Constructing new manufacturing plants or expanding existing ones
Example: Constructing a new manufacturing plant to increase production capacity for automotive parts. This would include the following steps:
- Site selection and feasibility analysis
- Obtaining necessary permits and approvals
- Designing the facility layout and workflow for optimal efficiency
- Coordinating construction, equipment installation, and facility commissioning
- Recruiting and training the new workforce
- Integrating the new facility with existing operations and supply chain
3. Process improvement: Implementing lean manufacturing techniques to enhance productivity
Example: Implementing lean manufacturing techniques to reduce waste and improve productivity in an electronics assembly line. This would involve:
- Conducting a thorough assessment of current processes and identifying areas for improvement
- Engaging cross-functional teams to develop and test lean solutions (e.g., 5S, Kaizen)
- Providing training and change management support to ensure successful adoption
- Closely monitoring and measuring the impact of process improvements
- Continuously refining and optimizing the new Lean manufacturing system
4. Technology upgrades: Integrating advanced technologies, such as automation and robotics, into production processes
Example: Integrating advanced robotics and automation into a plastics manufacturing facility. This would include:
- Identifying the business processes and manufacturing workflows to automate
- Evaluating and selecting the most suitable technologies and vendors
- Developing a detailed implementation plan, including equipment installation, system integration, and employee training
- Ensuring seamless transition from the old to the new systems with minimal disruption to production
- Implementing robust cybersecurity measures to protect the new technology infrastructure
- Continuously monitoring and optimizing the performance of the automated systems
The Role of a Manufacturing Project Manager
Manufacturing project managers play a critical role in overseeing and executing projects.
Their key responsibilities are:
- Planning and scheduling: Developing detailed project plans and timelines (e.g., outlining the steps to launch a new product by specific dates)
- Resource allocation: Assigning resources such as workforce, machinery, and materials (e.g., scheduling a team of welders to work on a new assembly line)
- Budget management: Monitoring project costs and ensuring adherence to the budget (e.g., tracking material costs and labor hours to stay within budget constraints)
- Risk management: Identifying potential risks and implementing mitigation strategies (e.g., having a backup supplier in case of a parts shortage)
- Quality assurance: Ensuring that the project meets industry quality standards (e.g., conducting inspections to ensure manufactured parts meet specifications)
- Communication: Coordinating with various stakeholders, including suppliers, engineers, and production teams (e.g., providing regular updates on project progress to all involved parties)
To excel as a project manager in the manufacturing industry, you should possess technical knowledge and an aptitude for identifying and resolving issues promptly. You should also be proficient in project management software, methodologies, and tools.
Leadership skills, strong verbal and written communication skills, and a degree in engineering, manufacturing, or a related field will help you succeed in manufacturing project management.
Stages of Project Management for Manufacturing
The manufacturing project management process is typically divided into five phases: initiation, planning, execution, monitoring, and closure. Each phase plays a vital role in ensuring the project’s success.
Initiation
The initiation phase in manufacturing project management involves defining the project’s objectives, scope, and feasibility. Key activities include:
- Creating a proposal outlining the project’s goals, benefits, and requirements
- Analyzing the technical and financial feasibility of the project
- Identifying all stakeholders and understanding their needs and expectations
For instance, a company may want to manufacture a new line of athletic shoes. In this phase, the project managers would define the project goals (launching the shoes within six months, achieving a target cost per unit), analyze the feasibility (considering raw material availability, production capacity, and competitor analysis), and identify stakeholders (engineers, designers, suppliers, marketing team).
Planning
During the planning phase, detailed project plans and schedules are developed. This phase includes:
- Defining the project scope and deliverables
- Creating a detailed project timeline with milestones
- Identifying and allocating resources required for the project
- Developing strategies to mitigate potential risks
- Estimating costs and preparing a budget
In the shoe manufacturing project, this phase would define the scope (types of shoes, number of units). The project manager would create a detailed timeline with milestones like prototype completion and pilot production run.Â
Resources would be identified—machining equipment, raw materials (specific types of fabric and rubber), and personnel (skilled workers for different stages of the production process). Risk mitigation strategies would address potential delays due to material shortages or quality issues. Finally, a cost estimate would be made for materials, labor, and machinery usage.
Execution
The execution phase in the manufacturing project management process is where the project plan is put into action. Activities in this phase include:
- Assigning tasks to team members and ensuring resource availability
- Overseeing the manufacturing process to ensure it aligns with the project plan
- Implementing quality assurance processes to meet industry standards
- Maintaining regular communication with stakeholders and team members
To continue the shoe manufacturing example, the manufacturing phase begins with the plan in place. The project manager assigns tasks, designers finalize the shoe model, engineers develop production processes, and procurement specialists secure raw materials.Â
The project manager oversees the production line, ensuring shoes are manufactured according to specifications and the timeline. Quality assurance checks are implemented at every stage—inspecting raw materials, monitoring stitching on the shoe upper, and verifying sole adhesion.Â
They maintain regular communication with suppliers regarding material delivery and with the marketing team for any packaging or branding updates.
