Si te gusta mejorar los procesos, probablemente hayas oído hablar de las herramientas Lean Six Sigma.
La metodología Lean Six Sigma puede ser un potente facilitador para mejorar los procesos de su empresa. Pero hay un inconveniente. Si es nuevo en esta metodología, puede resultarle bastante abrumadora. Los detalles pueden confundirle o puede sentirse estresado por los datos que necesita analizar.
No se preocupe. En este artículo, desglosaremos Lean Six Sigma y diez herramientas, así como los procesos empresariales para los que son adecuadas, con el fin de disparar la eficiencia de los procesos. ⚒️
Cuando se implementan correctamente, estas herramientas reducen eficazmente la variabilidad de los procesos y crean una cultura de mejora continua.
¿Qué son las herramientas Six Sigma?
Las herramientas Six Sigma son metodologías analíticas y de mejora de procesos que reducen la variabilidad de los procesos y garantizan unos niveles de calidad más altos en los resultados.
Desarrollado en la década de 1980 por el ingeniero de Motorola Bill Smith, el enfoque Six Sigma se utilizó inicialmente para mejorar el rendimiento de los procesos de fabricación. Con el tiempo, sectores como la educación, la sanidad y los servicios han adoptado este enfoque.
El objetivo principal de Six Sigma es identificar defectos y detectar las causas subyacentes de las variaciones en los procesos. Las herramientas asociadas implementan mejoras de calidad consistentes al identificar los problemas de los procesos.
Aprovechar estos métodos permite a las organizaciones ofrecer precisión, mejorar la fiabilidad y reducir la duración de los ciclos de los procesos.
10 herramientas y técnicas Six Sigma para mejorar los procesos empresariales
Aquí tienes 10 herramientas Lean Six Sigma de renombre para mejorar los procesos de garantía de calidad y la eficiencia operativa de tu organización:
1. Planificar, hacer, verificar, actuar (PDCA)
Este modelo iterativo de cuatro fases ayuda a las organizaciones a promover el control de calidad continuo y el aprendizaje constante. El ciclo PDCA es ahora un elemento fundamental de la metodología Six Sigma, que mejora la fabricación ajustada y el control de calidad en todos los sectores.
- Planificación: La fase de planificación identifica un problema u oportunidad de mejora dentro de un proceso. En esta fase se recopilan datos para evaluar el rendimiento actual y definir el alcance de la optimización del proceso del proyecto
- Pendiente: Esta fase implementa las estrategias a pequeña escala y evalúa los resultados de la fase anterior en comparación con los resultados esperados. Se trata de un experimento controlado con documentación precisa
- Comprobación: En este punto, su equipo verificará si los cambios implementados han dado lugar a una mejora cuantificable
- Actuación: Esta fase ejecuta los cambios a mayor escala e incorpora los comentarios de las fases anteriores. Las pruebas correctas estandarizan su nuevo proceso
Cuándo utilizar esta herramienta: El PDCA se puede aplicar a los procesos de desarrollo de software. Al abordar los comentarios de forma eficaz, puede garantizar que cada iteración cumpla o supere las expectativas de los clientes.
La función Pizarra de ClickUp ofrece un lienzo totalmente personalizable para generar ideas, elaborar estrategias y correlacionar procesos empresariales. También puede utilizarla para manipular flujos de trabajo ágiles y categorizar subtareas y causas fundamentales de ineficiencias en los procesos.
La plantilla de pizarra del proceso PDCA de ClickUp te permite hacer una lluvia de ideas sobre posibles soluciones y realizar un seguimiento de las iteraciones y los resultados del plan. Esta plantilla estructurada te permite organizar tu proceso en tareas específicas y utilizar diferentes estados para mantener a tu equipo informado sobre el progreso.
2. Mapeo de la cadena de valor (VSM)
Una cadena de valor es el pedido de tareas internas y externas que se utilizan normalmente para entregar productos o servicios a los clientes. El proceso de mapeo de la cadena de valor (VSM) ayuda a visualizar y analizar el flujo de materiales e información a medida que un producto se mueve a lo largo de la cadena de valor.
