プロセス改善に興味がある方なら、おそらくリーンシックスシグマのツールをご存知でしょう。
リーンシックスシグマ手法は、ビジネスプロセスの改善に強力な推進力となります。しかし、問題もあります。この手法を初めて使う場合、その内容に圧倒されてしまうかもしれません。詳細がわかりにくかったり、分析すべきデータにストレスを感じたりするかもしれません。
ご心配は無用です。この投稿では、リーンシックスシグマと 10 種類のツール、およびプロセス効率を飛躍的に高めるのに適したビジネスプロセスについて詳しくご説明します。⚒️
適切に導入されれば、これらのツールはプロセス変動を効果的に削減し、継続的改善の文化を築くことができます。
シックスシグマツールとは何ですか?
シックスシグマツールは、プロセス変動を削減し、出力の品質レベルを向上させるための分析的かつプロセス改善手法です。
1980年代にモトローラのエンジニアであるビル・スミスによって開発されたシックスシグマのアプローチは、当初、製造プロセスのスループット向上を目的として採用されました。その後、教育、医療、サービス業界など、多様な分野でこのアプローチが採用されるようになりました。
シックスシグマの主な目的は、欠陥を特定し、プロセスの変動の根本原因を突き止めることです。関連するツールは、プロセスの問題を正確に特定することで、一貫した品質の向上を実現します。
これらの手法を活用することで、組織は正確な成果を提供し、信頼性を向上させ、プロセスのサイクルタイムを短縮することができます。
ビジネスプロセスを改善する 10 のシックスシグマツールとテクニック
組織の品質保証プロセスと業務効率を向上させるための、信頼できるリーンシックスシグマツール10選:
1. 計画-実行-評価-改善 (PDCA)
この 4 段階の反復モデルは、組織が継続的な品質管理と継続的な学習を推進するのに役立ちます。PDCA サイクルは、現在ではシックスシグマ手法の基本要素となり、さまざまな業界でリーン生産方式と品質管理の改善に貢献しています。
- プランニング:プランニングフェーズでは、プロセス内の問題や改善の機会を特定します。このフェーズでは、現在のパフォーマンスを評価し、プロジェクトのプロセス最適化の範囲を定義するためのデータを収集します。
- 実行: このフェーズでは、戦略を小規模で実施し、前フェーズの結果を期待結果と照らし合わせて評価します。これは、正確な文書化を行う、管理された実験です。
- 確認: この時点で、チームは、実施した変更によって測定可能な改善があったかどうかを検証します。
- 実行:この段階では、変更を大規模に実行し、前の段階からのフィードバックを取り入れます。試用版が成功すると、新しいプロセスが標準化されます。
このツールを使用する場合:PDCA は ソフトウェア開発プロセスに適用できます。フィードバックに効果的に対応することで、各反復が顧客の期待を満たす、あるいはそれを上回ることを確実にすることができます。
ClickUp のホワイトボード機能は、ブレインストーミング、戦略立案、ビジネスプロセスのマッピングのために、完全にカスタマイズ可能なキャンバスを提供します。また、アジャイルワークフローの操作、サブタスクの分類、プロセスの非効率性の根本原因の特定にも使用できます。