Monitoring
Monitoring involves tracking the project’s progress and performance. Key activities include:
- Measuring project performance against the plan using KPIs
- Continuously checking for quality adherence
- Monitoring and managing risks as they arise
- Providing regular updates to stakeholders on project status
The shoe manufacturing project team monitors the progress against the plan. Key Performance Indicators (KPIs) could include units produced per day, defect rates during quality checks, and adherence to the project budget.Â
Random shoe samples are checked for quality throughout production. Identified risks, like a machine breakdown, are addressed promptly to minimize delays. Stakeholders receive regular updates on production numbers, quality control results, and budget adjustments.
Closure
The closure phase marks the completion of the project. Activities include:
- Conducting a thorough review of the project outcomes
- Documenting all project-related information and lessons learned
- Collecting feedback from stakeholders and team members
- Handing over the final product and closing out the project
Once the new athletic shoe line is manufactured, the project enters the closure phase. A final review is conducted to assess whether the project met its goals (e.g., launched on time, achieved target production costs, etc.).Â
All project documentation, including production blueprints, quality reports, and lessons learned (e.g., improvements for future production runs) are compiled.Â
The manufacturing project manager gathers feedback from stakeholders on the project’s execution and areas for improvement. Finally, the completed shoe inventory is handed over to the warehouse, and the project is officially closed.
Following these stages ensures that manufacturing projects are completed efficiently, on time, and within budget. It also helps in:
- Enhancing quality: Systematic monitoring and quality control processes ensure high-quality outputs
- Reducing risks: Proactive risk management minimizes potential project disruptions in project management and process
- Improving communication: Regular updates and stakeholder engagement foster better communication and collaboration throughout the project management and development phases
- Streamlining processes: Well-defined plans and schedules facilitate operations and improve efficiency
Project Management Tools for Manufacturing
Project management software and tools are essential in manufacturing for complex project management, coordinating teams, and tracking progress.
A versatile project management software like ClickUp, when tailored to the manufacturing processes, helps:
- Assign tasks to team members easily and track progress in real-time
- Set deadlines for each task in the production process
- Create standardized checklists for quality inspections at various production stages so you can track defects and prevent faulty products from reaching customers
- Reorder raw materials based on inventory levels and production requirements. Schedule stocktaking tasks to maintain accurate stock levels
- Plan preventive maintenance and equipment calibration tasks to prevent breakdowns and minimize downtime
- Assign safety training tasks and incident reporting to ensure compliance with industry regulations
ClickUp can be a versatile manufacturing software for small businesses and large enterprises alike.
Here’s what John Watson, Director of Non-Clinical Development, Auregen BioTherapeutics, said about using ClickUp for their manufacturing project management lifecycle:
Let’s take a closer look at the features that will help you drive manufacturing project success using ClickUp:
1. ClickUp Brain
ClickUp Brain for AI-powered document management: ClickUp’s built-in AI features can quickly review large volumes of procurement documents, identify discrepancies, and suggest corrections, saving time and reducing errors.
It can also enable you to:
- Summarize strategy documents and generate actionable insights. It identifies key points, allowing teams to focus on critical tasks
- Assist in drafting standard operating procedures (SOPs) by predicting text and summarizing key points, ensuring consistency and comprehensiveness
- Translate instructions across languages. This aids communication between global manufacturing teams
- Connects projects, documents, and knowledge with its AI neural network. It enhances collaboration and knowledge sharing within your manufacturing team
2. ClickUp Project Management Solutions for Teams
Leverage ClickUp’s Project Management Solutions for Teams for efficient collaboration across departments and stakeholders. Manage project roadmaps and development priorities and track progress in one place, granting complete project visibility to relevant teams.
Here’s how it can benefit your manufacturing business:
- Provides real-time updates and easy collaboration among team members. This streamlines production processes improves efficiency, and ensures smoother operations
- Allows you to assign tasks to team members, track progress in real-time, and boost productivity
- If your manufacturing team follows agile methodologies, it offers expert-crafted AI tools for product roadmaps, test plans, and technical specifications
- Allows you to build customized workflows tailored to your manufacturing processes. You can track, manage, and collaborate on projects effectively
3. ClickUp Tasks and ClickUp Automations
Automate task assignments for procurement officers, setting reminders for order placements, follow-ups, and delivery schedules using ClickUp Tasks.
Automate alerts for inventory levels, ensuring timely reorders and preventing stockouts or overstock situations using ClickUp Automations. Create automated workflows for each stage of the production process, ensuring tasks are completed sequentially, and dependencies are managed effectively.
Coordinate workflows on autopilot, preventing delays and minimizing project duration and expenses. Whether it’s reassigning tasks or seeking stakeholder approvals, ClickUp Automations has got you covered.
4. Integrate with ERP systems
Enterprise Resource Planning (ERP) is software that helps organizations automate and manage core business processes for optimal performance.
You can migrate data from your existing tools and ERP solutions to ClickUp easily and without data loss.