Su meta principal es identificar el desperdicio y las ineficiencias a través de la visualización de procesos de principio a fin.
- Empiece por correlacionar el estado actual: Este paso crea una línea de base para medir las mejoras y ofrece información sobre los flujos de trabajo o los cuellos de botella de los sistemas existentes
- Identificar problemas potenciales: Esto podría ser un desperdicio de recursos, como la sobreproducción, el tiempo de espera, el procesamiento excesivo, los defectos y el talento infrautilizado
- Diseñar un flujo de trabajo futuro: El tercer paso consiste en imaginar un flujo de trabajo con el mínimo desperdicio. Este paso incluye todo, desde el rediseño de los procesos hasta la organización de las células de trabajo
- Implemente los cambios: En esta fase, puede esperar inversiones en nueva tecnología o en la formación de nuevo personal para la fase de implementación
Cuándo utilizar esta herramienta: El VSM funciona bien en la fabricación y la logística a la hora de correlacionar el proceso de producción. Puede identificar retrasos y actividades que no aportan valor añadido, desde las materias primas hasta la entrega al cliente.
La plantilla Value Steam Mapping de ClickUp permite a tu equipo supervisar y perfeccionar continuamente los procesos tras actualizar los mapas del estado actual. Este proceso iterativo te ayuda a generar ideas para mejorar tus procesos existentes, mantener tus mejoras y seguir siendo ágil a la hora de responder a las condiciones dinámicas del mercado.
3. Diagrama de causa y efecto
Comúnmente llamada «diagrama de espina de pescado» o «diagrama de Ishikawa», esta plantilla puede ayudar a detectar las causas fundamentales de las ineficiencias de los procesos correlacionando las relaciones entre diferentes factores.
Empiece por definir el problema en la cabeza del espino y enciérrelo en un círculo para centrarse en él. A continuación, dibuje una línea recta (columna vertebral) desde la declaración del problema hasta el lado izquierdo de la pizarra. Esta línea representa la relación entre las causas y los efectos.
Más adelante, puede clasificar las causas del problema. Estas espinas del hueso de pescado suelen incluir problemas relacionados con la mano de obra, los materiales, los métodos, las máquinas o las mediciones.
Considera la posibilidad de añadir ramas específicas para cada categoría principal. Además de enumerar causas concretas, puedes animar a tus compañeros de equipo a compartir ideas en estas ramas. No dudes en añadir subramas para causas muy específicas. Utiliza software gratuito de gestión de proyectos como ClickUp para crear diagramas que desglosen tus métodos de mejora de procesos.
Cuándo utilizar esta herramienta: Esta herramienta es eficaz en entornos sanitarios para analizar eventos adversos o en el servicio de atención al cliente para resolver problemas recurrentes que afectan a la satisfacción de los clientes.
La plantilla de pizarra de causa y efecto de ClickUp te permite listar y revisar las relaciones entre tus problemas y sus posibles causas. Puedes utilizar marcadores digitales para resaltar los problemas clave y participar en debates para investigarlos más a fondo. Una vez completado el diagnóstico, puedes determinar medidas de acción personalizadas para abordar cada causa raíz creando un flujo de trabajo de ClickUp de tu elección.
4. Las cinco preguntas
Esta herramienta Six Sigma explora las causas fundamentales de un problema de proceso preguntando «por qué» cinco veces o tantas veces como sea necesario.
Preguntarse continuamente «por qué» a cada respuesta relacionada con el diagnóstico del problema le acerca a la causa raíz.
Su meta aquí es eliminar las capas de síntomas y suposiciones para descubrir la causa fundamental del problema. Una vez identificado el problema, es más fácil desarrollar contramedidas personalizadas.
Por ejemplo, supongamos que tiene un problema para retener a los empleados. Utilizando el método de las cinco preguntas, identifique la causa raíz del problema.
Problema: Baja tasa de retención de empleados.