ClickUp の PDCA プロセスホワイトボードテンプレートを使用すると、予想される解決策をブレインストーミングし、プランの反復と結果を追跡することができます。この構造化されたテンプレートを使用すると、プロセスを特定のタスクに整理し、さまざまなステータスを使用して、チームに進捗状況を常に知らせることができます。
2. バリューストリームマッピング (VSM)
バリューストリームとは、クライアントに製品やサービスを提供するために通常使用される、社内外のタスクの順序のことです。バリューストリームマッピング(VSM)プロセスは、製品がバリューストリームを流れる際に、材料や情報のフローを視覚化して分析するのに役立ちます。
その主な目標は、エンドツーエンドのプロセスを可視化することで、無駄や非効率性を特定することです。
- 現在の状況をマッピングすることから始めましょう: このステップでは、改善の測定基準となるベースラインを作成し、既存のシステムのワークフローやボトルネックに関する洞察を得ることができます。
- 潜在的な問題の特定: これは、過剰生産、待ち時間、過剰加工、欠陥、人材の未活用など、無駄なリソースの浪費が該当します。
- 将来のワークフローの設計: 3 番目のステップでは、無駄を最小限に抑えたワークフローを構想します。このステップには、プロセスの再設計から作業セルの編成まで、すべてが含まれます。
- 変更の実施: このフェーズでは、実装段階において、新しいテクノロジーへの投資や人材のトレーニングが必要になると予想されます。
このツールを使用する場合:VSM は、製造および物流において、生産プロセスをマップする場合に有効です。原材料から顧客への納品まで、遅延や付加価値のない活動を正確に特定することができます。
ClickUp のバリューストリームマッピングテンプレートを使用すると、現在の状況マップをアップグレードした後、チームがプロセスを継続的に監視および改善することができます。この反復プロセスにより、既存のプロセスを改善し、その改善を維持し、ダイナミックな市場の状況に対応しながら俊敏性を維持するための方法をブレインストーミングすることができます。
3. 因果関係図
一般に「フィッシュボーン」または「石川図」と呼ばれるこのテンプレートは、さまざまな要因間のリレーションシップをマップすることで、プロセスの非効率性の根本原因を特定するのに役立ちます。
まず、フィッシュボーンの上部に問題点を定義し、それを丸で囲んで注目します。次に、問題点の記述からホワイトボードの左側に直線(バックボーン)を描きます。この線は、原因と結果の関連性を表しています。
さらに、問題の原因を分類することができます。この魚骨の肋骨には、多くの場合、従業員、材料、方法、機械、測定に関する問題が含まれます。
各主要カテゴリに特定のブランチを追加することを検討してください。特定の要因をリストアップするだけでなく、チームメンバーにこれらのブランチでアイデアを共有するよう促すこともできます。非常に具体的な要因については、サブブランチを自由に追加してください。ClickUp などの無料のプロジェクト管理ソフトウェアを使用して、プロセス改善手法を分解した図を作成してください。
このツールを使用する場合:このツールは、医療現場での有害事象の分析や、顧客満足度に影響を与える繰り返しの問題を解決するカスタマーサービスで効果的です。
