Automations
Automate handoffs, status updates, and more.
Automatically assign tasks for each stage of your pipeline, trigger status updates based on activity, and switch priorities to alert your team on where to focus next.
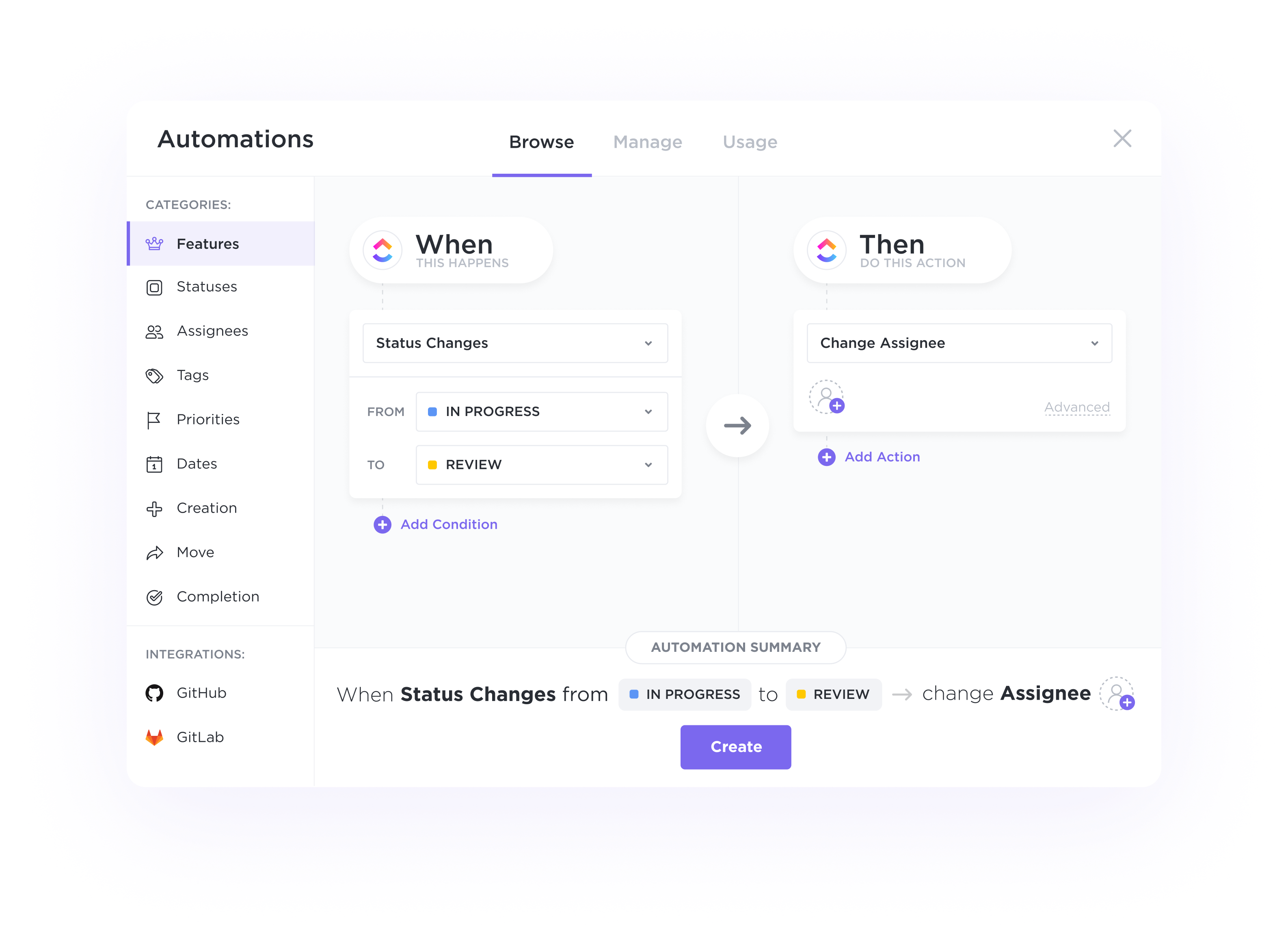
Gantt Charts
Optimize your workflow and enhance efficiency with ClickUp's CRM system customized for Quality Control Technicians. Streamline your processes, track tasks, and manage client interactions seamlessly all in one place. Try ClickUp today and take your customer relationships to the next level.
Free forever.
No credit card.
Trusted by the world’s leading businesses
Automations
Automatically assign tasks for each stage of your pipeline, trigger status updates based on activity, and switch priorities to alert your team on where to focus next.
Email Management
Eliminate silos and fast-track communication by integrating your emails with ClickUp. Collaborate on deals, send project updates to clients, and onboard customers with a single email hub.
CRM software provides tools such as customizable forms and fields, automated notifications, workflow management, and reporting capabilities to help quality control technicians track and manage defects and non-conformances effectively.
CRM software can generate reports and analytics that help quality control technicians identify trends and areas for improvement in the quality control process.
CRM software integrates with quality control tools and systems by centralizing quality-related data, automating workflows, providing real-time insights, and enabling collaboration among quality control technicians.
Gantt Charts