- Por qué: Los horarios de trabajo no eran flexibles
- Por qué: El alcance de los proyectos no está claro
- Por qué: Las fichas de producto no se compartieron a tiempo
- Por qué: Baja productividad por parte del cliente
- Por qué: Falta de recursos para recopilar y compartir información completa sobre los productos
A partir de estas causas, queda claro que los problemas se derivan de la incapacidad del cliente para compartir informes completos sobre los productos a tiempo. Abordar esto en una fase anterior del flujo de trabajo podría ayudar a sus empleados a trabajar según el plan y mejorar su satisfacción laboral.
Esta herramienta Lean Six Sigma ofrece simplicidad, eficiencia y eficacia a la hora de separar los síntomas de la causa raíz del problema.
Cuándo utilizar esta herramienta: Los cinco porqués se utilizan mejor en situaciones que requieren un análisis de las causas fundamentales, especialmente cuando los problemas son complejos y tienen múltiples capas. Considere la posibilidad de utilizar esta herramienta Six Sigma en entornos operativos para comprender las razones de los fallos de las máquinas o las interrupciones de los procesos.
La plantilla «5 porqués» de ClickUp permite una colaboración más rápida entre los equipos y ofrece una metodología repetible para resolver ineficiencias. Una vez identificadas las causas fundamentales de las variaciones en los procesos, pasa directamente a la resolución de problemas creando y asignando tareas específicas a los miembros de tu equipo.
5. FMEA
El análisis de modos y efectos de fallos (FMEA) es ideal para enumerar todos los fallos posibles en un diseño, un proceso de fabricación o montaje, un producto o un servicio.
Está diseñada para detectar posibles puntos de fallo y permitir a las empresas tomar medidas correctivas mediante la detección temprana. Puede utilizar FMEA para priorizar los problemas en función de su impacto y probabilidad de ocurrencia.
Empiece por reunir un equipo multifuncional con conocimientos sobre el proceso que se va a analizar. Esto introduce varias perspectivas sobre posibles fallos.
Una vez definido el producto, proceso, diseño o servicio que se va a analizar, haga una lista de cada paso o componente y correlacione las formas en que podría producirse un fallo. Estos son sus modos de fallo.
Cada modo de fallo se puntúa para reflejar su gravedad (S), repetición (O) y detectabilidad (D). El número de prioridad de riesgo (RPN) se calcula mediante:
RPN = S x O x D
Utilice este RPN para priorizar los modos de fallo en función de lo que más afecta a la funcionalidad del producto.
Cuándo utilizar esta herramienta: Es adecuada para la evaluación de riesgos de procesos nuevos o existentes, especialmente antes del lanzamiento de productos o procesos. Se utiliza ampliamente durante el diseño y el desarrollo en las industrias automotriz y aeroespacial para prevenir fallos futuros y mejorar la fiabilidad.
La plantilla FMEA Lean Six Sigma de ClickUp aclara qué subprocesos o componentes necesitan mejoras para evitar ineficiencias inesperadas. Sus diversas vistas te ayudan a organizar los riesgos por gravedad y frecuencia.
6. Kanban
Los tableros Kanban son potentes herramientas visuales de gestión ajustada para optimizar los procesos empresariales. Permiten a los usuarios visualizar las tareas, limitar el trabajo en curso y maximizar el flujo para reparar las ineficiencias del proceso y la eficacia operativa.
En primer lugar, correlacione los procesos clave de la empresa y clasifique cada proceso en fases distintas. Los primeros incluyen factores como la entrega de productos o la incorporación de clientes, y los segundos pueden incluir «Solicitud recibida», «Control de calidad» o «Procesamiento», etc.
Configure su tablero Kanban con columnas para cada fase. Este diseño visual le mostrará el progreso de sus tareas, lo que le permitirá detectar los cuellos de botella de manera eficiente.
No olvide mencionar el número máximo de tareas (límites WIP) que se pueden gestionar simultáneamente. Esto es crucial para identificar bloqueos y abordarlos de forma proactiva.
En general, su gestión dinámica de tareas revela información en tiempo real sobre el flujo del proceso y destaca todos los retrasos. La arquitectura de esta herramienta Six Sigma ayuda a realizar ajustes en los procesos mediante la reasignación de recursos. También puede intentar redefinir los pasos del proceso para reducir las ineficiencias.