ClickUp の因果関係ホワイトボードテンプレートを使用すると、問題とその潜在的な原因の関係をリストアップして確認することができます。デジタルマーカーを使用して重要な問題を強調表示し、議論してさらに調査することができます。診断が完了したら、お好みの ClickUp ワークフローを構築して、各根本原因に対処するためのオーダーメイドのアクションステップを決定することができます。
4. 5つのなぜ
このシックスシグマツールは、プロセス問題の根本原因を特定するために「なぜ」を5回、または必要に応じて繰り返し問いかけることで、その原因を掘り下げていきます。
問題の診断に関連する最後の答えに対して「なぜ」と繰り返し質問することで、根本原因に近づきます。
ここでの目標は、症状や仮定の層をはがして、問題の根本的な原因を明らかにすることです。問題点が特定されれば、その問題に合わせた対策を立てることが容易になります。
たとえば、従業員の定着に問題があるとします。5つの「なぜ」の手法を用いて、問題の根本原因を特定します。
問題: 従業員の定着率が低い。
- 理由: 仕事のスケジュールが柔軟でなかった
- 理由:プロジェクトの範囲が明確ではない
- 理由:製品概要が時間通りに共有されなかった
- 理由:クライアント側の生産性の低下
- 理由:完全な製品情報を収集・共有するためのリソースの不足
これらの原因から、問題はクライアントが包括的な製品概要を時間通りに共有できないことに起因していることは明らかです。ワークフローの早い段階でこの問題に対処することで、従業員はプラン通りに仕事を進め、仕事の満足度を高めることができます。
このリーンシックスシグマツールは、問題の根本原因から症状を分離する際、シンプルさ、効率性、効果性を提供します。
このツールを使用する場合:5つのなぜは、根本原因の分析が必要な状況、特に問題が複雑で多層的な場合に最適です。機械の故障やプロセスの混乱の原因を理解するために、運用環境でこのシックスシグマツールを使用することを検討してください。
ClickUp の 5 Whys テンプレートを使用すると、チームでのコラボレーションが迅速になり、非効率性を解決するための繰り返し可能な手法を導入できます。プロセスの変動の根本原因を特定したら、チームメンバーに特定のタスクを作成して割り当て、問題解決にすぐに取り掛かることができます。
5. FMEA
故障モード影響分析 (FMEA) は、設計、製造または組み立てプロセス、製品、またはサービスにおけるすべての考えられる故障をリストアップするのに最適です。
これは、潜在的な障害点を発見し、早期発見によって企業が是正措置を講じることができるように設計されています。FMEA を使用すると、問題の影響度と発生の可能性に基づいて、問題の優先順位を付けることができます。
まず、分析するプロセスに関する知識を持つ部門横断的なチームを編成することから始めます。これにより、潜在的な失敗について複数の視点が導入されます。
分析対象とする製品、プロセス、設計、またはサービスを定義したら、各ステップまたはコンポーネントをリストアップし、障害が発生する可能性のある方法をマップします。これが障害モードです。
各故障モードは、その重大度 (S)、発生頻度 (O)、および検出可能性 (D) を反映してスコアが付けられます。リスク優先度番号 (RPN) は、次のように計算されます。
RPN = S × O × D
この RPN を使用して、製品の機能に最も影響を与えるものに基づいて、故障モードの優先順位を付けます。
