Use this Gap Analysis Template to identify organizational gaps, assess performance, and set measurable goals, enhancing business strategy by understanding strengths, weaknesses, and improvement opportunities.
Explore more
Related templates
See more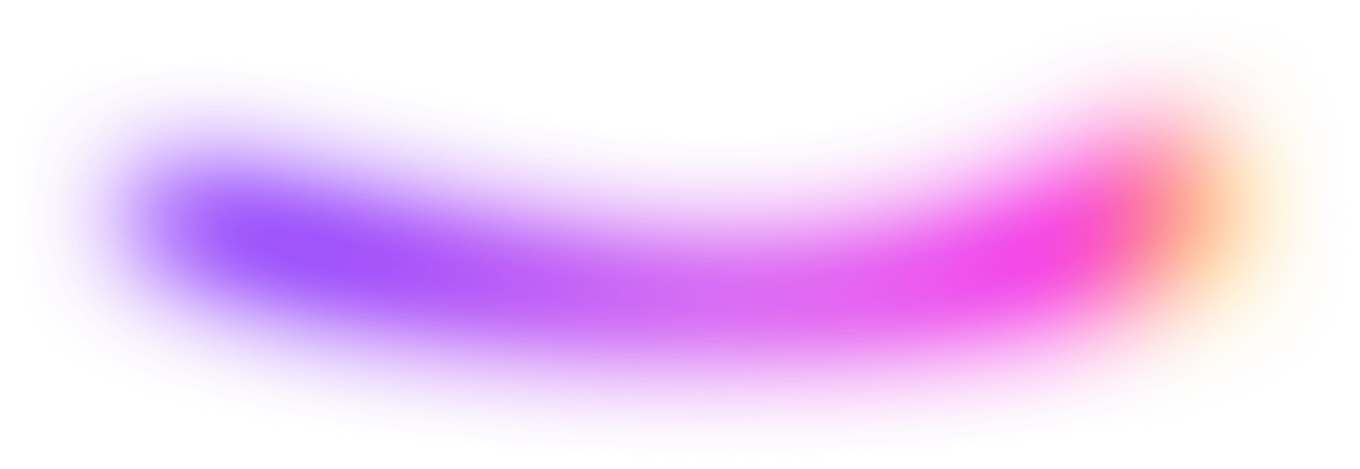