Cuándo utilizar esta herramienta: Kanban es ideal para equipos de desarrollo de software y contenido editorial para gestionar proyectos, regular el flujo de trabajo y limitar visualmente el trabajo en curso.
Por ejemplo, la función Tablero Kanban de ClickUp te permite visualizar claramente las fases del flujo de trabajo y realizar un seguimiento del progreso en tiempo real. La combinación de estas capacidades con el enfoque basado en datos de Six Sigma es perfecta para evitar errores en procesos a pequeña y gran escala.
La plantilla de tablero Kanban de ClickUp divide las tareas más grandes en subtareas más alcanzables y ofrece información sobre la capacidad de su equipo. Puede reducir significativamente la duración de los ciclos de las tareas y maximizar el retorno de la inversión de sus recursos.
7. Gráfico de Pareto
Los gráficos de Pareto son un tipo de gráfico de barras que representan la frecuencia o el impacto de los problemas o causas en un proceso. El principio 80/20 de Pareto sugiere que el 80 % de todos los problemas se deben al 20 % de las causas.
El gráfico le ayuda a separar las «pocas causas vitales» de las «muchas causas triviales» de un problema. Esto le permite abordar los problemas de alto impacto desde el principio.
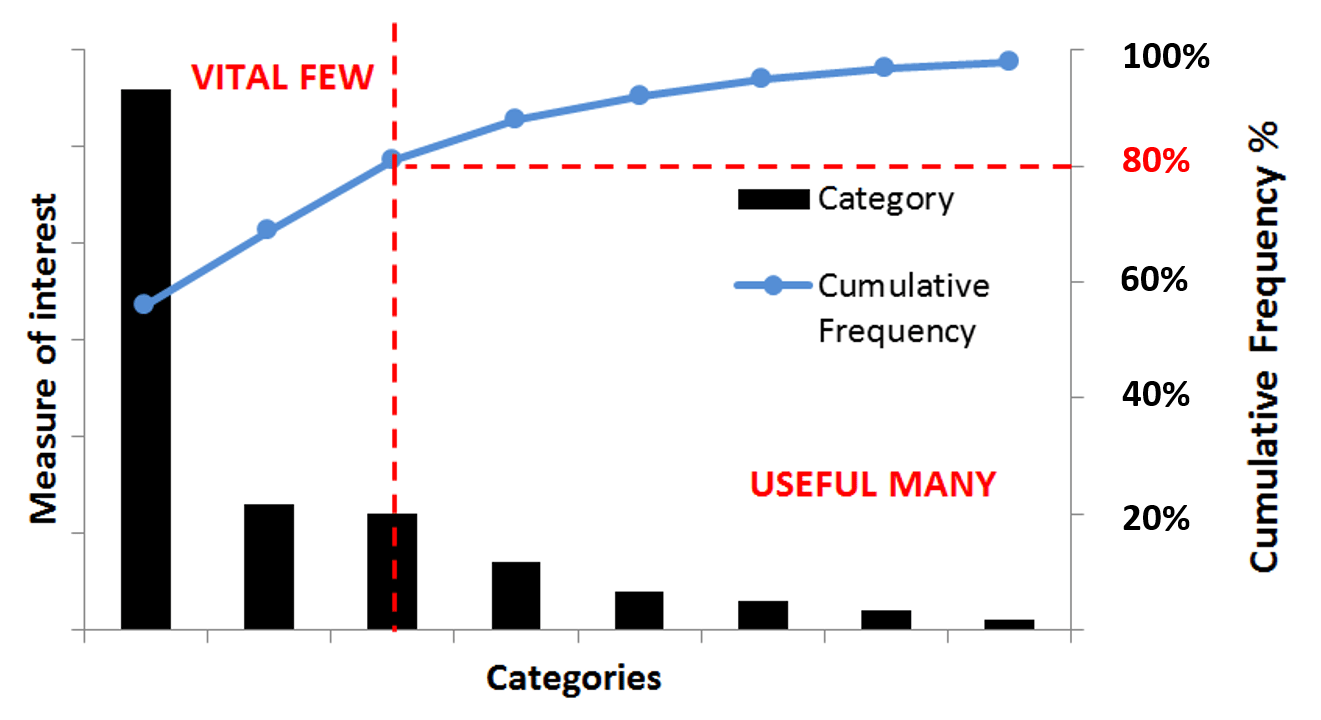
Los dos primeros pasos incluyen la recopilación y categorización de datos. Una vez categorizados los problemas, debe contabilizar la frecuencia de repetición de cada categoría. A continuación, clasifique las categorías en función de la frecuencia de repetición, de mayor a menor. Después, calcule el porcentaje acumulado del total de defectos o causas que se contabilizan en cada categoría.