Here are some of the benefits of integrating with ERP systems:
- ERP systems integrate various business processes, such as finance, inventory management, human resources, and production planning. By doing so, they eliminate redundancies and improve the flow of information within the organization. For example, consider an HR department that uses separate systems for payroll, employee records, and recruitment. An ERP system would consolidate these functions, allowing HR professionals to access all relevant data from a single platform. This streamlines processes, reduces manual effort, and ensures consistency
- Automation is a key feature of ERP systems. Routine tasks like data entry, approvals, and reporting are automated, reducing the need for manual labor. Employees can focus on more strategic activities, such as analyzing data, making informed decisions, and collaborating with colleagues. This shift from repetitive tasks to value-added work enhances overall efficiency
- ERP systems centralize data management. Instead of maintaining separate spreadsheets or databases, all relevant information resides in one place. This reduces the risk of discrepancies due to data duplication or outdated records. Accurate, real-time insights are available for decision-making, whether it’s tracking inventory levels, monitoring project progress, or assessing financial performance
- As businesses grow, their operational needs evolve. ERP systems are designed to scale alongside the organization. Whether you’re adding new processes, expanding to new locations, or accommodating additional users, ERP solutions can adapt without requiring significant system overhauls. This scalability ensures long-term viability
In addition to manufacturing ERP software, you can link ClickUp with CRM systems to ensure customer orders and feedback are seamlessly incorporated into the production planning process.
5. ClickUp Dashboards
Set clear project management goals and track them on dashboards. Set monthly or quarterly production targets and use dashboards to monitor real-time progress.
ClickUp’s Dashboards allow you to:
- Track key quality metrics to ensure products meet manufacturing industry standards and customer expectations
- Use these insights to monitor supply chain KPIs, such as lead times and supplier performance, to identify areas for improvement in project management and progress
- Automate project reports, freeing up time for essential tasks
- Create communication hubs, keeping stakeholders informed and aligned
You can make a project management dashboard to visualize your manufacturing projects. Here’s how:
- Define KPIs: Start by identifying the key performance indicators (KPIs) relevant to your manufacturing project
- Select a template: ClickUp offers dashboard templates for various purposes, such as task tracking, team collaboration, time-tracking metrics, and more
- Customize cards: Add cards to your dashboard representing different aspects of your project (e.g., tasks, milestones, resource allocation)
- Visualize data: Use charts, graphs, and widgets to display project-related information
- Collaborate: Share the dashboard with your team and stakeholders for real-time insights
6. ClickUp Kanban Boards and ClickUp Gantt charts
Visualize workflows with ClickUp Kanban Boards and ClickUp Gantt charts. Use Kanban boards to track production stages, from raw material procurement to finished goods.
In ClickUp’s Kanban Board view, you can:
- Easily track progress by visualizing tasks with customizable statuses (e.g., Closed, Open, Review, In Progress, Blocked)
- Add product and SKU-specific information in Custom Fields (e.g., Order Number, Production Line, Priority) to tasks
- Assign tasks, set due dates, and communicate within ClickUp
You can customize the visualizations to manage quality standardization issues and corrective actions, addressing them promptly during the project management cycle.
Similarly, Gantt Charts provide a timeline view of project schedules, which is essential for managing complex manufacturing projects. You can:
- Plan and track the progress of long-term projects, ensuring milestones are met on time
- Allocate resources efficiently, avoiding overbooking and underutilization
- Get a clear overview of resource availability (personnel, machinery, raw materials)
- Schedule and track quality control activities throughout the process
- Plan and schedule maintenance tasks to prevent disruptions. Optimize equipment performance and prevent breakdowns
- Visualize material flow and identify potential delays. Take proactive measures to mitigate supply chain bottlenecks
7. ClickUp Project Management Template
Drive complex, cross-functional projects with the ClickUp Project Management Template. Customize this prebuilt template to streamline various aspects of manufacturing project management, from procurement and inventory management to production scheduling and quality control.
Here’s how you can use this project management template:
- Create lists for different stages of procurement, such as ‘Order Placement,’ ‘In Transit,’ and ‘Received.’ Use tasks to track individual orders, assign them to procurement officers, and set due dates
- Maintain a list of active vendors, including key details like contact information, delivery performance, and contract terms
- Add custom fields for machine usage, material costs, and quality checks
- Set project management milestones for critical stages such as prototype completion, initial production run, and final quality checks using custom statuses
Efficient resource allocation is crucial in manufacturing. ClickUp allows you to assign tasks to specific machines, workstations, or employees based on availability and skillset, optimizing resource utilization and preventing delay. By providing a central platform for discussions, file sharing, and real-time updates, it helps you keep everyone informed and eliminates communication silos.
Effective Project Management for Manufacturing Success
Understanding the roles, stages, and tools involved in manufacturing project management can help you streamline operations and achieve organizational goals. It’s also important to choose the right project management software that ensures risk management efficiency across key project milestones.
Your chosen project management software should also be able to analyze data, track materials, and identify potential bottlenecks.
ClickUp offers a powerful solution in this regard, with its comprehensive features and functionalities, which are essential in manufacturing project management software.
From task tracking and resource allocation to inventory management and risk mitigation, ClickUp equips your project team with tools to overcome challenges and drive success in the manufacturing process.
Try ClickUp today!