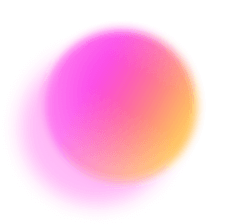
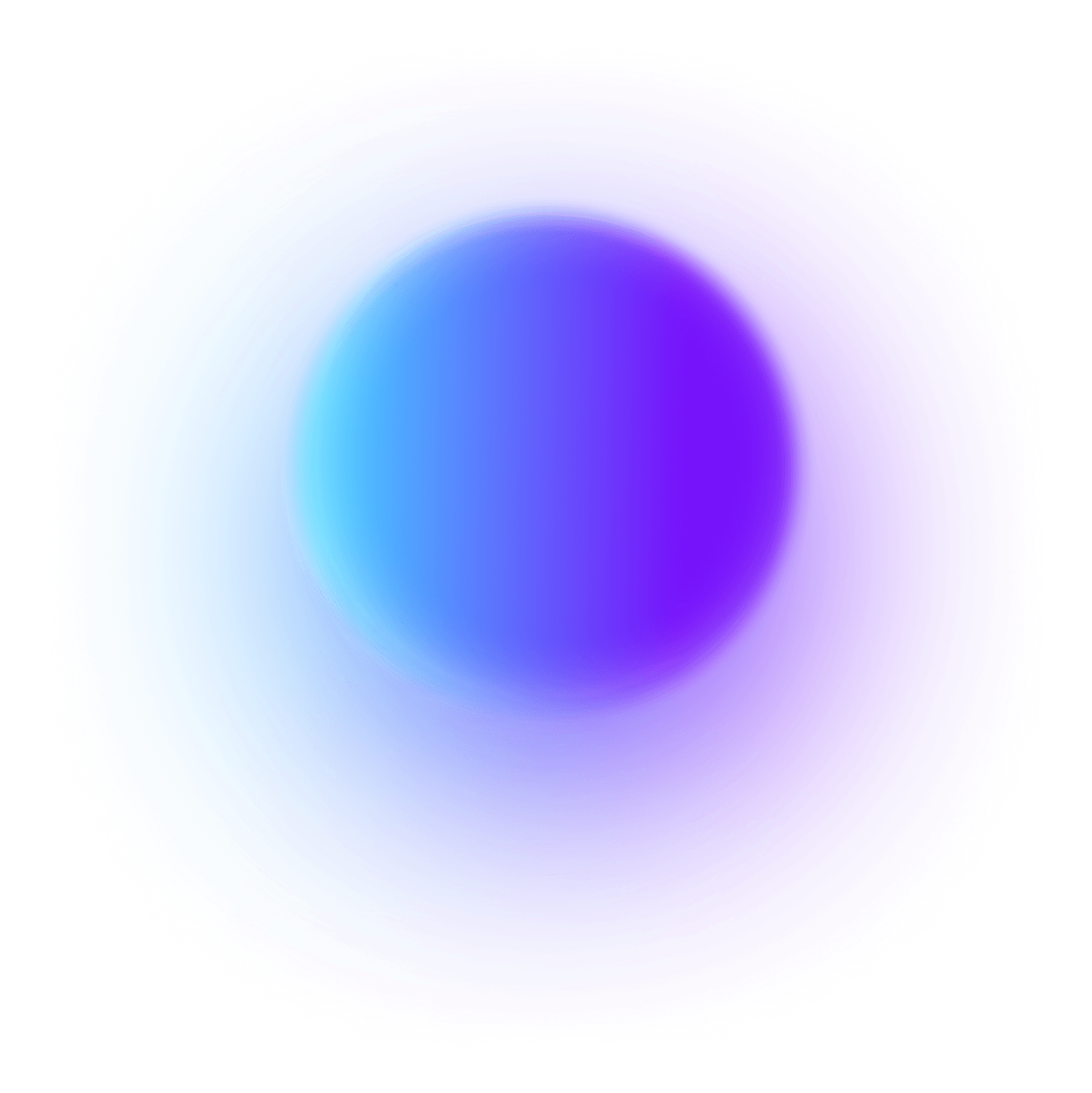
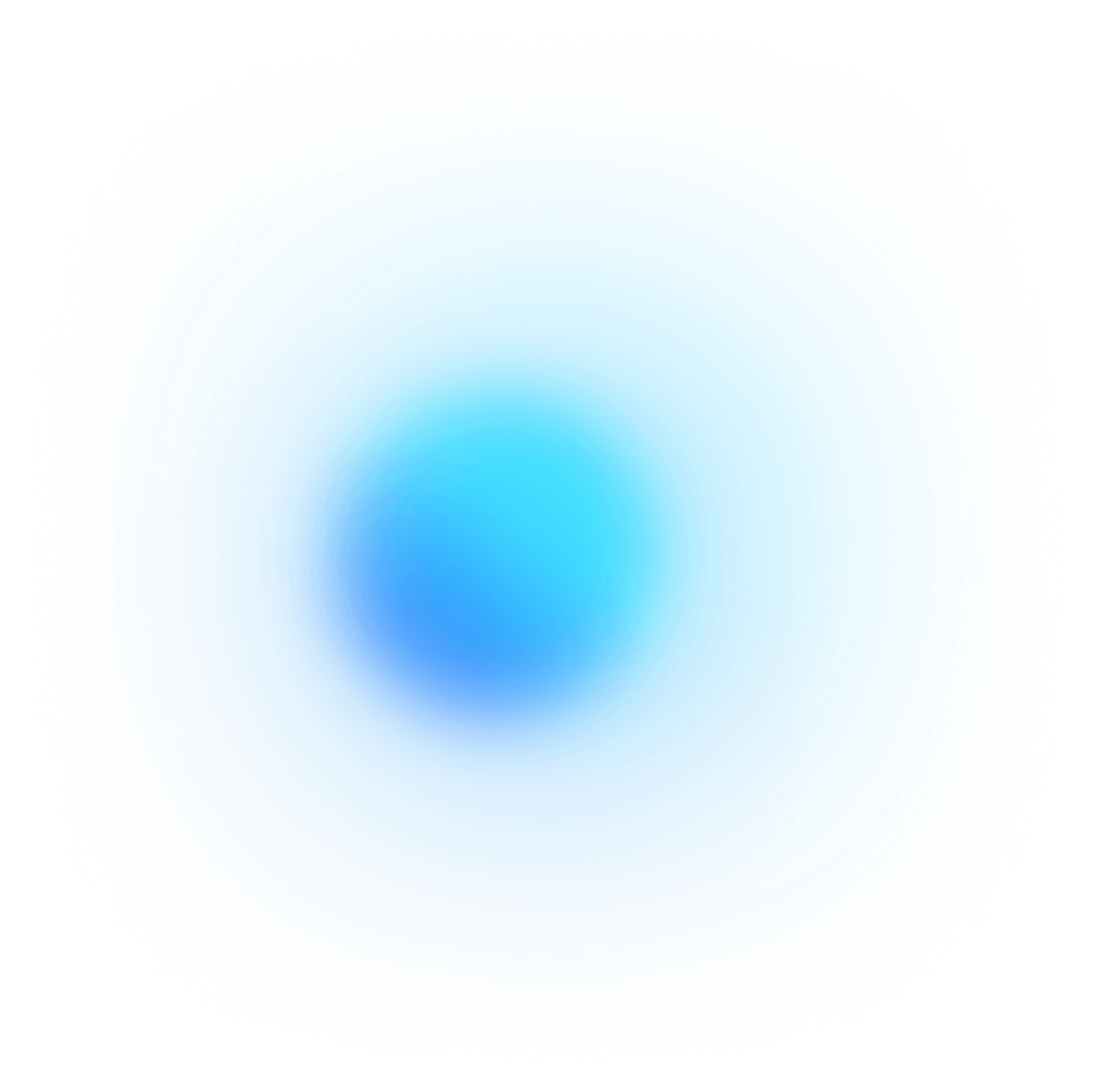
Supercharge your productivity
Organize tasks, collaborate on docs, track goals, and streamline team communication—all in one place, enhanced by AI.