Por último, trace las categorías en el eje horizontal del gráfico y la frecuencia en el eje vertical.
El gráfico de Pareto ayuda a alcanzar las metas de mejora de los procesos de su empresa al:
- Medir y comparar problemas
- Identificar áreas de interés
- Asignar recursos de forma eficaz
- Iteración para la mejora
Cuándo utilizar esta herramienta: Ayuda en el desarrollo de software al priorizar qué errores o funciones deben abordarse primero en función de su frecuencia y su impacto en los usuarios.
8. Tiempo takt
El tiempo de ciclo es un concepto fundamental que sincroniza los ritmos de producción con la demanda de los clientes, creando un flujo de operaciones fluido y continuo.
El tiempo Takt le ayuda a establecer el ritmo de producción para que se ajuste a la velocidad a la que se necesitan los productos. Con el tiempo Takt, puede esperar una alta eficiencia en la producción y menores costes de residuos e inventario.
Tiempo de ciclo = Tiempo total de producción disponible / Demanda del cliente
Por ejemplo, si una fábrica opera durante 960 minutos al día y la demanda de los clientes es de 320 unidades al día, el tiempo takt es:
Tiempo de ciclo = 960 minutos / 320 unidades = 3 minutos / unidad
En la mejora de los procesos empresariales, el tiempo de takt es adecuado para ajustar la velocidad de las operaciones equilibrando las cargas de trabajo o reconfigurando las líneas de producción. Puede supervisar las métricas de producción para comprobar si algún paso no cumple con el tiempo de takt.
Cuándo utilizar esta herramienta: Funciona mejor en el sector de la fabricación de productos electrónicos de consumo. Ayuda a alinear la velocidad de producción con la demanda del mercado para evitar la sobreproducción y reducir los costes de inventario.
9. Poka-Yoke
Poka-Yoke, un término japonés que significa «a prueba de errores», incorpora medidas de seguridad en los procesos para evitar y corregir los errores en su origen, antes de que se conviertan en defectos. Esta herramienta Six Sigma hace que sea prácticamente imposible que se produzcan errores.
Como la mayoría de las técnicas Six Sigma, se empieza por analizar el proceso y detectar los puntos de error comunes. Estos pueden deberse a errores humanos, como olvidos o suposiciones incorrectas.
Además, analiza los errores causados por el diseño del proceso, la interfaz o la interacción entre el empleado y el proceso.