このツールを使用する場合:新規または既存のプロセスリスク評価、特に製品やプロセスの立ち上げ前に適しています。自動車および航空宇宙業界では、将来の故障を防止し、信頼性を高めるために、設計および開発段階で広く使用されています。
ClickUp の FMEA リーンシックスシグマテンプレートは、予期せぬ非効率性を回避するために改善が必要なサブプロセスやコンポーネントを明確にします。さまざまなビューにより、リスクを重大度や頻度に応じて整理することができます。
6. カンバン
かんばんボードは、ビジネスプロセスを最適化するためのリーンマネジメントにおける強力な視覚化ツールです。ユーザーは、タスクを視覚化し、進行中の作業を制限し、フローを最大化して、プロセスの非効率性と業務効率を改善することができます。
まず、重要なビジネスプロセスをマップし、各プロセスを明確なフェーズに分類します。前者には、製品の配送や顧客オンボーディングなどの要素が含まれ、後者には「リクエストの受信」、「品質チェック」、「処理」などが含まれます。
各フェーズの列を含むカンバンボードを設定します。この視覚的なレイアウトにより、タスクの進捗状況を確認でき、ボトルネックを効率的に見つけることができます。
同時に処理できるタスクの最大番号 (WIP リミット) をメンションすることを忘れないでください。これは、障害を特定し、積極的に対処するために非常に重要です。
全体として、そのダイナミックなタスク管理により、プロセスフローに関するリアルタイムのフィードバックが明らかになり、すべての遅延が強調表示されます。このシックスシグマツールのアーキテクチャは、リソースの再割り当てによるプロセスの調整に役立ちます。また、プロセスステップを再定義して、非効率性を削減することもできます。
このツールを使用する場合:カンバンは、ソフトウェア開発や編集コンテンツチームで、プロジェクトの管理、ワークフローの調整、進行中の作業の視覚的なリミット設定を行う場合に適しています。
たとえば、ClickUp のカンバンボード機能を使用すると、ワークフローのフェーズを明確に視覚化し、進捗状況をリアルタイムで追跡することができます。これらの機能を Six Sigma のデータ駆動型アプローチと組み合わせることで、小規模および大規模プロセスのエラー防止に最適です。
ClickUp のカンバンボードテンプレートは、大きなタスクをより達成しやすいサブタスクに分割し、チームのキャパシティに関する洞察を提供します。これにより、タスクのサイクル期間を大幅に短縮し、リソースの ROI を最大化することができます。
7. パレートの法則
パレート図は、プロセスにおける問題や原因の頻度や影響を表す棒グラフの一種です。80/20 のパレートの法則によると、すべての問題の 80% は 20% の原因によって発生しています。
このチャートは、問題の原因のうち「重要な少数の原因」と「些細な多数の要因」を区別するのに役立ちます。これにより、影響の大きい問題から最初に取り組むことができます。
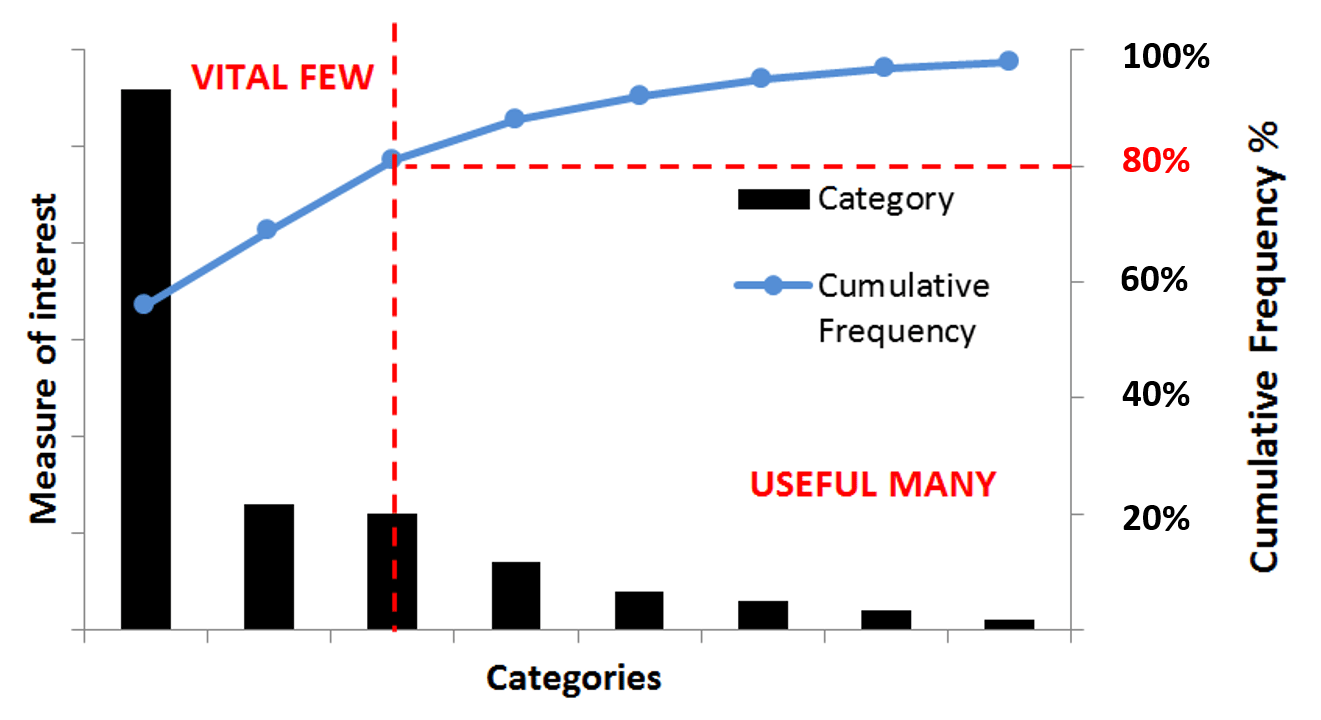
最初の 2 つのステップは、データの収集と分類です。問題が分類されたら、各カテゴリーの発生頻度を集計します。次に、発生頻度の高い順にカテゴリーをランク付けします。次に、各カテゴリーが占める欠陥または原因の総数の累積割合を計算します。
最後に、カテゴリをチャートの横軸に、頻度を縦軸にプロットします。