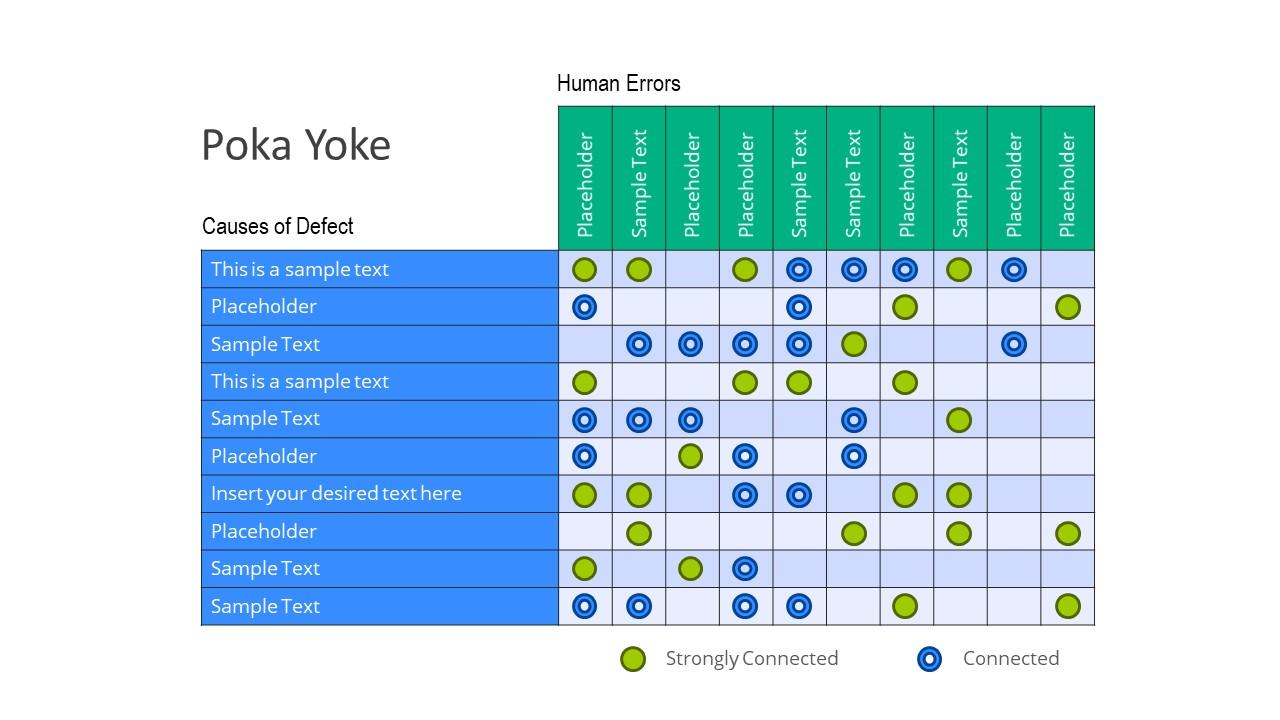
Lo más importante es desarrollar una solución Poka-Yoke que evite los errores o los haga evidentes de inmediato si se producen. Aquí hay tres tipos básicos de Poka-Yoke:
- Tipo de contacto: Identifica defectos en los productos mediante pruebas de atributos físicos
- Tipo de valor fijo: Garantiza que se realicen un número específico de movimientos o acciones
- Tipo de paso de movimiento (secuencia): Comprueba las secuencias de acción adecuadas y verifica si se completan en el orden correcto y sin omisiones
Puede probar plantillas adicionales de mejora de procesos para combinar dos de las técnicas anteriores y realizar pruebas A/B.
Cuándo utilizar esta herramienta: Ampliamente utilizado en la fabricación de automóviles, Poka-Yoke garantiza que las piezas se instalen correctamente, evitando errores de montaje y mejorando la calidad del producto.
10. SIPOC
Es el acrónimo de «proveedores, insumos, procesos, productos y clientes». SIPOC ayuda a su equipo a visualizar el contexto, el alcance y las partes interesadas clave involucradas. Utilice este tipo de Lean Six Sigma para garantizar que los análisis o cambios posteriores estén bien orientados y sean relevantes.
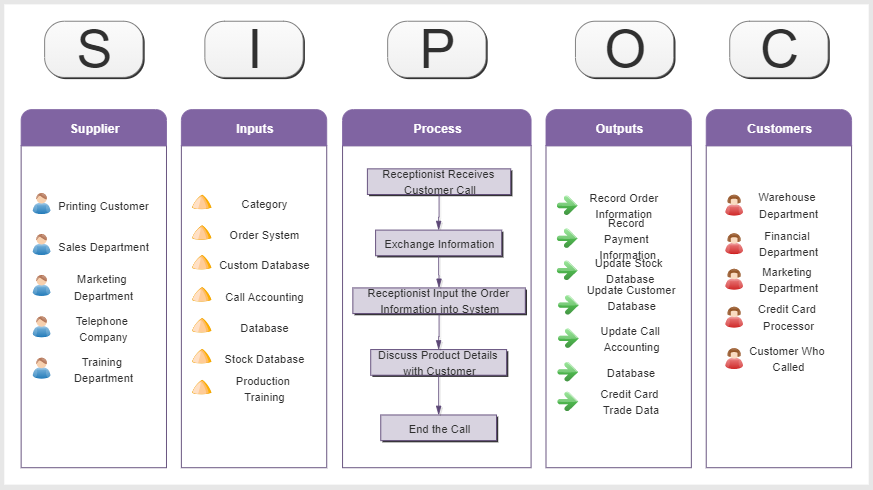
Describa el proceso que desea mejorar en cinco o siete pasos de alto nivel. A continuación, correlacione los cinco componentes de SIPOC.