パレートチャートは、以下の点でビジネスプロセスの改善目標に役立ちます。
- 問題の測定と比較
- 重点領域の特定
- リソースの適切な配分
- 改善のための反復
このツールを使用するタイミング:ソフトウェア開発において、バグや機能の優先順位を、その発生頻度やユーザーへの影響度に基づいて決定するのに役立ちます。
8. タクトタイム
タクトタイムは、生産率と顧客の需要を同期させ、スムーズで継続的な業務フローを実現する基本的な概念です。
タクトタイムは、製品の需要に合わせて生産ペースを設定するのに役立ちます。タクトタイムを使用すると、生産効率の向上、無駄の削減、在庫コストの削減が期待できます。
タクトタイム = 総生産可能時間 / 顧客需要
たとえば、工場が 1 日 960 分稼働し、顧客の需要が 1 日 320 ユニットの場合、タクトタイムは次のようになります。
タクトタイム = 960分 / 320単位 = 3分 / 単位
ビジネスプロセスの改善では、タクトタイムは、作業負荷のバランスを調整したり、生産ラインを再構成したりして、業務のスピードを調整するのに適しています。生産メトリクスを監視して、ステップがタクトタイムを満たしていないかどうかを確認することができます。
このツールを使用する場合:このツールは、家電製造業界で最も効果的です。生産速度を市場の需要に合わせて調整し、過剰生産を回避し、在庫コストを削減するのに役立ちます。
9. ポカヨケ
「ミス防止」を意味する日本語の「ポカヨケ」は、ミスを欠陥になる前に発生源で回避および修正するためのフェイルセーフ機能をプロセスに組み込む手法です。このシックスシグマツールを使用すると、エラーの発生を事実上不可能にすることができます。
ほとんどのシックスシグマ手法と同様に、まずプロセスを分析し、一般的なエラーポイントを見つけます。これらは、忘れや誤った仮定などの人為的なミスが原因である可能性があります。
さらに、プロセスの設計、インターフェース、または従業員とプロセスの相互作用によって生じるエラーを分析します。
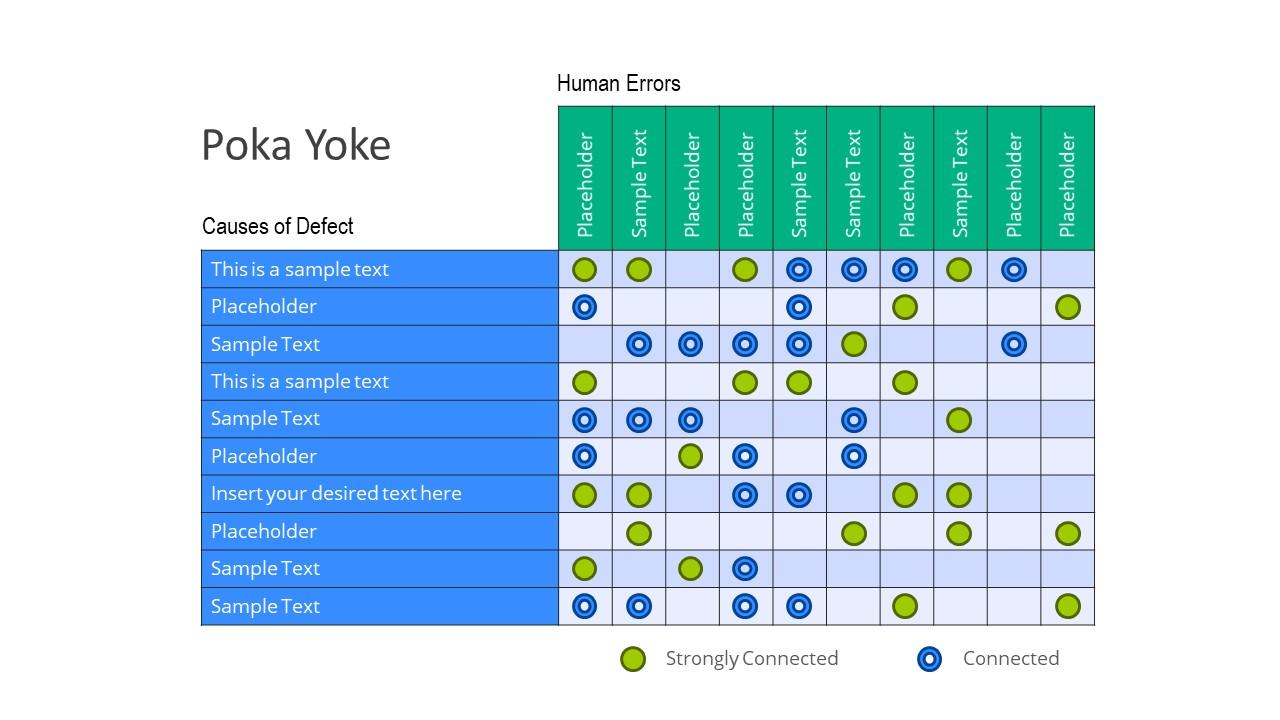
最も重要なのは、エラーを未然に防止したり、エラーが発生した場合にすぐにそれを明らかにするポカヨケソリューションを開発することです。ポカヨケには、主に 3 つのタイプがあります。
- お問い合わせの種類:物理的特性をテストして製品の欠陥を特定する
- 固定値タイプ:特定の数の移動またはアクションが確実に実行されるようにします。
- 動作ステップ(シーケンス)タイプ: アクションの適切なシーケンスをチェックし、正しい順序で、漏れなく完了しているかどうかを検証します。
追加のプロセス改善テンプレートを試して、上記の 2 つの手法をマージし、A/B テストを実行することができます。
このツールを使用する場合:自動車製造で広く使用されているポカヨケは、部品が正しく取り付けられていることを確認し、組み立てエラーを防ぎ、製品の品質を向上させます。
10. SIPOC
これは、サプライヤー、インプット、プロセス、アウトプット、および顧客を表す頭字語です。SIPOC は、チームが状況、範囲、および関与する主要な利害関係者を視覚化するのに役立ちます。このリーンシックスシグマタイプを使用して、その後の分析や変更が的確で関連性のあるものになるようにしてください。
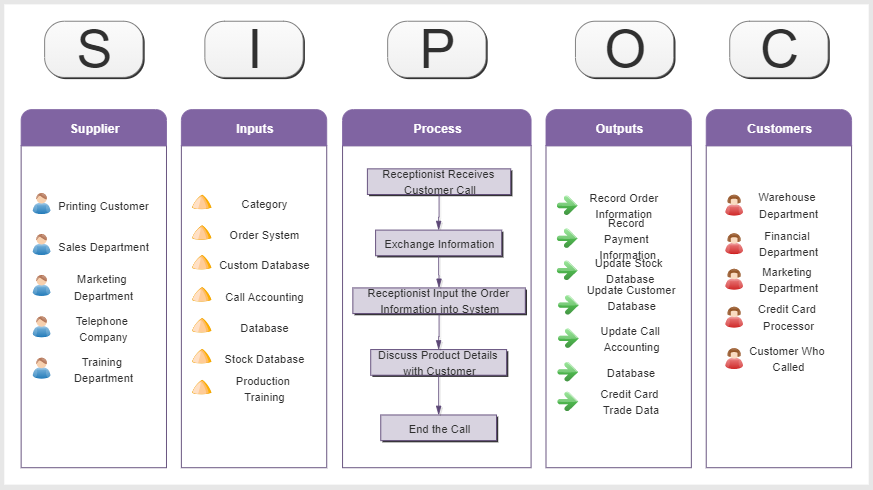