- Los proveedores aportan información al proceso. Pueden ser equipos internos, proveedores externos o sistemas
- Los insumos son la lista de materiales, información u otros recursos que ayudan a ejecutar el proceso
- El proceso incluye los pasos críticos de la tarea, desde el inicio hasta el final. Recuerde que debe hacer una panorámica de alto nivel, no un mapa detallado del proceso
- Los resultados definen lo que produce el proceso. Son los resultados o productos que se obtienen del proceso
- Los clientes son aquellos que reciben sus productos. Tenga en cuenta que los clientes pueden ser internos o externos a la organización
Puede crear una tabla o un diagrama SIPOC sencillo que describa el flujo desde los proveedores hasta los clientes a lo largo del proceso. Pruebe a trabajar con diferentes plantillas de diagramas SIPOC para comprender mejor varios estilos de utilidad.
Cuándo utilizar esta herramienta: Esta herramienta es adecuada para sectores de servicios como la hostelería o la banca para correlacionar los procesos de atención al cliente. Ayuda a identificar qué elementos afectan a la experiencia de los clientes.
La plantilla SIPOC de ClickUp te permite establecer procesos sistemáticos para tu cadena de suministro sin perder tiempo ni recursos en tareas redundantes. Informa a tu equipo del alcance de un proceso a través de vistas separadas, como proveedor, proceso, entrada y salida, para ayudar a localizar las ineficiencias más rápidamente.
Su camino hacia la excelencia operativa
Estas herramientas Six Sigma marcan una mejora estratégica en el enfoque de su empresa o equipo hacia la mejora de procesos. Además de optimizar los procesos individuales, permiten a los equipos adoptar una cultura gratificante de mejora continua.
La integración de estas herramientas en las operaciones diarias prepara a su organización para obtener ganancias sostenidas en productividad y calidad. Si se pregunta por dónde empezar, pruebe a integrar las plantillas Six Sigma en ClickUp para que los procesos de su empresa sean más fiables y menos propensos a errores.
Regístrese hoy mismo en ClickUp y promueva una cultura de mejora continua.
Preguntas frecuentes
1. ¿Qué son las herramientas Six Sigma?
Las herramientas Six Sigma mejoran los procesos empresariales minimizando los errores. Algunas de ellas son el diagrama de espina de pescado (para identificar las causas raíz), el diagrama de Pareto y el FMEA (para fijar como objetivo las áreas de mejora críticas), las 5 preguntas (para profundizar en el origen del problema), los gráficos de control (para supervisar la variabilidad) y el PDCA (para la planificación iterativa).
2. ¿Es Six Sigma una herramienta Lean?
Las herramientas Six Sigma suelen asociarse con Lean, ya que ambas tienen como objetivo mejorar la eficiencia empresarial. Lean se centra en eliminar el desperdicio y mejorar el flujo de los procesos de producción para aumentar la eficiencia. Por otro lado, Six Sigma reduce la variación y los defectos para mejorar la calidad.
3. ¿Es Six Sigma una herramienta de calidad?
Sí, Six Sigma es fundamentalmente una herramienta de mejora de la calidad diseñada para reducir la variación de los procesos y mejorar la calidad de los resultados. Puede utilizar herramientas estadísticas para alcanzar y mantener un nivel de defectos en los procesos de no más de 3,4 defectos por cada millón de oportunidades.