改善したいプロセスを 5 から 7 つの大まかなステップで説明してください。次に、SIPOC の 5 つの要素をマップにまとめます。
- サプライヤーは、プロセスにインプットを提供します。これは、社内のチーム、社外のベンダー、システムなどです。
- 入力には、プロセスの実行に役立つ資料、情報、その他のリソースがリストされます。
- このプロセスには、タスクの開始から終了までの重要なステップが含まれます。これは詳細なプロセスマップではなく、概要として作成してください。
- アウトプットは、プロセスによって生み出されるものを定義します。これらは、プロセスから得られた結果または成果物です。
- 顧客とは、あなたの成果物を受け取る人です。顧客は、組織の内部または外部のいずれにも存在する場合があることに注意してください。
サプライヤーから顧客へのプロセス全体のフローを説明する、シンプルな SIPOC テーブルや図を作成することができます。さまざまな SIPOC 図テンプレートを試して、いくつかのユーティリティスタイルをよりよく理解してください。
このツールを使用する場合:このツールは、ホスピタリティ業界や銀行業などのサービス業界で、顧客サービスプロセスをマップする場合に適しています。顧客体験に影響を与える要素を特定するのに役立ちます。
ClickUp の SIPOC テンプレートを使用すると、冗長なタスクに時間やリソースを無駄にすることなく、サプライチェーンの体系的なプロセスを設定できます。サプライヤー、プロセス、入力、出力などの個別のビューを通じて、チームにプロセスの範囲を通知し、非効率な部分をより迅速に特定するのに役立ちます。
オペレーショナルエクセレンスへの道
これらの Six Sigma ツールは、ビジネスやチームの業務改善アプローチを戦略的に強化します。個々のプロセスを最適化するだけでなく、チームに継続的な改善というやりがいのある文化を浸透させることもできます。
これらのツールを日常業務に組み込むことで、組織は生産性と品質の持続的な向上を実現できます。どこから始めればよいか迷っている方は、ClickUp にSix Sigma テンプレートを統合して、ビジネスプロセスの信頼性を高め、ミスを減らしてみてください。
今すぐ ClickUp に登録して、継続的な改善の文化を推進しましょう。
よくある質問
1. シックスシグマツールとは何ですか?
シックスシグマツールは、エラーを最小限に抑えることでビジネスプロセスを改善します。その中には、フィッシュボーン図(根本原因を特定するため)、パレート図および FMEA(重要な改善領域をターゲットにするため)、5 つのなぜ(問題の原因を掘り下げるため)、管理図(変動を監視するため)、PDCA(反復的な計画のため)などがあります。
2. シックスシグマはリーンツールですか?
シックスシグマツールは、ビジネス効率の向上を目的とするリーンとよく関連付けられます。リーンは、無駄を排除し、生産プロセスのフローを改善して効率を高めることに重点を置いています。一方、シックスシグマは、変動や欠陥を減らして品質を向上させます。
3. シックスシグマは品質管理ツールですか?
はい、シックスシグマは基本的に、プロセスのばらつきを減らし、生産品質を向上させるための品質改善ツールです。統計ツールを使用して、100 万回の機会あたり 3.4 件以下のプロセス欠陥レベルを達成し、維持することができます。